Looking Back at Electric Motor Use in Factories, Advancements in 1889
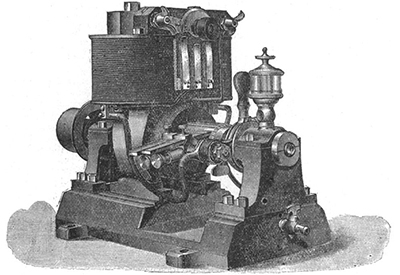
New Type of C & C Motor (110V)
July 16, 2019
The other day I came across an interesting article that takes us back to some early innovations regarding the use of electric motors in manufacturing facilities. The article titled “The Electric Motor in Factories”, and was published in Science by the American Association for the Advancement of Science in 1889. [1]
The article follows a group of individuals from the New York Electric Society and the American Institute of Electrical Engineers as they tour the factory of the C. & C. Electric Motor Company. The focus of the tour was on the engine room and the manner in which the entire factory was driven from the engine room not by massive belts passed through the floor to power equipment motors, as was the standard at the time, but with shafting. Shafting in 1889 was somewhat revolutionary and allowed for less power to operate the factory and allowed for easier maintenance and shut down of particular manufacturing lines or divisions.
The engine itself was belt driven direct to a 50,000W Edison wound dynamo that furnished the power to light the building and power the motors that drove heavy machine such as lathes, planers, drill-presses and milling machines. In total there were around 30 such heavy machines throughout the factory. The touring group was quite impressed that to run all of these machines only four motors were being used, two 3.5 hp and two 1 hp. However, the group did note that many of the machines were only in operation for short periods and the machines would not be used simultaneously.
It was also noted the current for the incandescent light bulbs required a heavy draw, although it never exceeded 18 hp, and during peak daytime hours that could drop to 12 hp. “The average load on the dynamo is about 40 amperes, or about 12 electrical horse-power, which covers both light and power. The friction load on the engine is 6.4 hp, giving us a total of about 20-22 hp on the engine. The power which would be required to operate the factory in the usual way, by belting through the floors, was estimated to be between 30 and 50 hp, without considering the power required for the lights, amounting to an additional 15 hp.” [2]
It is always interesting to look back and see how some minor changes to the way we operate can have substantial benefits, a point we are still refining today. Motors and operations have come a long way, but at times we benefit from simply looking at the minor differences in how another operates or makes use of the same products you do, it might just benefit how you operate as well.
[1] The Electric Motor In Factories, In Science 13 (317) (1889) pp. 153-154
[2] The Electric Motor In Factories, p. 2
Photo Source: The Electric Motor In Factories, p.154