PC- and EtherCAT-Controlled for Parts Sorting with 100% Inspection
April 28, 2025
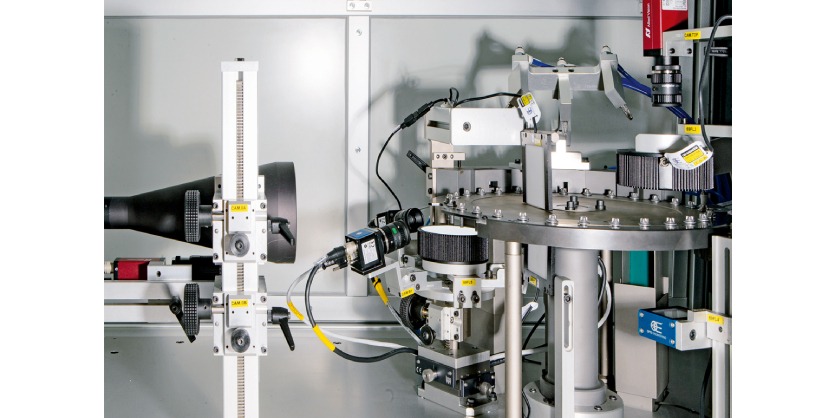
PC-based control and EtherCAT in a new generation of sorting machines
Dimac designs and develops innovative solutions for 100% inspection of fasteners and small metal parts. The company has identified EtherCAT and PC-based control from Beckhoff as the mainstays of the next generation of sorting machines, which will make the La Mille concept machine – the thousandth Dimac project – even faster, more powerful, and open to the integration of additional systems.
Dimac srl, based in Tortona, Italy, states that it is one of the few companies in the world to specialize in manufacturing high-speed machines for 100% sorting and quality control of small metal parts and fasteners. “Fast is up to 1200 parts per minute,” explains Guido Noce, general manager of Dimac.
With an export share of over 70% and having installed more than 1;000 machines, the company supplies the most important American and European manufacturers of fasteners – with the automotive sector as one of its most important markets. In addition to screws, nuts, and washers, Dimac machines are used to inspect a wide range of components. These range from motors, airbags, and other electromechanical components to jeans buttons, the tiny screws used in glasses, and chain links.
High flexibility and speed
The variety of different parts and quantities requires a flexible and powerful automation solution for the sorting and inspection systems. This is because the control technology ultimately determines the speed and reliability of the machines. With its La Mille concept, Dimac initiated an ambitious project, with the aim of completely redesigning the existing automation solution in order to further enhance the performance and reliability of the machines.
“The reliability of our machines is the result of a concept based on a single piece of software that has been constantly updated with variants and new functions,” explains Guido Noce. Over the years, the many extensions to the previous solution had led to limitations in the operation and management of the software. After 25 years of overlapping software layers, it was time to make a new technological leap.
“When we conducted a market analysis among automation providers, we found that PC-based control from Beckhoff and EtherCAT were the best for fulfilling our needs,” emphasizes Enrico Ottaviano, engineering manager at Dimac. Guido Noce adds: “With La Mille, we want to comprehensively test the best that the market currently has to offer, in our view. The aim is to create an automation platform that will shape the next generations of Dimac machines.”
Performance and openness were the deciding factors
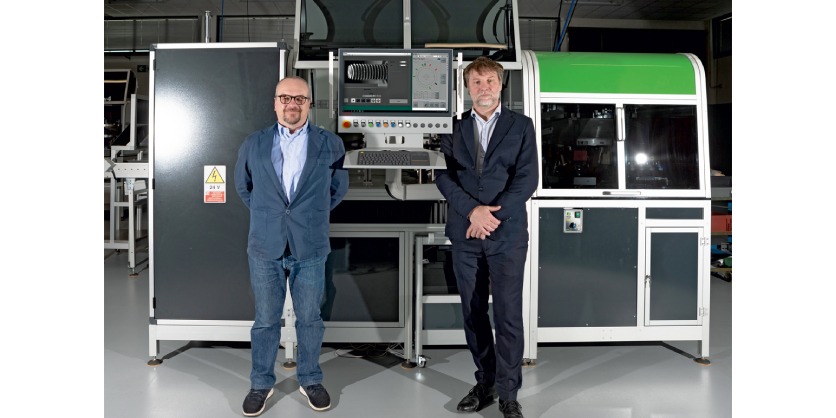
“We chose PC-based control from Beckhoff and EtherCAT primarily because of their openness and performance,” emphasizes Ottaviano. He was looking for a solution that did not prescribe a specific topology or tie the company to one supplier or a limited group of manufacturers. The open EtherCAT protocol and the many providers of corresponding masters, devices, actuators, and solutions fulfill this requirement.
