The COVID-19 Cold Chain: Why Refrigeration Logistics of Vaccine Distribution are Critical
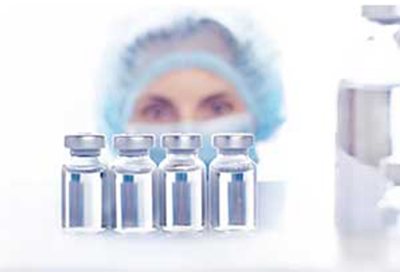
January 5, 2021
As the world prepares to immunize against COVID-19 in the coming weeks and months, there will be real logistical challenges involving the storage, transportation, and distribution of the vaccine under temperature-controlled conditions throughout the entire cold chain. Because of the required two doses for full effect of the vaccine, there will be a need for more than 15 billion doses to cover the entire population.
While the two vaccines that are currently approved for emergency use both need to remain frozen, they require different freezer temperatures. Moderna’s vaccine is stable at a regular freezer temperature of -20 degrees Celsius for up to six months. However, the Pfizer vaccine must be kept extremely cold, at a temperature of -70 degrees Celsius — a temperature colder than the Arctic. This will require an ultracold freezer to keep the vaccine effective.
How the Cold Chain Will Play a Role in Distribution
The cold chain, a temperature-controlled supply chain infrastructure that includes airplanes, trucks and cold storage warehouses, will play a major role in the successful rollout of the COVID-19 vaccine. The vaccines will start at cold storage units in the manufacturing plant, then be transported in refrigerated planes or trucks, and finally be properly stored at the provider facility. At any point in this process a disruption to the cold chain would deem the vaccines too warm and therefore ineffective.
According to the Center for Disease Control and Prevention (CDC), manufacturers, distributors, and health care providers will share the responsibility of ensuring the vaccine cold chain is maintained from the time vaccines are manufactured until they are administered. Disruptions or issues with the cold chain have caused issues in the past. The World Health Organization estimates that nearly 2.8 million doses of vaccines were lost in 2011 because of a broken cold chain. Losing this many doses would be disastrous for gaining control of the COVID-19 pandemic.
The Importance of System Monitoring
In addition to proper storage at these super cold temperatures, system monitoring will be crucial to ensuring the integrity and quality of these important life-saving products. Regal’s newest solution, Scandia, utilizes connected motors with EIA485 Modbus communications, temperature sensors, and networking capabilities that provide 24/7 real time access to motor functionality and system performance.
In the past, medical refrigeration systems have utilized double condensers to allow for a backup mode in case a failure occurred with the standard condenser. If the motor on the condenser side failed, the second fan could be started without any disruptions to the temperature of the cooler. With the Scandia cloud-based asset monitoring solution, it’s possible to automatically detect equipment problems well before they become a problem. This allows for immediate corrective actions and maintenance planning in order to help avoid the time and expense of troubleshooting and most importantly – prevent loss of vaccines.
Motor Options for Medical Refrigeration Systems
Regal’s wide array of motor offerings include Shaded Pole, Permanent Split Capacitor (PSC), and Electronically Commutated Motors (ECM) with power output from 2W to 75W. These products are ideal for ensuring evaporator and condenser applications in medical refrigeration systems are functioning properly.
All of Regal’s Shaded Pole and PSC motors can be sold with a variety of mounting brackets and fan blades in order to optimize airflow and system efficiency. Regal’s global manufacturing footprint gives them the ability to quickly adjust their production location to support the increased demand and provide the most cost-effective Shaded Pole and PSC motors for refrigeration equipment needs. In fact, their PSC motors are already successfully being used in vaccine coolers to support the Center for Disease Control and Prevention (CDC) during project Warp Speed.
Regal’s ECMs can operate at up to 72% peak efficiency, which means they dissipate less heat and allow the refrigeration system to operate more efficiently. Their products are certified for use in low Global Warming Potential (GWP) refrigeration systems that are commonly used for vaccine storage, as well as being ATEX certified for being intrinsically safe. Another key benefit of the ECMs is the superior sound performance, which is well-suited for hospitals so healthcare workers and patients can enjoy a more comfortable environment.
How Regal Can Help
In order to support the rapid ramp up in refrigeration equipment needs, Regal are increasing production of their motors and their manufacturing facilities have developed streamlined procedures to process and ship as quickly as possible. By leveraging their large global manufacturing network, they have motors ready to ship and can supply your demands from multiple manufacturing locations.