Compact Carrying Case Solution Offers Versatile Use in the Field
November 11, 2024
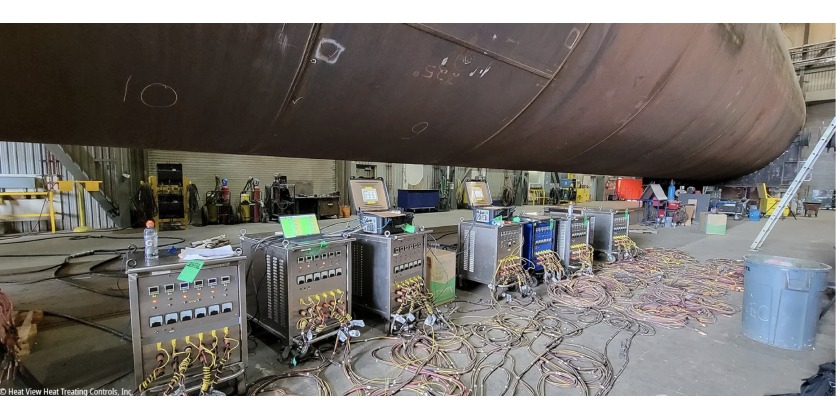
Portable PC- and EtherCAT-based controls for in situ heat treatment
Heat treatment is traditionally used in the welding of pipelines to influence the material properties through controlled heating and cooling. A Canadian system integrator was looking for a flexible, compact system solution for controlling and documenting this process. With the space-saving EtherCAT Terminals and Industrial PCs from Beckhoff, the smallest version of the Heat View solution now even fits in a carrying case.
When system integrator Jeremy Breetzke started prototyping the Heat View Heat Treating System, he had no idea how many different applications and industries it would eventually be used in. Back in 2018, he simply saw a gap to fill. There was no compact, flexible option to control, monitor and provide reports during in situ heat treating in factories, plants or remote areas. So the owner of Grand Controls, Inc. based in London, Ontario, started working on a design.
“The Heat View product grew so quickly that in 2021 we spun it off as its own company, Heat View Heat Treating Controls, Inc.,” Jeremy Breetzke says. Scott Fong is Group Director at KASI Technologies Inc., a company that sells and rents field heat treating equipment. So he knew the requirements for the new platform firsthand and supported the development process with technical input.
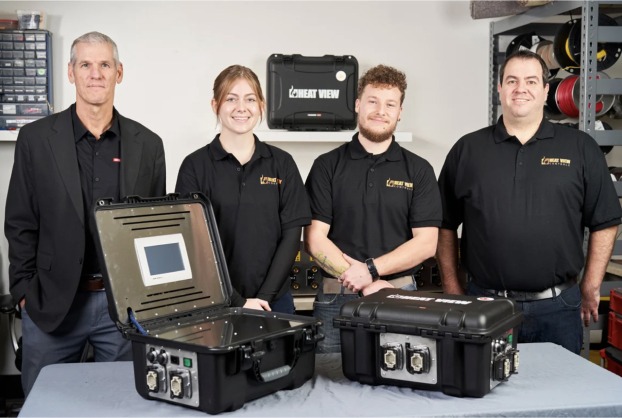
The original use of the control system was to ensure that welded parts reached and held the correct temperature to avoid defects. This is critical when building oil and gas pipelines or refining infrastructure, for example, where failures can be costly and environmentally catastrophic.
The system has been used for that purpose in aerospace, mining, shipbuilding, petrochemicals and more. But it has also been applied to power generation and high-velocity combustion. Once the work is completed, the unit provides the necessary quality control reports.
Covering all the bases with PC-based Control
The team of developers had several goals. First, the product had to be easy to transport and set up. Second, it needed to flexibly adapt to customers’ requirements, such as accommodating different types of current transformer (CT) coils or communicating via various fieldbus protocols to existing equipment. Third, it needed to be easy to use with a more intuitive operator interface, whether the customer wanted a built-in control panel or simply to plug in a laptop. Jeremy Breetzke had been working with Beckhoff Canada since 2017 for applications with his system integration business, and knowing the flexibility of the EtherCAT and PC-based control technologies, they seemed like an ideal fit for these requirements.
The Heat View Heat Treating System comes in several form factors with options for customization. The most portable is the ConPak 24-channel heating controller, which is built into a rugged plastic case for easy setup and portability. In addition, the company provides an embedded controller for installation into new or existing equipment and generator panels.
From an automation technology perspective, both systems are very similar. Scalable, fully integrated control technologies from Beckhoff allow the company to use either a C6015 ultra-compact Industrial PC (IPC) or a CP6606 Panel PC when customers would like a built-in, 7-inch industrial touchscreen. “Both controllers run the same Windows version, along with TwinCAT 3 automation software, of course,” Jeremy Breetzke says. “So the code that we wrote for the CP6606 was easy to port over to the C6015, and we could write custom code in C# and C++, which isn’t possible on a traditional PLC.”
By leveraging TwinCAT 3 from Beckhoff, the Heat View team benefited from a universal, end-to-end engineering and runtime platform for automation. TwinCAT integrates with Microsoft Visual Studio, which empowers engineers to program in a familiar, contemporary environment with the language that best fits their application. Jeremy Breetzke appreciated having Structured Text as a programming option, as well as the ability to deploy functions built into the libraries: “TwinCAT has a vast array of libraries that includes many function blocks that aren’t very common with PLCs, such as file read and write,” Breetzke says. “This makes code development much faster.”