In addition, the cycle times and update intervals of the decentralized peripherals needed to be significantly shorter than before. With regard to future developments, the aim is to reduce cycle times from 10 ms to around 1 ms. Guido Noce comments: “Even during the first tests, we realized that we could achieve the required performance with the high-performance EtherCAT protocol.”
Another important aspect was the ability to use open, standardized software and development environments such as IEC 61131-3. “We chose the Beckhoff TwinCAT software system precisely because of these properties,” adds Ottaviano. Dimac uses a CX5240 Embedded PC with an Intel Atom® processor with 1.6 GHz clock frequency (quad-core) as the controller; another industrial PC is currently being used for the image processing application. In the first phase, the project team wanted to ensure that image processing was not subject to any external influences.
Added value for end users too
For the machine end user, the La Mille control concept means higher sorting system speeds plus additional inspection criteria. “Our solution increases productivity, the number of stations, and the number of inspections that our machine can perform in the future,” says Noce. In addition, the openness of EtherCAT enables further components to be integrated. Users also benefit from the significantly improved user-friendliness based on TwinCAT HMI, e.g., for diagnostics and configuration. In addition, Dimac integrates the image processing software into the visualization and can therefore combine all machine functions on one Beckhoff Control Panel.
Inspections during production
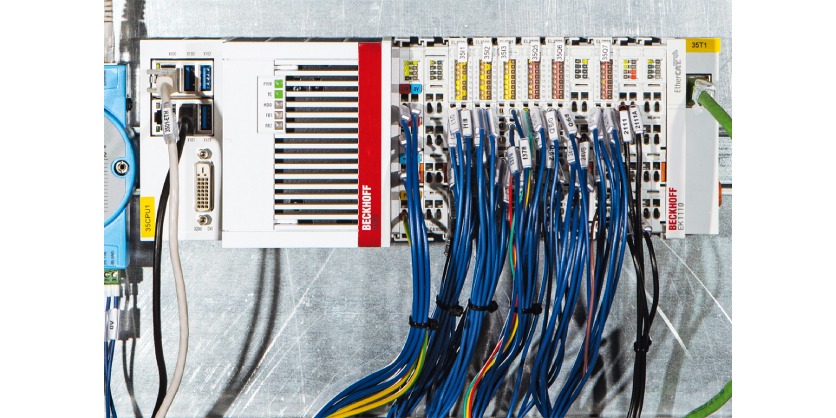
The 100% inspection and sorting of parts normally only takes place after production. In the production process itself, the most important parameters of a component are still measured manually and spot-checked in the laboratory. However, there is growing interest among manufacturing companies in integrating the data from sorting machines into inspection processes during production and using the objective and reliable data for continuous quality improvement and predictive maintenance.
Dimac is already working on integrating cobots, linear axes, and transport systems into its machine concept in order to replace the classic inspections operators carry out using plug gauges and other types of gauge with automated spot checks. Guido Noce comments: “We see PC-based control and EtherCAT as key technologies for these applications, which, previously, we have often been unable to implement due to excessive development costs.” PC-based control provides the necessary functions in an integrated system: control, image processing, motion, safety, human-machine interface, connectivity, and interoperability.
Enrico Ottaviano and his team are assisted by the Beckhoff support team. “We are very satisfied with the technical support in terms of technical expertise and response times. Using EtherCAT and PC-based control as the automation architecture will take Dimac’s new generation of machines to a new level in terms of performance, reliability, and data analysis capability,” emphasizes Ottaviano.
More Information
Related Story
Control Cabinet-Free Automation as a Game Changer in Machine and System Engineering
“The MX-System is changing the face of design and installation in the world of machine building,” explains Ludger Martinschledde, Managing Director of Schirmer Maschinen GmbH. In its initial use in a system for processing profiles, the pluggable system solution for control cabinet-free automation from Beckhoff ticked all the boxes in every project phase, from planning and design through to installation and commissioning.