SICK: Motor Feedback Systems Rotary HIPERFACE STS
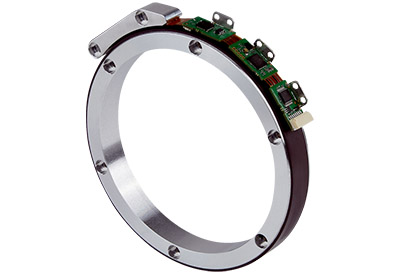
October 28, 2021
The trend toward highly dynamic drive systems has clearly strengthened in recent years. The STS absolute motor feedback system ensures maximum flexibility and precision when measuring the position and speed of hollow shaft motors and direct drives. The non-contact magnetic measurement principle works without causing wear. A scalable measurement system, the STS adapts to different hollow shaft diameters of the application. In addition, the STS scores points with its particularly flat design and compact dimensions, making it the ideal solution for tight installation situations. Thanks to the standardized HIPERFACE interface, the motor feedback system can be easily integrated into nearly any industrial environment.
At a glance
- – Non-contact and bearing-free measurement of speed and position
- – Resolutions up to 12,672 measurement steps per revolution
- – Accuracy of up to ± 0.05°
- – For hollow shaft diameters from 30 mm to 500 mm
- – Reliable in harsh ambient conditions
- – HIPERFACE interface with extended type label
- – For internal and external rotor motors
Your Benefits
- – Flat, compact motor design due to maximum flexibility and installation of the motor feedback system with millimeter precision
- – Increase in dynamics and PSDI times due to the elimination of mechanical components, such as belts
- – Bearing-free technology maximizes the service life and machine availability of the overall system
- – Use of hollow shafts to feed through hoses and cables saves valuable installation space
- – Safe Motion for safe monitoring of machine movements and optimal interaction between man and machine
Advantages
More application possibilities – with the STS motor feedback system
The compact STS absolute motor feedback system comprises a read head and a magnetic ring and ensures maximum flexibility and precision when measuring the position and speed of direct drives. The non-contact magnetic measurement principle works without causing wear. Thanks to the standardized HIPERFACE interface, the STS can be integrated into virtually any industrial environment. Challenging environmental influences such as high air humidity or fine dust have no impact on either the measurement quality or the service life of the system. The absence of wear and tear parts also maximizes the service life and guarantees the high availability of the overall system. This enables the machine-side maintenance intervals to be significantly reduced.
More application possibilities – with the STS motor feedback system
The compact STS absolute motor feedback system comprises a read head and a magnetic ring and ensures maximum flexibility and precision when measuring the position and speed of direct drives. The non-contact magnetic measurement principle works without causing wear. Thanks to the standardized HIPERFACE interface, the STS can be integrated into virtually any industrial environment. Challenging environmental influences such as high air humidity or fine dust have no impact on either the measurement quality or the service life of the system. The absence of wear and tear parts also maximizes the service life and guarantees the high availability of the overall system. This enables the machine-side maintenance intervals to be significantly reduced.
Perfect for use where others reach their limits
Being a scalable measurement system, the STS can be perfectly tailored to the hollow shaft diameter of the application. Device variants in one of seven standard internal diameters of 30 mm to 230 mm are available for this purpose. With these standard sizes, the system covers the typical diameters of commonly used industrial direct drives. In addition to this, custom diameters for millimeter precise installation up to a hollow shaft diameter of 500 mm can be implemented. The design of the read head can also be tailored to the customer’s requirements, thereby enabling the STS to be integrated into even the tightest installation spaces. Thanks to the flexible technology, two different motor concepts are supported: internal rotor motors as well as external rotor motors – the choice is yours with the STS.
Ultraflat design for compact applications
Every millimeter often counts for applications in the area of robotics as well as in handling solutions. The STS motor feedback system with its especially flat design and compact overall dimensions excels in this regard: With an installation height of just 12.5 mm, the STS offers the ideal solution for tight installation situations. Significantly more compact machines – with no loss in precision – can be designed using a direct drive with a high-performance system. Because these do not have any wear and tear parts like belts or couplings, the overall maintenance costs are markedly reduced. The hollow shaft present can also be used to pass through cables, hoses or wires.
Fields of applications
- – Ideal for integration into servo hollow shaft motors
- – Direct drives, e.g. torque motors
- – Rotational and swivel axes, e.g. extruders
- – Robot joints
- – Drive systems in the field of AGVs and mobile platforms