Q&A With HELU: Ferrules
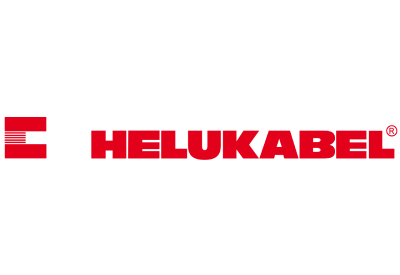
October 28, 2022
A popular trend that is growing in the US market is the use of ferrules, also known as end sleeves, to terminate single and multi-conductor wires, e.g. in the terminal blocks within a machine’s control panel. For US equipment manufacturers that export to Europe, using ferrules is a requirement toreceive CE certification so that a company can do business within the European Union. Regional Sales Manager Bob Wells takes some time to answer a few questions he hears in the field about this cable termination technique.
Q: What is a wire ferrule?
A: A wire ferrule is a type of pin terminal used to prevent the unraveling of stranded wire and to increase the stability of electrical connections. It is usually made out of tin plated copper. This tube or barrel is placed over a section of stranded wire extending from stripped insulation,then compressed with a crimping tool to hold the strands together.
Q: What are some advantages of using ferrules compared to terminating stranded conductors?
A: Using ferrules enables users to take advantage of the features of stranded wire without the problems caused by a bare wire connection. Every strand of a wire can now be inserted into a connector, without any strands fanning out to the sides upon insertion. The seconds required to apply a ferrule to the wire ends are more than made up by the ease of insertion. Once crimped, the bundle is converted into what acts as the end of a solid conductor wire. Ferrules greatly reduce the contact resistance between the wire and connector and minimize oxidation in the strands because of the limited air space between them. Finally, ferrules provide strain relief which prevents conductor breakage due to bending and vibration.
Q. What are some of the types of ferrules available in the market?
A: There are three different types of wire ferrules: insulated, non-insulated and twin/dual/double.
- A) Insulated ferrules have a plastic-colored PVC collar or shoulder over the tin plated copper barrel. These ferrules are easier to work with, especially on smaller conductors, where the shoulder helps to guide the individual wire strands into position.
- B) Non-insulated ferrules do not have a shoulder. Without the shoulder, it can be difficult to install because the shoulder is not there to guide the conductor strands as it’s very similar to threading a needle. However, when space is limited, non-insulated ferrules are popular.
- C) Twin/dual/double wire ferrules have a larger insulated collar that allows you to insert two wires of the same size into the ferrule tube to be crimped tightly and securely using a properly sized ferrule. This provides an efficient connection of multiple wires in the same terminal clamp or simplifies wire jumping between terminal clamps.
Q: What size ferrule should be used?
A: The selected ferrule should match the cross section of the wire being used. For example, a 1.5 mm2 (AWG 16) ferrule means it will be connected to a 1.5 mm2 (AWG 16) wire. If a double ferrule is used installers need to be careful as two AWG conductors may need a larger ferrule compared to using two metric-sized conductors. If two AWG wires of the same size are being used, then the correct ferrule size is determined by increasing the total wire size by three steps. For example, two AWG 20 wires, which each have a cross sectional area of 0.519 mm2 each, are equivalent to a single AWG 17 (1.04 mm2), so a 1.5 mm2 (AWG 16) capacity ferrule should be specified. While it’s theoretically possible for two AWG 20 wires to fit into a 1.0 mm2 capacity ferrule, it is likely to be a tight fit and more challenging if one wants to efficiently terminate the wires.
Q: Why do insulated ferrules have different color shoulders?
A: The shoulder color on insulated ferrules identifies the matching conductor size. There are three different standards as shown below. The colors used can be the user’s choice unless specified. However, blue for AWG 14, black for AWG 16, and red for AWG 18 are typically the color/size used in the US market.
Q: Why are there different lengths of ferrules?
A: Different types of connectors require different ferrule lengths, i.e. barrel length, which can range from 0.24-1.26 in (6-32 mm) depending on the ferrule size. As an example, a recessed PCB terminal may require a longer barrel to properly terminate, whereas a DIN rail terminal block in a control panel may just require a standard-length barrel, which is typically 0.5 inches (12 mm).
Q: Is there a special tool required to properly install ferrules?
A: Yes, there are specialized tools one should use to properly cut, strip and crimp the ferrules to ensure proper contact with the wire. You do not want to use pliers as this will not provide a uniform crimp around the wire. Based on where the cable or wire is being terminated, either at an assembly/harness shop or on-site, there are a variety of handheld and electric bench-top machines to process the cable and wires quickly and efficiently.
Source