Understanding General Motor Starting Methods
December 21, 2023
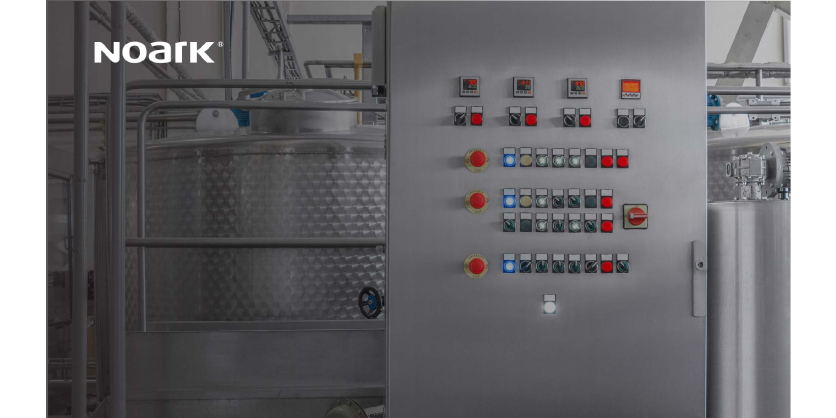
Motor starting methods and their strengths and weaknesses
In industrial manufacturing, motors play a very important role in driving processes, handling or transforming materials from raw materials to finished products or services. It is equally as important for use in commercial applications, such as household appliances and industrial machinery in buildings and infrastructure, as well as in automobiles.
From Newton’s first law of motion, we know that motors must overcome high inertia at starting. That’s where motor starting methods come in, providing the necessary power to get things up and running smoothly. Choosing the right motor starting method minimizes stress on the motor and ensure a reliable and efficient start-up.
This article will cover the following motor starting methods and their strengths and weaknesses:
- Across the Line
- Reduced Voltage
- Multispeed
Across the Line Method
The “Across the Line” motor starting method is all about simplicity and effectiveness. This method delivers direct power supply to the motor, in other words the full line voltage is applied across the motor terminals, with no additional bells and whistles. Across the Line method can be applied in a reversing and non-reversing configuration to deliver power to the motor.
Pros of Using an Across the Line Motor Starter
- Simplicity: One of the key advantages of an Across the Line Motor Starter is its simplicity. It doesn’t require complex circuitry, making it easy to install and maintain. This simplicity also translates into lower costs, both in terms of equipment and labor.
- Cost-Effective: Across the Line Motor Starters are generally more affordable compared to other motor starting methods such as Auto transformer, Star-delta, Soft Starters or Variable Frequency Drives (VFDs). If budget constraints are a concern, this type of starter might be the way to go.
- Instantaneous Start: When time is of the essence, an Across the Line Motor Starter shines. It provides an immediate start-up, ensuring your motors reach their full operational speed without any delay. This feature can be particularly beneficial in low power applications where motors need to respond quickly, like in emergency situations or time-sensitive processes.
Cons of Using an Across the Line Motor Starting method
- Current Overload: One of the main drawbacks of an Across the Line Motor Starter is the possibility of a high inrush current. When the motor is energized, a sudden surge of current can occur, potentially causing a buildup of reactive power in the supply network, and voltage dips on other equipment in the vicinity. which may trigger a fault trip on circuit breakers. This issue can be mitigated by oversizing the starter components to handle the initial current spike but with higher cost implication.
- Mechanical Stress: Starting a motor across the line can exert significant mechanical stress on the motor and connected components. The sudden jolt during the starting process can lead to safety concerns, increased wear and tear, potentially reducing the lifespan of the motor. Proper maintenance and periodic inspections are crucial to mitigate this concern.
Reduced Voltage Method
Before we delve into the pros and cons, let’s quickly understand what a reduced voltage motor starter is all about. As the name suggests, this method involves reducing the voltage supplied to the motor during its initial start-up, which helps mitigate the sudden inrush of current. By limiting the initial current, a controlled start of the motor is achievable. This technique offers some interesting advantages and trade-offs. Examples of the reduced voltage starting are Auto-transformer starter, Star-Delta Starters and Soft Starters.
Pros of Reduced Voltage
- Decreases Mechanical Stress: By gradually ramping up the voltage, a reduced voltage motor starter significantly reduces the stress on mechanical components, such as belts, gears, and couplings. This smoother start can prolong their lifespan and minimize the risk of premature failure or workplace hazards.
- Enhances Power Grid Stability: Reduced voltage starting causes less voltage drop and reduces the strain on the power grid. This not only benefits the motor’s performance but helps maintain overall stability in electrical distribution and prevents voltage fluctuations that can affect other connected devices.
- Increases Energy Efficiency: When motors start at full voltage, they often experience a high inrush current, leading to increased reactive power or wasteful energy consumption. By reducing the voltage at startup, the initial current draw is minimized, optimizing energy efficiency and reducing electricity bills.
