Is Predictive Maintenance Expensive? Or Are We Being Short Sighted?
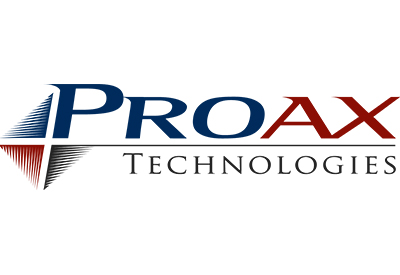
February 16, 2021
By Mathieu Paré, Application Specialist Omron Automation Americas
In the absence of a predictive maintenance strategy, manufacturers must take care of their equipment with regularly scheduled preventive maintenance. According to Plant Engineering, manufacturers spend an average of 19 hours per week maintaining their equipment. As the equipment ages, maintenance becomes increasingly time-consuming and costly, thus making preventative maintenance very expensive.
To combat the high cost of preventative and reactive maintenance, many companies are now embracing predictive maintenance technologies, which provide 24/7 monitoring of equipment condition to reveal any issues before an actual failure occurs. However, some manufacturers still balk at the upfront cost of these advanced solutions.
Let’s explore a couple of reasons why it’s actually more expensive to avoid a predictive maintenance strategy.
1) Regularly scheduled maintenance can miss issues arising between inspections.
Preventive maintenance strategies – in which maintenance activities are performed at regular intervals – have large blind spots. Since there’s no round-the-clock machine monitoring system, equipment problems that start to show up immediately after a maintenance session will continue to evolve until the subsequent maintenance session.
Depending on the type of system, this situation could be untenable. In one example, a Canadian research facility found that – despite frequently scheduled maintenance – its air handling units (AHUs) were failing unexpectedly. When the facility started using the Omron K6CM motor condition monitoring device for predictive maintenance, these failures stopped occurring.
By installing a round-the-clock monitoring system, the facility was able to ensure 100% uptime of a critical system and avoid the destruction of valuable biomedical research materials that would otherwise result from a lack of AHU functioning.
2) Without 24/7 monitoring, manufacturers often replace equipment prematurely.
Manufacturers relying on preventive maintenance find themselves with a dilemma. To avoid a catastrophic machine failure – since there’s no continuous monitoring to sound the alarm between maintenance sessions – they typically opt for buying new equipment before it’s truly necessary.
By investing in predictive maintenance, manufacturers can rest assured that the system will indicate exactly when it is necessary to consider replacing equipment. Continuous monitoring removes the need to hedge one’s bets and replaces it with peace of mind and confidence in a fully functioning system.