Top Three Areas Where a Cobot Can Dramatically Improve Productivity
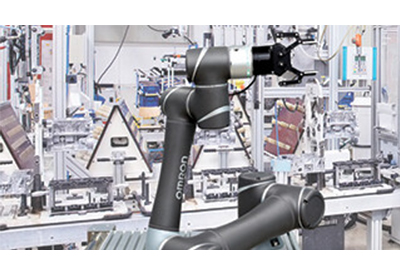
May 31, 2021
There re quite a few repetitive tasks in manufacturing. If all of these tasks must be performed manually, then a large number of a manufacturing company’s employees would be occupied with extremely mundane and tedious activities throughout the day.
One of these technologies is the collaborative robot, or cobot for short. This type of robot has built-in safety mechanisms allowing it to work closely with humans as well as on its own. Easy teaching mechanisms mean that cobots start covering new tasks with minimal changeover effort, adding to their flexibility.
Let’s take a look at a few key task categories that a cobot can perform, allowing human workers to focus on value-added activities that require more intelligence.
1.Machine tending
Machine tending refers to the activity of loading and unloading raw material or works-in-progress to and from a machine. Most machine tending processes are still performed manually–that is, by humans. You can guess that this work would be highly repetitive and burdensome, as well as –due to its proximity to the machine –potentially dangerous.
As qualified workers become difficult to find, many manufacturers are turning to automated machine tending solutions in the form of cobots. Collaborative robots can feed parts to machines for long periods of time without interruption, thereby freeing up operators to focus on more invigorating and creative tasks.
2.Assembly
As with machine tending, assembly can involve tasks that are dangerous for humans to perform. In addition, fitting parts together requires extremely high precision and accuracy, and today’s labor shortage and high turnover rate means that companies are spending excessive amounts of time training human resources.
Since cobots can perform a variety of extremely high-precision tasks with minimal downtime, they’re an excellent option for assembly applications. Their compact form factor and lack of caging helps them fit easily into the most space-constrained applications, leaving room for other needs as they arise.
3.Packaging
Packaging and palletizing applications are known for causing repetitive stress injuries and lifting-related musculoskeletal problems among workers.
Collaborative robots can greatly ease this strain and boost productivity by taking over the heavy lifting. They can also make it easier for companies to scale up during busy seasons, since hiring additional workers can be difficult.