Understanding the Ramifications of Damaged and Incorrect Labels
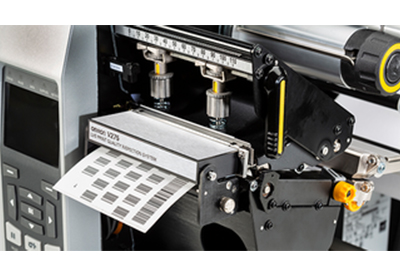
May 3, 2021
What drives the requirement for accurate, high-quality labels? With so much hanging in the balance for manufacturers and retailers competing on a global scale, there’s no good reason to ignore the need for label quality. Mislabeled packaging could have consequences that range from wasted product to (potentially severe) consumer health issues.
Let’s take a look at four major areas that illustrate the importance of ensuring the accuracy and legibility of product and packaging labels and discuss a solution that can help avoid errors.
Area 1: General product traceability
Product traceability, in a general sense, is essential for consumer safety, regulatory compliance and overall quality perception. If there’s a problem with a product, traceability allows the consumer, retailer or another entity to quickly locate and segregate defective products in the event of a recall.
Area 2: Life sciences industry regulations
In most life science-related industries, and particularly in the medical device and pharmaceutical industries, there are regulatory requirements requiring that labels show the correct content, are legible and contain barcodes of a minimum quality.
Noncompliance with respect to labeling can lead to FDA warning letters or even recalls, and label issues have historically been one of the top three causes of recalls in the pharmaceutical industry. According to the Sedgwick Brand Protection Recall Index, there was a 22% increase in medical device recalls from 2019 to 2020.
Large retailers are also working to ensure quality compliance for pharmaceutical products. Amazon, for example, has begun imposing FDA labeling requirements on firms selling supplements on its site. If a seller can’t demonstrate this compliance, the product will be removed.
Area 3: Customer-driven labeling specifications
Many manufacturers of higher-value or higher-risk items rely on proprietary, serialized label content to help mitigate that risk of counterfeit products entering the supply chain. Label authenticity can be controlled and verified by means of label inspection and serialization.
As an example, the recent report of counterfeit 3M N95 masks entering the U.S. supply chain highlights the need for anti-counterfeiting strategies.
Area 4: Safety and brand protection
Most retailers require their suppliers to conform to certain specifications that define label content and printing quality. If retailers cannot receive product due to a poor quality or incorrect information within the barcode, they often return the product and issue a financial penalty to the supplier.
For example, one major retailer charged a supplier of brooms and mops fines in excess of $100,000 due to the use of an incorrect barcode type on the product packaging. This issue led to the supplier adopting a printer-integrated label inspection system to avoid such errors in the future.
The power of printer-integrated label inspection
Printer-integrated label inspection systems are a highly effective way to prevent labeling errors and ensure that only high-quality barcodes make it onto final packaging. These systems are capable of analyzing 100% of all labels produced in a way that doesn’t slow down production. If an error is discovered, the system can be programmed to stop all printing immediately.
In the long run, automated label inspection can dramatically increase a company’s competitive advantage by minimizing the likelihood of hefty fines or dissatisfaction among retailers and consumers.