Lincoln Electric Introduces the Easily Programmable Fab-Pak Cobot Guru Robotic Collaborative System
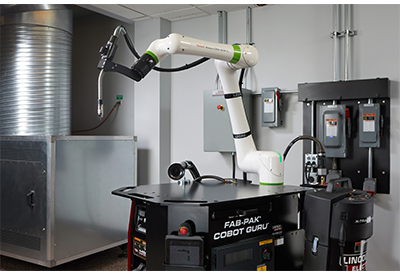
May 28, 2021
The new Fab-Pak Cobot Guru system from Lincoln Electric automates the highest mix of different products while providing even non-welders with the ability to easily program it for increased productivity in even the smallest of workspaces.
It comes standard with the following components:
- – FANUC CRX 10iA with tablet-based teach pendant
- – Integrated pushbutton torch control
- – AutoDrive 4R100 Wire Feeder
- – Power Wave R450 Welder
- – Fixed welding table
- – Heavy-duty casters
- – Stabilizing kickstand
- – Utility drawer and tablet tray
The Fab-Pak Cobot Guru system’s dual-action, pushbutton interface and intelligent torch system allow operators to reduce cumbersome programming. Users at any level of expertise, including those with zero robotics experience, can record weld points with the push of a button and teach the cobot arm directly at the torch.
Operators can simply move the cobot’s arm with their hand to the start and finish waypoints. The cobot does the rest by calculating weld settings and parameters using the Lincoln Electric Arc Welding plug-in and then fluidly and automatically welds the part.
The system also features a new tablet teaching pendant that uses Icon-Based Timeline Programming. This feature reduces the programming learning curve by making it more relatable to an app-based generation of welders. Available upgrades include integrated fume extraction, a dual-zone, manual turntable system, and flexible tooling kits.