Reducing Total Cost of Ownership in Pumping Systems
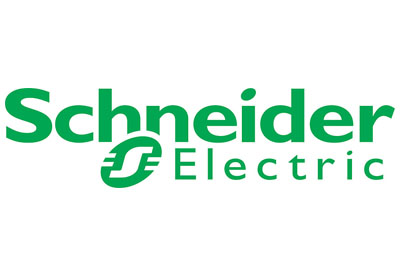
November 1, 2017
by Lionel Gaudrel and Arnaud Savreux
Wherever pumping systems are present–in environments such as buildings and water / wastewater and oil and gas facilities–energy consumption exerts a major influence on cost. Despite the fact that electrical energy cost represents 40% of the total cost of ownership of pumping systems, many organizations fail to introduce the proper steps to leverage cost reduction through efficiency improvements. To solve this dilemma, the following major barriers need to be recognized and addressed: Lack of proper metrics – Energy efficiency has traditionally not been used in assessing performance. In most organizations, the responsibilities of energy procurement and efficient operations are separate and consistent / standardized metrics are not utilized. Knowledge gap – A lack of awareness in energy efficiency opportunities is prevalent and, as a result, potential savings and other benefits are missed. Fear of investment – Operations personnel often struggle to present attractive large or even small investments to their finance organizations.
This paper demonstrates how deployment of an energy management plan, with limited investment, can provide reductions in pumping systems TCO while maintaining sustainability objectives. Any sound energy plan should take into account the following three steps: 1. Energy efficiency management 2. Asset management 3. Energy cost management For the purposes of this paper, the scope of a pumping system will be defined as encompassing all related elements starting from the point of the electrical utility connection down to the point of end use. This paper will illustrate how energy management best practices can result in a 20% reduction in TCO and a return of investment (ROI) within 24 months.
Energy efficiency is now a global high priority for both industrialized and emerging countries. The Rio conference and Earth Summit of 1992 and the Kyoto Protocol of 1997 resulted in the signing of a global treaty that sets binding targets for reduction of greenhouse gas emissions. The International Energy Agency (IEA) and various governments and non-governmental organizations (NGOs) agree that the reduction of CO2 emissions and the resulting energy savings can be achieved through the deployment of energy efficient products and systems. The challenge, however, is that the nature of production in industrial environments is in a constant state of flux. Production cycles, for example, are influenced by variables such as market demand, weather, and local regulations. As a result, factory and building operators need to understand how and when energy is used in order to minimize consumption and related costs. The pump system energy management approach discussed in this paper will review the nature of efficiency loss not only for individual components within the system, but also for the system as a whole, integrated entity. In pumping systems, most inefficiency comes from: A mismatch between the pump deployed and the actual system requirement (i.e., undersized or oversized) The improper use of throttling valves and damper technologies to control the flow of liquids These two elements imply that the way pumping systems are controlled plays a major role regarding how efficiency can be improved. Control systems themselves are composed of both hardware and software components. On the hardware side, variable speed drives are a primary enabler of high efficiency performance.
Read the full repot here: https://download.schneider-electric.com/files?p_enDocType=White+Paper&p_File_Id=1165518381&p_File_Name=998-2095-02-19-14AR0_EN.pdf&p_Reference=998-2095-02-19-14AR0_EN