MagnaShear Maintenance-Free, No-Adjustment Brakes Eliminate Downtime Featured in EASA Booth #730
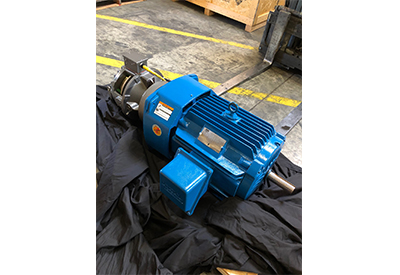
March 25, 2021
Force Control Industries will feature their MagnaShear maintenance-free, no-adjustment brake that virtually eliminates motor brake downtime. The MagnaShear motor brake employs oil shear technology, providing longer service life in demanding applications like the frequent start/stop cycles seen on cranes, hoists, winches and other equipment. Proven oil shear technology transmits torque between lubricated surfaces – thereby eliminating wear on friction surfaces. A patented fluid recirculation system dissipates heat – eliminating heat build-up which is the most common problem in dry braking systems. Elimination of the wear significantly increases service life and virtually eliminates adjustment which also elongates maintenance intervals. In addition to cranes, winches and hoists, they are ideal for applications where the motor is reversed each cycle such as loader/unloader conveyors, rail car spotters and dumpers, ship and rail car loading conveyors, trippers and pallet return conveyors.
The oil shear technology also provides a smooth “cushioned” stop which reduces shock to the drive system, further extending service life of downstream components.
The totally enclosed MagnaShear brakes are impervious to moisture, dirt and dust that is common in concrete block plants as well as asphalt shingle manufacturing, coal, bulk materials handling, forest products manufacturing, and more.
How Oil Shear Works
Unlike dry brakes, oil shear technology includes a layer of automatic transmission fluid between the brake disc and the drive plate. As the fluid is compressed, the fluid molecules shear – thus imparting torque to the other side. This torque transmission causes the rotating discs to decelerate against the stationary plates bringing them down to stop. Since most of the work is done by the fluid particles in shear, wear is virtually eliminated. Elimination of wear also eliminates the need for adjustments which are common for dry braking systems.
In addition to transmitting torque, a patented fluid recirculation system helps to dissipate heat which is the major problem with traditional dry brakes. Along with heat removal and torque transmission, the fluid serves to continually lubricate all components of the oil shear brake, elongating their service life. MagnaShear brakes with oil shear technology provide significantly longer service life, characterized by virtually maintenance-free operations.
Suitable for a Wide Range of Motor Sizes
These proven motor brakes are available to accommodate a wide range of applications. Spring set torque ratings from 3 to 1250 foot-pounds are available. MagnaShear motor brakes are available in multiple torques for the same motor frame.
MagnaShear motor brakes feature “quick mount” features for quick and easy mounting to drive motors in NEMA frame sizes 56 to 449. They are shipped ready to install, with no assembly or adjustments required. They are also available pre-mounted on a motor for severe duty applications. MagnaShear motor brakes can be furnished to fit a NEMA or IEC frame motor, as a complete motor and brake assembly, or to mount on a machine frame or other special mounting configuration.
These proven motor brakes are totally enclosed from outside contaminants, with seal integrity for harsh and washdown environments. A modular design /assembly allows for ease of servicing and maintenance.
For more information, visit www.forcecontrol.com.