Small-Scale Automation – Why Size and Reach Matter
May 6, 2025
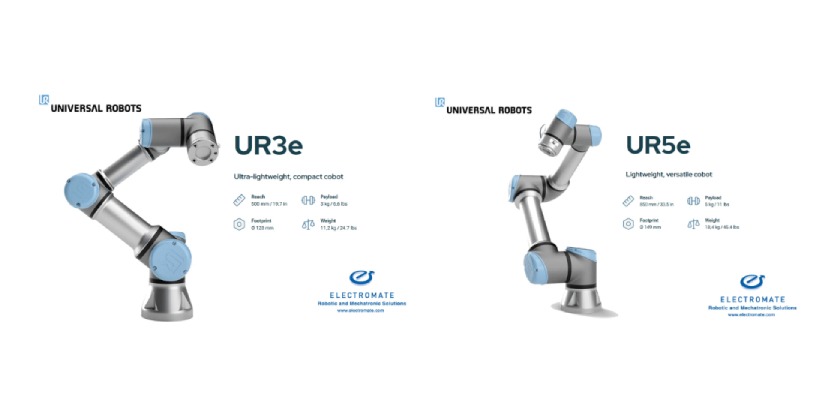
In small-scale automation, choosing the right robotic arm is less about raw power and more about precision, flexibility, and footprint. Workspace constraints, task complexity, and integration costs all scale differently at the bench or cell level than they do on a full production line. In these environments, size and reach are critical differentiators, directly impacting the success and ROI of any collaborative robot deployment.
Why Size Dictates Deployability
Most small manufacturers, startups, and research facilities don’t have the luxury of reconfiguring an entire production floor to install automation. They need robots that fit existing workbenches, CNC stations, inspection cells, or mobile carts. Collaborative robots like the UR3e are designed for exactly these constraints.
At just 11.2 kg with a compact footprint, the UR3e can be mounted on a tabletop and deployed by a single technician. It doesn’t require safety fencing and can be relocated quickly for multi-purpose use. This makes it ideal for lean production environments, R&D labs, and pilot automation cells where flexibility is more valuable than brute strength.
Reach Sets the Work Envelope
Reach determines how far the cobot can move its end effector from its base—crucial when trying to automate multiple steps within a single small cell. Too little reach limits access to tool positions, part bins, or machines. Too much reach in a confined space results in inefficiencies or physical interference.
- The UR3e, with a 500 mm reach, is optimized for tight stations where precision handling of small parts is the priority.
- The UR5e, with 850 mm of reach, provides extended access for tasks like multi-part testing, light assembly, or flexible inspection routines in midsize cells.
- Oversizing your reach can introduce unnecessary cost and increase programming complexity without functional benefit.
Application Examples Where Size and Reach Matter
Electronics Assembly: Small PCBs and components demand high repeatability and minimal footprint. A UR3e can complete pick-and-place and soldering with no wasted motion.
Lab Testing & Inspection: Cobots in medical or material testing labs need to access instruments, place samples, and operate devices—all within confined bench space.
Startup Automation Cells: New manufacturers looking to automate light tasks—like screwdriving or machine tending—need systems that deploy fast and adapt easily.
The Risk of Over-Specifying
Deploying a larger, higher-payload robot than required creates hidden inefficiencies:
- Slower movement speeds due to added inertia
- More complex programming to avoid collisions
- Unnecessary cost in hardware and integration
When the goal is agility, compactness and right-sized reach often produce better throughput and faster payback than bigger systems.
In small-scale automation, size and reach aren’t just specs—they are constraints that define whether your automation works at all. Collaborative robots like the UR3e and UR5e are built to meet these challenges. Choosing a cobot with the smallest footprint and shortest reach that still meets your task requirements results in faster deployment, greater efficiency, and a more scalable path to automation.
Related Story
Electromate Announces 2025 Collaborate Canada- A Collaborative Robot (Cobot) Automation Fair in Toronto
Electromate is pleased to announce it will be hosting a Collaborate Canada Cobot Automation Fair on Tuesday, May 27, 2025, in in Toronto, Ontario.
This complimentary event is ideal for End Users, Machine Builders, and System Integrators looking to automate a production process.