Protection & Controls Engineer, Matt Davis on his Experience as a Young Professional
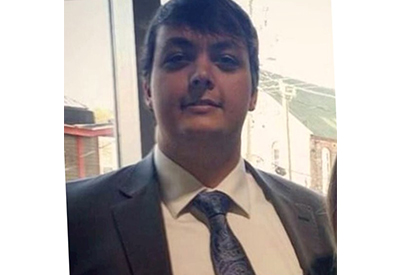
September 16, 2019
By Blake Marchand
Drives & Control Solutions had the pleasure of interviewing Matt Davis of Newfoundland Power, a talented young professional working as a Protection and Controls Engineer.
For our purposes Davis’ story begins in 2011 at Memorial University (MUN) in Newfoundland where he enrolled in their Engineering program. Following his first year he found himself drawn towards math and physics, “particularly the electrical side of physics,” he noted, as well as the courses focused on programming, circuits and robotics, which lead him towards the co-operative Electrical and Computer Engineering faculty at MUN.
Davis completed his first co-op term working with Rio Tinto as an Automation Engineering Student, which provided him with control systems experience in a heavy industrial environment, something he had always been interested in exploring. “While there I was mainly gaining exposure to the projects of my colleagues while also working on a small control system project to set up an EMT response mode in the cargo elevator in the processing plants,” he explained, adding, “That little project was the first to get me into a control system – making changes and testing them, and although a fairly simple and non-process related, it provided an immediate change for the workers in the plant.”
Davis would go on to co-op with Teck Resources, a minning operation that gave him more experience working on a heavy industrial site. “Main duties included keeping mobile equipment single line diagram as up to date as possible. Mine trailing cable inspection and logistics, as well as smaller projects and contractor supervision.”
Davis spent the remainder of his co-op terms with The Cahill Group as an Instrumentation and Control Engineering Student in Mount Pearl, Newfoundland, and a Construction/Commissioning Field Engineering Student in Fort McMurray, Alberta. The former had him working on the HVAC control systems for the living quarters at an Exxon Mobile project.
“The HMI to be used was a Panelview Plus (Rockwell Automation) and my main duty was to use the Ducting and Instrumentation Diagrams to create the new screens to fit the project specification, including all active animations and operator interfaces,” he said of his work in Mount Pearl, “Also setting up the tag database and the user control and access levels. The student following my work term would then translate the logic flow diagrams and existing tags into the PLC and complete the process of linking the PLC configuration to the HMI. This was my first real exposure to HMI screens and building them from scratch, as well as the hands-on nature of the work it was likely one of my favorite work terms to date,” he said, Davis noted another contributing factor was gaining experience with I/C engineering.
Davis finished off the co-op portion of his program in Fort McMurray, on the Conoco-Philips Surmont 2 SAGD Project, supervising and providing progress reports on the construction and commissioning of well pads. His second term in Fort McMurray focused on developing the commissioning plans for each well pad.
“Throughout my work terms I was pretty lucky to always seem to have excellent, experienced mentors and supervisors to help me along the way who were passionate about Control Systems Engineering and Engineering in general. As well as seeking out the chances to work on what interests me the most and getting involved every chance I could.”
Davis graduated from MUN in 2016 and was offered a job with Astaldi Canada doing ‘fly-in-fly-out’ work on their Muskrat Falls project. He worked with Astaldi for just under 2-years, deciding to move on to a Controls Systems position with Wood PLC.
With Astaldi, Davis noted, “A couple highlights were helping wire up an overhead crane, being involved in tower crane maintenance, troubleshooting a concrete batch plant, and troubleshooting water management equipment.”
With Wood Group, Davis was placed in their full-time pool of engineers supporting a client owned FPSO, “this would be my first bit of experience in a purely control systems role,” noted Davis.
“A couple of my major projects were the overhauling of the alarm system onboard to bring it up to industry standards, this was worked on together with a more senior Engineer since it was ongoing when I joined Wood,” Davis continued, “I was also involved in some process/safety optimization projects onboard the FPSO for example, process debottlenecking, subsea well additions, updated fire and gas logic, equipment replacements, or upgrading logic to account for more operational cases.”
“By far however, the most enjoyable times for me with Wood were when I travelled offshore Being offshore was an excellent opportunity to get more familiar with the equipment, both controls as well as process equipment. The system onboard was all ABB gear, the Bailey Infi 90 system with a little bit of third-party stuff for special applications (HIMA, GE, Allen Bradley).”
While working with Wood, it became clear for Davis that he preferred to work with control systems. Although, he noted the demand for controls engineers in Newfoundland isn’t particularly high.
