Danfoss Editron partners with Kongsberg Evotec
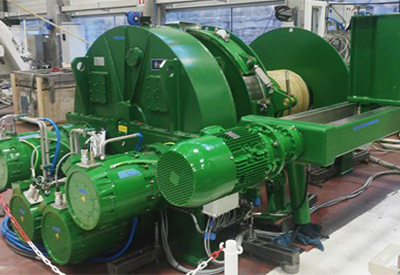
January 10, 2019
Danfoss Editron has partnered with Kongsberg Evotec, part of the Kongsberg Maritime international technology group. They will develop a fully electric-powered marine winch powered by EDITRON, the world’s most sophisticated electric drivetrain system.
Marine winches are components on vessels used in offshore industries such as fishing, research and seismic. As well as those taking part in on-water construction projects for offshore wind farms. The EDITRON drivetrain for the Kongsberg Evotec marine winch system is comprised of lightweight and compact, yet immensely powerful, reluctance-assisted permanent magnet motors. These save weight and space in the deck handling equipment. Both of which are a scarce resource in a marine vessel and needed for payload purposes.
The new electric solutions offer better area utilization in both new-builds and retrofits. They save on weight and space compared to traditional hydraulic-powered winches, which have high installation costs. The reason is the amount of piping required and need a big installation space for the hydraulic power unit. Hydraulic winches are also less energy efficient than electric counterparts. As they experience bigger power losses and run on a higher average power usage, even when in idle operation. Further potential downsides of hydraulic winches include negatively impacting working conditions on board vessels. This is thanks to the loud noise levels they emit and the risk of oil spilling into the marine environment.
Integrating electric components into the winches allows them to be controlled remotely. This makes them more responsive to commands and providing functionality with tailored applications. These can give direct upsides to operation safety and cost. This drives further efficiencies by lowering fuel costs and associated CO2 emissions when compared to traditional hydraulic designs.
The EDITRON winch application software also combines winch-specific functionalities. Such as wire tension control and limit, speed control, position control and brake control. Additionally, several safety features are directly implemented into the drivetrain. These ensure a quick and seamless response to any failure handling event. This is achieved by operating the drives in a redundant set-up and having this philosophy anchored into the drive/control interface architecture.
Kongsberg Evotec’s Operations Manager Bjørn Berge states:
“Compared to traditional hydraulic winches, which still have a strong standing in some applications. We see the new generation of winch solutions as an important contribution to tomorrow’s handling technology. We are aiming at being a major player within marine handling technology. Therefore, we need to ensure that we can help our end-customers reduce their operating costs. At the same time, increase safety through better, easier and more accurate control of the equipment. Weight and space saving when installing our winches onto both new-build and older vessels where we are working on retrofit perspective are vitally important to this.
Through tests and demonstrations, we have proven that our cooperation with Danfoss Editron was the right strategic decision. Additionally, that we are now in front with some of the solutions we are offering to the market. We consider Danfoss Editron to be one of our most important technology partners for the future. Therefore, we highly appreciate the cooperation and collaboration established on both a technical and management level within the two companies.”
The first two electric winch systems, featuring the new Danfoss Editron drivetrain solutions, have been supplied to the offshore and seismic markets. In early 2019, the first large-scale project will be commissioned and delivered from Havyard in Leirvik, Norway. This is, after going through full-scale interface and functionality testing. With 10 winches and 20 drives and motors in total being installed on a pelagic trawler. Additionally, a Launch and Recovery System featuring a dual motor fed by two inverters and Kongsberg Evotec control system has been delivered to a Norwegian customer for start-up and commissioning in Turkey. As well as the standard drivetrain functions and safety, this system includes heave compensating functionality. Power efficiency and regeneration become major contributors to increased system performance and reduced operating costs.
Danfoss Editron is also working with Kongsberg Evotec on an automated deployment and retrieving system for seismic nodes. This is powered by its EDITRON software. The system, which will increase the speed and reduce the cost of ocean bottom seismic node operations, can be seen as a revolution in its market and the technology is now available for customers.
Joonas Talvitie, Project Manager at Danfoss Editron, commented:
“It’s great to be working with one of the marine industry’s biggest players as the electric revolution continues to move forward with significant momentum. We’re proud to offer our market-leading technology to customers as it provides them with further opportunities to fully electrify their on-board equipment and reduce fuel costs and associated emissions.”