Why ANCA’s AIMS AutoComp Is Your Secret Weapon for Effortless Manufacturing of Best Quality Tools
May 29, 2024
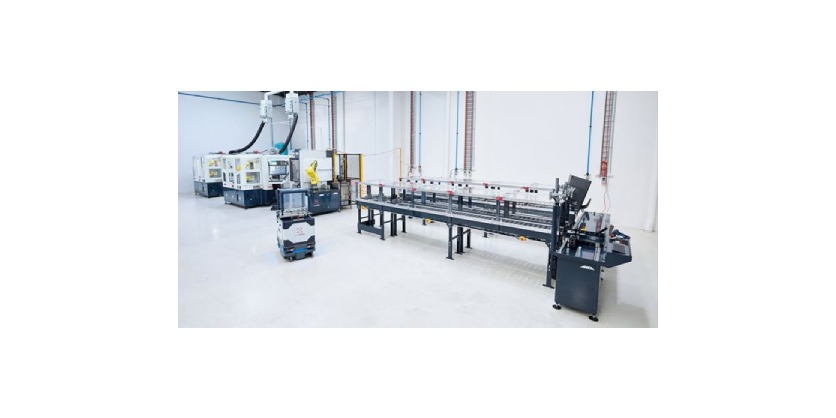
An industry first solution unique to ANCA, AIMS AutoComp ensures consistent quality by keeping your tools within tolerance throughout unattended grinding processes
ANCA Integrated Manufacturing System (AIMS) is a ground-breaking solution that is transforming the tool manufacturing industry. With its modular and flexible ecosystem, AIMS can be customised to meet your specific needs, giving you unparalleled control and adaptability.
As the saying goes, “You can’t manage what you don’t measure.” AIMS empowers you with comprehensive reports and intelligent insights using machine learning technology. By gaining full visibility into every aspect of your operations, you can focus on continuous improvement and drive optimal performance.
With AIMS enabling 24/7 unattended operation, reliable and accurate dimensional tolerance control becomes essential. AIMS AutoComp is a key component of AIMS and achieves this goal by keeping your tools within tolerance throughout unattended grinding processes over extended periods.
AIMS AutoComp is an industry first solution unique to ANCA
An industry and world-first, it lifts tool measurement and compensation during batch grinding to another level, releasing a human operator that would normally be required to perform this task. This feature contributes to direct labour savings and driving cost per tool down for manufacturers.
The AIMS AutoComp capability is constantly expanding with new tool geometries being added, and traceable results in accurate measurements with no ongoing costs thanks to automation.
A closed loop solution that guarantees consistent quality
When combined with AIMS AutoFetch, a mobile robot which transfers the physical tools between stations, AIMS AutoComp forms an autonomous and closed-loop measure and compensate solution. This unique ANCA offering guarantees reliable, error-free, and round-the-clock tool batch management, ensuring your tools consistently meet the required tolerance levels.
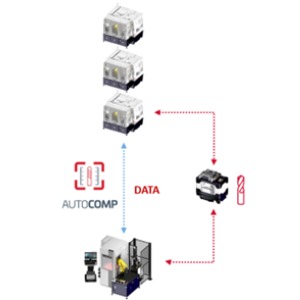
AIMS offers a seamless and user-friendly experience through familiar tools like the enhanced Measurement Wizard. Whether you’re dealing with small or large production batches, AIMS adapts effortlessly to meet your requirements.
The AIMS recipe provides sequential instructions to the AIMS cell on the necessary processes and their order. For instance, the recipe may include parameters for grinding, measurements, measurement frequency, laser marking, edge preparation, and washing. You can customise it up according to your individual needs.
The AIMS Server acts as a repository for all your recipes, ensuring easy access and execution whenever needed. If you already have a Manufacturing Execution System (MES) in place, the AIMS Server seamlessly interfaces with it, allowing you to call upon stored MES recipes or tool files as required. AIMS Server is designed with flexibility in mind.
How does AIMS AutoComp operate?
Batch setup behaviour
During the setup of the grinding process, you can determine how the system operates. You can choose to measure the first few tools individually one-by-one using ZOLLER before grinding the next tool. If compensation is required, it is applied to the next tool before grinding. In this way you have a guarantee the batch stabilises before switching to fully automatic batch grinding mode.
