Turbines or Electric Drive Systems for Pipeline Compressors: The Long-Term Gain
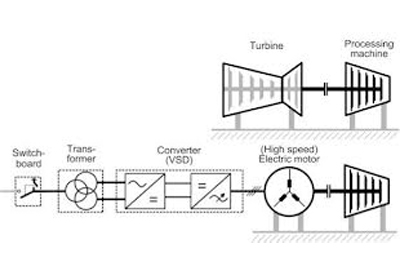
By: Owen Hurst
In this article the consideration of electrical drive systems and their benefits over turbines for use in Oil& Gas operations is examined. For this consideration we review an article first published in 2016 by Gunther Schwarz and Hans Keller, members of Siemens AG.[1]
Schwarz and Keller note that turbines have traditionally been used to drive processing machines, but here we focus primarily on the concerns regarding turbine use for driving centrifugal compressors for pipeline compressions. In Canada pipeline discussion is a common topic among the industry and the public, and a common concern is often the low efficiency levels and high emissions that are associated with this operation. In 2016 Canada had 73,000km’s of pipeline and thus ensuring efficient compression over such distances is critical to maintaining a cost-effective operation and ensuring environmental concerns are accounted for.
But before considering the drives themselves we need to briefly consider the operation of compressors in Oil & Gas operations and turbine operation. By understanding these the benefits of elective drive systems become more prevalent.
The compressors job is obviously to produce pressure, but its operation and maintenance can be optimized depending on the driver and control platform in place. Speed limits of compressors can be controlled to ensure operational efficiency and to avoid low flow conditions that can result in incidence loss and potential surge if the compressor operation is not adjusted. Operation through variable speed provides the best results as they only use the power required for operation and can be controlled within the compressors defined speed range.[2]
There are several forms of turbine operations in place. Gas turbines are commonly used for flexible operations and consist of three parts: air compression, combustion chamber and turbine. It is somewhat difficult to track exact statistics on gas turbines as many are made to order and vary from design to design. However, they do typically rely on specific applications like ambient temperature, ambient pressure, humidity, load, range and fuel.[3] There are two primary gas turbine types used, aero-derivative and heavy duty. There also exists an industrial gas turbine that is not considered here. Aero-derivative has a higher firing temperature leading to higher efficiency in operation but also higher emissions. Heavy Duty has a lower firing temperature designed for robust use and longer life with lower efficiency and emission rates.
Steam turbines are also common in operations and are in regular use to power compressors. However, industrial sites with steam networks in place are unlikely to make the switch to electric drives as a result of the financial cost of changing operations.
Now to consider the various opportunities presented by electric drive systems to generate the necessary control and compression needed for Oil & Gas piping. Electric drive trains are made up of a transformer, converter, variable frequency drive (VFD or VSD, variable speed drive), an electric motor and at times a harmonic filter. In regard to frequency drives in higher power applications the load commuting inverter (LCI) type is required and typically requires the use of a harmonic filter. In other application voltage source inverter (VSI) frequency drives are the more common.[4] For the motor either induction (asynchronous) or synchronous are applied. “Centrifugal compressors often are operating at high speed conditions. Therefore high speed motor with sleeve bearings or Active Magnetic Bearing, short AMB, is a well suiting solution for direct driven compressor operation without gearbox or hydraulic torque converter.”[5]
When considering the potential benefits of utilizing electric drive systems over turbines Schwarz and Keller utilized common value/ranges and undertook various tests with these applications in consideration.[6]
Emissions are one of the primary environmental concerns and a major driver of enhancing technology. Based on standard carbon dioxide production levels of a simple cycle gas turbine, an 8 MW compressor gas turbine in operation over a year would produce roughly 32.000 tonnes of carbon dioxide.[7] An electric powered drive system produces zero emissions on site.[8]
Another advantage to electric drive systems is their operability in terms of installation and depending on the source of electricity are more flexible and do not require regular fuelling considerations.
But, next to the substantial decline in emissions the operational efficiency is the primary advantage. One for this is the difficulty in pinpointing gas turbine efficiency. Gas turbines have various types and are often set to specific design parameters and ambient conditions. However, ambient conditions may change on site that lead to deviating operational parameters that cause fluctuating efficiencies that are hard to track from site to site. Electric motors typically have a specification between -20 and 40 °C and has a near constant efficiency across the ambient temperature range. And if there is expectation of ambient temperatures beyond these ranges they can be factored in at the design phase.
“Assuming a compressor efficiency of 83%, which represents a realistic value for the design point and an efficiency of 40% for an aero-derivative, the gas turbine drive train has a total efficiency of 33% for ideal conditions (heavy duty around 27%). The electric drive train, starting from the transformer (99%), VFD (9%), electric motor (98%) and same compressor efficiency of 83% ends up at a total efficiency of 80%.”[9]
There are a few further considerations that present particular benefits. One concern is that suction pressure in depleting oil fields decreases and requires increasing compressor power. Typically an entirely new compressor string would be required but in terms of electric operations a double end electric drive may be used to include a second compressor into the operation.
Start-up & stop processes can also have a major impact on operations. The ability to start and stop in a timely and efficient manner can be a great advantage. Aero-derivative gas turbines can start within about 10 minutes and Heavy Duty take about 10-15 minutes from idle speed. We should also note that there are limitations for compressor start processes, but electric drives can typically reach operating speeds in less than 4 minutes.
General maintenance is always a concern as downtime is costly but electric drives offer an advantage in this area. Typically, gas turbines require regular shutdowns and can lead to several days of maintenance required per year. Electric drives require minimal maintenance and can often been assessed while in operation. And as they do not require typical maintenance such as oil changes the effectiveness is optimized. Further electric drives offer sensor and analytic monitoring of the whole drive train which can provide real-time data and regular digital reports.
So, it seems obvious that electric drive systems offer an advantage over gas turbines as a means to power and control pipeline compressors. However, every operation has particular needs to consider such as location and relationship to the power grid. As a result, companies should perform an assessment of each method by looking closely at energy costs, operating hours/load, maintenance schedules, downtime, emissions tax and insurance to determine if utilizing an electric drive system in their operation would be beneficial.
Schwarz and Keller likely noted it best by quoting another forward thinker and then closely defining the overall advantages: “’The electric light did not come from the continuous improvement of candles’ (quote from Oren Harari), in other words the electric drive train offers the flexibility to meet changing demands, lowers the environmental impact, offers a higher level of availability and comes along with higher efficiency.”[10]
The article by Schwarz and Keller is certainly forward thinking and lays out in a very clear and defined manner the advantages of utilizing electric drive systems can bring to Oil & Gas operations, and as such their report and finding should be a primary driver for the future of Oil & Gas operations.
Image 1 source: https://w3.siemens.com/markets/global/en/oil-gas/Documents/downloads/technical-papers/Turbine-Replacement-PCIC-2017.pdf
Sources
[1] Schwarz, Gunther and Keller, Hans. “Turbine Replacement by Electric Drive Systems Provides Significant Benefits”, PCIC Europe EUR17_49
[2] Schwarz and Keller. “Turbine Replacement by Electric Drive Systems Provides Significant Benefits,” p. 1
[3] Schwarz and Keller, p. 2
[4] Ibid., p.3
[5] Ibid
[6] The statistics utilized henceforth are the results of Schwarz and Keller and as they stated these “only present indications, not absolute values.”
[7] Ibid., p.4
[8] Ibid
[9] Ibid., p.5