BiSS-C and SSI Encoder Interface Protocols Explained
March 5, 2025
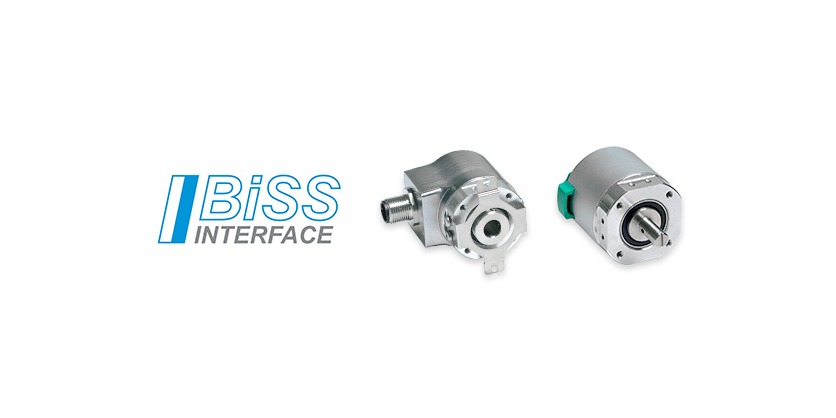
BiSS (Bidirectional Synchronous Serial) Interface, specifically the BiSS-C variant, is an open-source, real-time serial protocol designed for high-speed, bidirectional data transmission. Developed to improve upon traditional serial interfaces, BiSS-C supports efficient communication with absolute encoders, sensors, and other automation components.
BiSS-C Key Features
- High-Speed Communication: Supports clock rates up to 10 MHz, making it suitable for high-performance applications.
- Bidirectional Data Transfer: Allows reading encoder data and writing configuration parameters, enabling advanced diagnostics and system flexibility.
- Open Protocol: Unlike proprietary interfaces like EnDat and Hiperface, BiSS is an open protocol, reducing licensing costs and increasing adaptability.
- Real-Time Performance: Supports cyclic data exchange for real-time motion control applications.
- High Data Integrity: Implements CRC (Cyclic Redundancy Check) to ensure error detection and data integrity.
- Multi-Slave Support: Allows connection of multiple devices in a daisy-chain configuration, reducing wiring complexity.
BiSS-C Applications
- Robotics and industrial automation
- CNC machines and precision positioning systems
- Semiconductor manufacturing
- High-speed motor feedback systems
SSI Protocol Overview
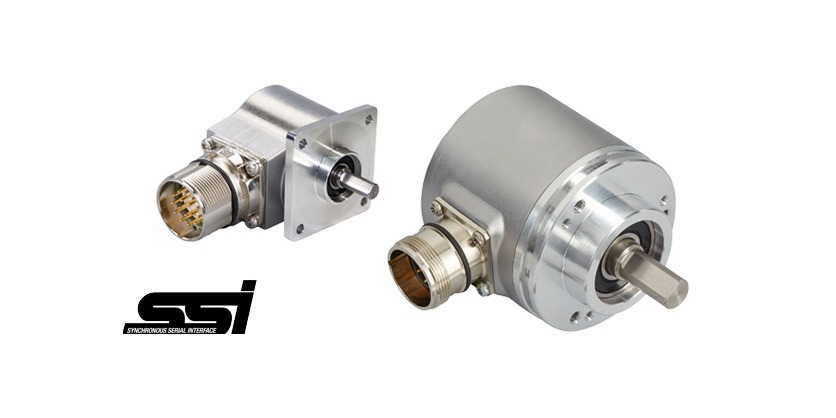
Synchronous Serial Interface (SSI) is a widely adopted serial communication protocol primarily used for absolute encoders. SSI is a unidirectional interface where the encoder transmits position data to the controller upon request.
SSI Key Features
- Unidirectional Communication: Data is transmitted only from the encoder to the controller, with no ability for configuration or diagnostics.
- Fixed Data Length: Typically supports 13-bit to 32-bit data formats, making it reliable for simple position feedback.
- Moderate Speed: Operates at clock rates between 100 kHz and 2 MHz, suitable for many automation applications but slower than BiSS-C.
- Simplicity and Compatibility: SSI is easy to integrate into existing systems due to its straightforward architecture.
- Noise Immunity: Uses differential signaling (RS-422) for robust data transmission in industrial environments.
SSI Applications
- Industrial automation and PLC-based control systems
- Elevator and conveyor systems
- Basic position feedback in motion control
- Automotive and medical applications requiring absolute positioning
Comparison of BiSS-C and SSI
Feature | BiSS-C | SSI |
Communication Type | Bidirectional | Unidirectional |
Data Integrity | CRC for error checking | Parity bit (optional) |
Speed | Up to 10 MHz | 100 kHz to 2 MHz |
Real-Time Capability | Yes, supports cyclic communication | No real-time feedback |
Multi-Slave Support | Yes | No |
Flexibility | High, supports configuration and diagnostics | Limited, only position data transmission |
Licensing | Open protocol | Standardized but more restricted |
Best For | High-speed, real-time, configurable systems | Simple, robust, cost-effective systems |
Key Takeaways
- BiSS-C is a more advanced, high-speed, and flexible protocol with bidirectional communication, making it ideal for real-time applications requiring diagnostics and configuration.
- SSI is a simpler, unidirectional protocol known for its robustness and ease of integration, suitable for applications that do not require advanced features.
- The choice between BiSS-C and SSI depends on the application’s needs: if high-speed, real-time data exchange with configurability is required, BiSS-C is preferred. For simpler and reliable position feedback, SSI remains a viable option.
Related Story
Introducing a New Generation of POSITAL Kit Encoders
POSITAL has announced a major upgrade to its family of 36 mm kit encoders for motion control applications. For these new devices, introduced as part of the company’s NEXTGEN initiative, upgrades include higher resolution and refined packaging that provides more compact form factors, better protection from solid particles and simpler installation procedures.