Batch grinding behaviour
This phase involves determining the frequency of measurements in the external measurement machine (e.g., ZOLLER) during batch grinding. Again – you are in driver’s seat and decide on behaviour of your AIMS cell.
OD Control with AIMS AutoComp
AIMS AutoComp uses both ZOLLER and LaserUltra for OD control during the grinding process. The collaboration between the ZOLLER and LaserUltra optimises the grinding cycle and enhances the quality of your tools.
Unattended tool measurement and compensation workflow
When AIMS AutoComp works in conjunction with AIMS AutoFetch, it enables a fully unattended tool measurement and compensation workflow. This workflow leads to substantial labour savings, typically exceeding 60% compared to traditional systems. Accurate, on-time, and frequent measurements contribute to reducing scrap. Depending on your AIMS AutoComp settings, you can expect a scrap reduction of 40% to 60%.
To illustrate the effectiveness of the solution, consider the following scenario of 10 tool and cutter grinding machines running 24/7 in three shifts, grinding 6mm tools with a cycle time of 360 seconds per tool. In this case, every 15th tool needs to be measured using the ZOLLER.
Over a 24-hour period, it would require measuring 160 tools. In a standard operation, an operator would manually pick up these tools from the grinder, transfer them to the ZOLLER, clean them, measure them, transfer the measurement values back to the grinder, and manually replace the tools on the pallet. Assuming a conservative estimate of 10 minutes per tool for these activities, it would amount to a total of 26 worker-hours to complete this task accurately.
By implementing AIMS AutoComp and AIMS AutoFetch for material transfer, this entire process happens automatically and error-free, resulting in saving 26 worker-hours and eliminating the potential for human errors.
AIMS AutoComp settings in ToolRoom and AIMS Server
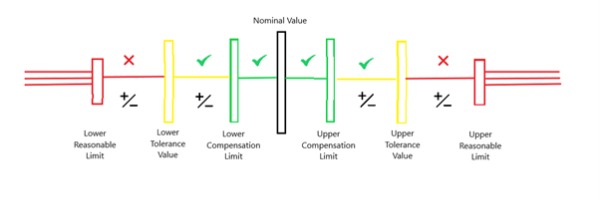
The example below showcases a three-flute endmill. In the ToolRoom software, you can establish a list of geometries for the AIMS AutoComp that will enable automatic ZOLLER measurement and parameter compensation. You have the flexibility to define your own tolerance bands, which will be considered during the unattended grinding process. The images below provide an illustration of this:
The system’s flexibility is evident, allowing you to customise the behaviour of AIMS AutoComp according to your specific requirements and preferences.
The image below shows the view of the Measurement Wizard for the example tool, which demonstrates the parameters available for measurement and compensation. Here, you can access a comprehensive list of parameters that can be measured and compensated for the example tool. This list is constantly expanding to accommodate various tool types and geometries.
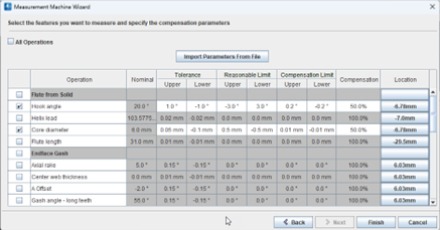
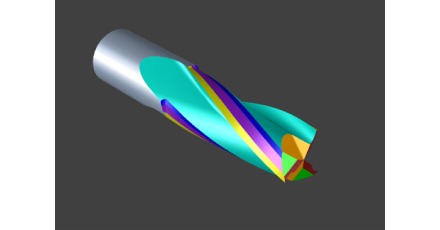
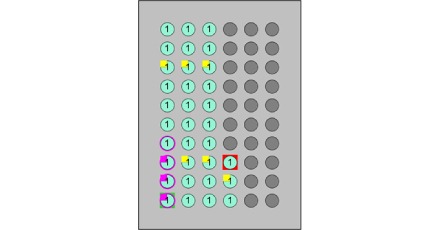
Speak to the ANCA team to discuss the steps you need to take towards a fully automatic, lights out manufacturing solution.
Related Story
ANCA’s AIMS Selected as Finalist for 2024 Manufacturing Leadership Council Awards
The Manufacturing Leadership Council (MLC) is the digital transformation division of the National Association of Manufacturers and, as part of its mission, annually seeks world-class manufacturing companies and key individuals who contribute to the technology. 2024 marks the 20th anniversary of this premier awards program.