Cons of Reduced Voltage
- Decreased Torque: One drawback of reduced voltage starting is the initial reduction in torque output. Depending on the application, this may negatively impact the motor’s ability to start under loaded conditions, such as when starting a motor with a heavy load or in adverse weather conditions.
- Increased Start-up Time: As the voltage gradually increased, the motor’s overall start-up time is prolonged. Although this may not be critical for certain applications, it could be a disadvantage in time-sensitive operations that require quick motor response.
- Additional Equipment and Complexity: Implementing a reduced voltage motor starter requires complex control circuitry and the use of additional components, such as an autotransformer. This increased complexity means more components to install, maintain, and troubleshoot, which will require additional cost, expertise, or resources.
Multispeed Method
Using the Multispeed method of motor starters, the voltage and frequency applied to the motors can be varied so that the motors can be operated at varying speeds ensuring a smooth and controlled start. An example of a multispeed starting is the AC Drive or Variable frequency Drives.
Pros of the Multispeed Method:
- Energy Efficiency: One of the significant advantages of the multispeed motor starter method is its ability to optimize energy consumption. By providing the motor with multiple speed options, it allows for precise control over the power output. This flexibility enables the motor to operate at a slower speed when less power is required, resulting in reduced energy costs and increased efficiency.
- Enhanced Equipment Lifespan: The multispeed motor starter method helps extend the lifespan of electrical equipment by reducing wear and tear. By gradually ramping up the motor’s speed, it eliminates sudden jolts and stresses on the machinery. This controlled acceleration and deceleration minimize mechanical stress, leading to a longer life for both the motor and connected devices.
- Versatility in Operation: the multispeed motor starter method offers increased versatility in various industrial applications. With multiple speed options, this method can provide precise control over motor speed, making it ideal for situations where a constant speed may not be suitable. Industries such as manufacturing, HVAC systems, and water treatment plants can benefit from this adaptable motor starter method.
Cons of the Multispeed Method:
- Higher Initial Costs: While the multispeed motor starter method provides numerous benefits, it often comes with a higher initial cost compared to traditional motor starters. The complexity of the system, including additional components and control mechanisms, can increase the upfront investment. However, it’s important to consider the long-term advantages and potential energy savings when evaluating this factor.
- Increased Maintenance Requirements: The multispeed motor starter method may require more frequent maintenance compared to conventional motor starters. The high cost of the set up increases the need for regular maintenance to prevent potential failures or malfunctions with adverse cost effect. Regular inspections and scheduled maintenance routines are essential to ensure optimal performance and prevent unexpected downtime.
- Complex Installation and Setup: Implementing the multispeed motor starter method can be more intricate, demanding specialized knowledge and expertise during installation and setup. Electricians and engineers need to have a deep understanding of this technology to properly configure and integrate it with existing systems. Therefore, it is crucial to work with qualified professionals and ensure proper training for maintenance personnel.
Integrate NOARK Electric Motor Starters to Improve Your Power Systems
Now that they’ve explored the world of motor starting methods, it’s clear that each method has its own unique advantages and considerations. Whether you prefer the simplicity of an across the line starter, or the more advanced reduced voltage or multispeed starting there’s no denying the remarkable engineering that goes into getting those motors up and running. To keep receiving tech tip articles like this one, sign up for the Noark Newsletter to receive monthly emails featuring insightful articles, product updates, free resources, and more!
Also, while the starting method may not be the sole factor in selecting a motor, understanding the pros and cons can help you make an informed decision based on your specific needs and preferences. To ensure that your motor is starting safely and efficiently, contact the Noark Electric team to find the right motor starter components for the job.
Related Story
Noark Electric Tech Tip: Understanding Combination Motor Controllers
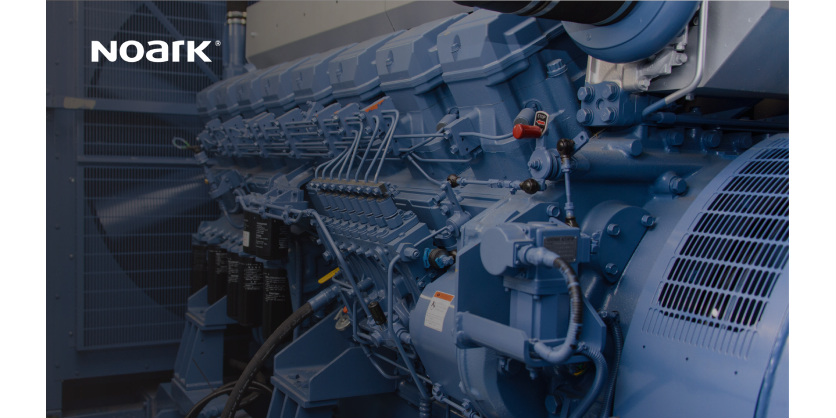
Electric motors are critical components in every production process or facility because they are the movers of mechanical equipment and machinery. Without them, nothing gets done. When designing a system, it is imperative to provide protection for motors using various protection and control systems. A Combination Motor Controller (CMC) is one way to provide motor branch circuit protection and control.