In his current position at Newfoundland Power, Davis primarily handles control systems for their network of hydroelectric/diesel turbine generators. “These are mainly all based on an Allen Bradley architecture. I am also involved in backup generator support, transformer protection, and assisting with the roll out of a new IoT solution for IED management, both configurations and event management.”
Considering you’re relatively new to the industry, I’d be curious to know how your experience in school has translated into the technical work you are doing now on the job? There’s certainly a learning curve with any new job, but did it meet your expectations, were there any interesting/unexpected challenges, or aspects that were particularly interesting to you?
I found that in school you learn some pretty antiquated techniques and technologies to achieve proper control. Of course, they also teach you the fundamental theory behind control which provides the basis for which to build a more complicated modern system. I would say that while learning different theories, such as system dampening, cascaded controllers, the maths behind PID loops, and general control structure were helpful it would’ve also been beneficial to learn more about modern control solutions, such as PLCs and their role, or the application of communication technologies in a DCS.
As for learning curve, I don’t believe there is too much of a learning curve when it comes to the baseline theory, but more the execution. In my current employer transition I have gone from all ABB equipment to all Allen Bradley equipment, learning all the new software and all the new hardware components of the system is proving to be the bigger challenge overall.
I would say my favorite aspect of my education was learning how to build closed loop systems and playing with PID gains to achieve the correct system response; we used Simulink in our classes to model systems and playing with the values and different control types gives you an appreciation for how you can expect the system to react.
What is your day-to-day like as a Protection and Controls Engineer for Newfoundland Power? What challenges you, what interests you?
My general work structure is that I have a few projects I work on throughout the fiscal year (design in the spring, implementation in the summer, and commissioning in the fall). I will typically come in and check if anything needs my attention for one of my projects and if not just work on tasks I will need to complete. The thing I like the most about control systems is that it is more hands on than other Engineering disciplines, so I will typically work on getting some device up and running (such as a communications link) or my IED mgmt. project requires a lot of leg work to build the inventory base before the database configuration can really happen effectively, so on days where there is nothing pressing I can dive into that for 8 hours.
Since we are a utility provider my position also requires road travel, one of my projects is replacing a HMI in a plant about 6 hours away so there are days where I will hop in a truck and drive out to the nearest hotel to complete a site visit as required. Overall, it is a pretty self-directed position as we have an operations department as well that typically handles issues that need immediate attention.
Are there any projects you have worked on that have been particularly fascinating for you?
While I was with Wood, I was working on some process debottlenecking/emergency shut down (ESD) scopes of work. I found the thought process for “last man standing” equipment particularly interesting; ensuring that if there is fire/an explosion my skid is engineered to keep on operating to ensure the situation doesn’t escalate. It was a nice opportunity to look more into the philosophy side of control system as well as oil and gas system design in general. Since it was mainly a process driven task there were lots of chances to ask questions and gain insight into the production process under scrutiny. It was also broken out into a lot of different scopes of work so there were many different things to dive into. Lastly, since it had ESD components it was exposure to some of the controls hardware on board that isn’t ABB, since the ESD system was stand alone for integrity reasons.
With respect to industry trends or technologies, what is interesting to you right now, or what do you find is pertinent to what you are doing? Is there anything you see as becoming more prominent 5-10 years down the road?
While I was working in oil and gas there was a big dependency on hard wired individual signals, especially when doing high integrity cause and effect trips. I think in the coming future using TCP/IP and more streamlined and unified communication methods in – even high integrity – control systems will become more common. I believe that as technology advances for even further distributed control systems (i.e. Ethernet networks and long run fibre) you will see more remote control, especially in the offshore industry.
Also, with further distributed control I think IoT will become a significant player. You will see more job positions open up for specialized IT (I’ve seen a few now for Automation IT Engineers) who will handle the IT side of network control solutions.
I have heard of smart homes and some pilot project by some of the big tech companies in the US, however, industry application will lag behind cutting work being done by technology companies, as expected.
There are also some people doing interesting work in the field of AI and machine vision to detect issues in a process environment or using big data analytics to optimize plant operation. I think the future of Automation and Controls is going to be pushing more into delocalized control, data acquisition, and self-sustaining systems.
What do you hope to accomplish with your career?
To be honest, I’m not exactly sure. I really enjoy technical work and really prefer being on site working and seeing the equipment; I think that is the best way to learn about any system. However, I am not sure if that feeling will maintain as I enter my thirties or forties. I’m sure at some point I will want to come back to an office and get into a more management position. The company I currently work for really seems to take care of its employees, so I would say this will be a much longer-term arrangement than my previous employers.
I am currently trying to position myself for a smooth transition into supervisory roles when the time comes, if ever. I am studying for my GMAT and plan to do an MBA in the next few years. I will likely pursue a part time course.