EtherCAT supports versatility
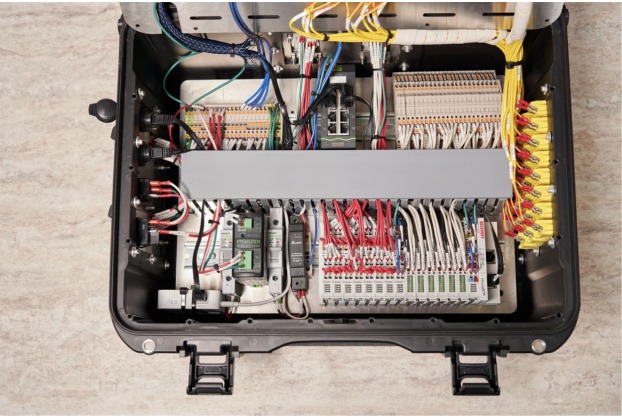
EtherCAT simplifies industrial networking significantly for Heat View. The wide variety of Beckhoff bus couplers and gateways to more than 30 common protocols ensures Heat View can connect to all kinds of modern control and SCADA systems.
Heat View uses various EL series EtherCAT Terminals for basic input and output of signals. However, even more specialized measurement modules retain the same compact 12-mm housing size. Thus, the compact EL2624 4-channel relay output offers a relay contact up to 125 V AC or 30 V DC, with its long lifetime reliably cycling in the field for years.
With four individually parameterizable analog inputs, the EL3174 EtherCAT Terminal supports signals ranging from -10/0 to +10 V or -20/0/+4 to +20 mA on each of the channels. This helps the systems adapt to changing customer requirements in terms of current transformers, according to Jeremy Breetzke. “With most heat-treating control solutions, changing the CT type would require opening up the console, rewiring it and replacing all the CTs – or using very expensive ones that rectify the signal and feed it back into their controllers,” he says.
Ideal for wide-ranging applications
“Sometimes, crews weld pipelines in remote areas where they camp and use generators for power. Other times, they’re working on large facilities and move the setup around frequently,” Jeremy Breetzke explains. “It’s much easier to pull a 45-pound ConPak system out of your pickup and plug in four cables than transport traditional consoles that often weigh 800 pounds or more.”
Currently, Heat View appreciates the ability to communicate quality control data to an operator’s laptop using an Ethernet cable and the ADS protocol. Since TwinCAT engineering software is free to download from the Beckhoff website, customers can also easily install updates. The system’s next step will involve additional IoT connectivity. Support for vertical communication protocols – such as OPC UA, MQTT and AMQP – will allow users to send reports and push updates from the cloud.
“We’re monitoring so many different variables and mitigating faults to create a foolproof system. Our systems integrate elements of AI, so they can learn on the fly and detect problems while factoring in external variables,” Scott Fong from KASI Technologies says. “These capabilities are game changers compared to what’s on the market and the next-generation products we have in development will be even better.”
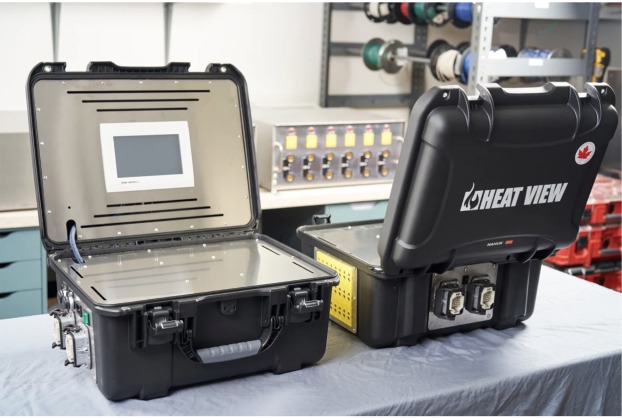
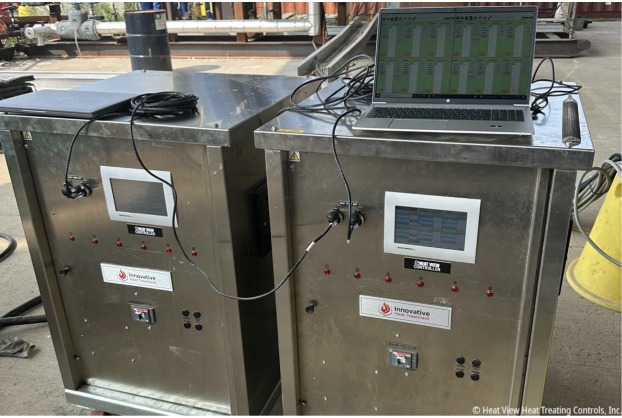
More Information
- EtherCAT Terminals
- TwinCAT automation software
- Heat View Heat Treating Controls Inc.
- Grand Controls Inc.
Related Story
TwinCAT PLC++: Next Generation PLC Technology
TwinCAT PLC++ is a completely new development from Beckhoff that integrates seamlessly into the existing TwinCAT ecosystem. Of course, TwinCAT PLC++ continues to be based on the languages described in IEC 61131-3. Due to – but not limited to – the advanced compiler technology and the new architecture used, a significant leap in engineering and runtime performance can be achieved.