Safely Testing For Absence of Voltage
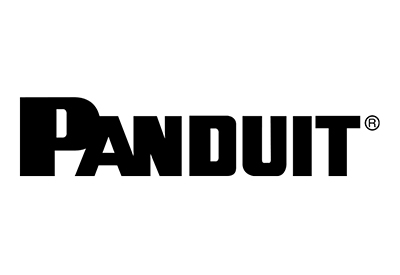
September 28, 2021
De-energizing equipment, following adequate lockout/tagout procedures, and verifying the absence of voltage are key components to establishing an effective foundation for an electrical safety program. Even though there has been significant progress in bringing awareness to electrical hazards in the workplace and the importance of establishing a strong electrical safety program, the electrical injury rate remains stable. Employees performing service or maintaining equipment can be exposed to grave physical harm or even death if hazardous energy is not properly controlled. Following an effective electrical safety program, properly de-energizing equipment, and verifying the absence of voltage before performing work can help to reduce the possibility of a dangerous electrical incident. However, the critical step of verifying the absence of voltage is often overlooked or performed incorrectly because the process is time consuming and cumbersome. This paper examines the challenges surrounding the voltage verification process and offers a solution that improves electrical safety by reducing the likelihood of distraction and human error.
The Rate of Electrical Injuries
Exposure to electricity continues to be a leading cause of injury and death among workers. Violations of electrical standards and lockout/tagout procedures were two of the Occupational Safety and Health Administration’s (OSHA) top ten most frequently cited standards in 2017. Data from the U.S. Bureau of Labor Statistics indicates that in the period from 2003 to 2012, there were more than 24,100 nonfatal electrical injuries and nearly 2,000 electrical fatalities. Even more alarming, these numbers are likely underreported. Furthermore, there has been little change in the nonfatal electrical injury incident rate over the past decade.
One of the leading causes of both fatal and nonfatal electrical injuries is contact with wiring, transformers, or other electric components. This category accounted for 29% of electrical fatalities from 2003 to 2010 and 36% of nonfatal electrical injuries from 2004 to 2010.2,3 The Electrical Safety Foundation International performed an analysis indicating that over the past 20 years the percentage of injuries attributed to this category has remained constant.
Incidents in the workplace resulting from contact with exposed wiring, transformers, or other electrical components may involve construction, installation, maintenance, and repair work. Primary injuries resulting from these and other electrical incidents include electrical shock, thermal burns, or a combination of the two.
According to a study concerning arc flash injury data analysis, the most common work task leading to arc flash injury is workers replacing fuses without turning off the power and verifying that equipment is de-energized.
Testing for Absence of Voltage Using a Hand-held Device
Verifying the absence of voltage is part of the process to establish an electrically safe work condition. Even after de-energizing equipment and following lockout/tagout procedures, workers must treat equipment as if it is energized until proven otherwise. The process to verify that equipment is de-energized is described in NFPA 70E. Traditionally, this process involves the use of a portable, hand-held voltage test instrument, but another option is presented in the latest edition of NFPA 70E.
According to Step 7 of NFPA 70E-2018 Article 120.5:
Use an adequately rated portable test instrument to test each phase conductor or circuit part to verify it is de-energized. Test each phase conductor or circuit part both phase-to-phase and phase-to-ground.
Before and after each test, determine that the test instrument is operating satisfactorily through verification on any known voltage source.
Exception No. 1: An adequately rated permanently mounted test device shall be permitted to be used to verify the absence of voltage of the conductors or circuit parts at the work location, provided it meets the following requirements: (1) It is permanently mounted and installed in accordance with the manufacturer’s instructions and tests the conductors and circuit parts at the point of work; (2) It is listed and labeled for the purpose of verifying absence of voltage; (3) It tests each phase conductor or circuit part both phase-to-phase and phase-to-ground; (4) The test device is verified as operating satisfactorily onany known voltage source before and after verifying the absence of voltage.
Limitations of Portable Testers
Using portable, hand-held testers requires workers to be exposed to electrical hazards when testing for voltage and when verifying that the tester is operating before and after the test. When performed properly, this process can be very effective; however, any deviation from the process or improper use of personal protective equipment (PPE) can put worker safety at risk.
Wear and Tear
Portable hand-held voltage testers are susceptible to mechanical and electrical failure and worker misuse. Workers must regularly inspect handheld voltage testers to guard against failure from wear, the impact of being dropped, and the harsh environment of the factory floor.
Human Error
Devices that require workers to manually select settings and use interchangeable test leads are susceptible to user error. Not only could this produce erroneous readings, it may cause injury if the leads are not properly installed or applied to the correct test point.
Rating of Test Instruments
With portable equipment, it is important to ensure that the test instrument is rated for the application. One of the most common causes of voltage testing errors is the use of an inadequately rated tester. Using a test instrument on a source that exceeds its voltage rating can result in failure or damage to the tester and injuries to the worker.
Inadequate or Incomplete Training
Training workers on the selection, maintenance, and use of hand-held test instruments is crucial to ensuring safety. Hand-held test instruments have limitations and if a worker does not understand these limitations, errors can occur. For example, if there is unexpected downtime, a worker in a rush to repair equipment may use a borrowed tester. If the worker is unfamiliar with the borrowed tester, errors can occur.
Exposure to Hazards
Another disadvantage of implementing a voltage verification test with a hand-held tester is that the worker performing it may be inadvertently exposed to electrical hazards. This could occur before the test when testing the tester, during the test if the panel is not de-energized, and after the test when re-verifying the hand-held tester. Because an enclosure must be accessed while performing the voltage verification test with a hand-held test instrument, there is potential for significant risk of exposure to electrical hazards.
A Safer Way – VeriSafe Absence of Voltage Tester
The VeriSafe Absence of Voltage Tester (AVT) is the first absence of voltage tester listed to UL 143611 designed specifically to verify the absence of voltage in electrical enclosures.
The VeriSafe AVT reduces the risk of exposure and helps eliminate user error. With a built-in self-test mechanism, there is no need to access a separate known voltage source to verify that the tester is functioning. Operating the AVT will not expose workers to electrical hazards.
Hand-held voltage testers possess certain limitations when used for verifying the absence of voltage, such as worker misuse, mechanical and electrical failure, inadequate application rating, inadequate or incomplete worker training, and possible inadvertent exposure to electrical hazards while verifying the absence of voltage.
In comparison, the VeriSafe AVT presents the following advantages over hand-held voltage testers when verifying the absence of voltage:
- • Allows the operator to test for absence of voltage without exposure to electrical hazards, before removing doors and covers on electrical equipment
- • Automated test sequence reduces procedure time, complexity, and human error
- • Reduces errors due to inadequately rated testers and incorrect tester settings
- • Self-contained solution — does not require additional tools, equipment, or voltage source
- • Less susceptible to damage than portable, hand-held equipment
- • Provides a visual alert to abnormal power conditions by indicating when voltage is present (red LEDs)
- • Confirms absence of AC and DC voltage with a single test
VeriSafe AVT – The Safe, Efficient, Accurate Way to Verify
The VeriSafe AVT safely, reliably, and efficiently verifies the absence of voltage before workers access potentially dangerous electrical equipment. This results in a significant increase in worker safety when verifying the absence of voltage in electrical equipment and can reliably be done in a fraction of the time compared to portable testers. AVTs complement any lockout/tagout program while improving safety and efficiency hazards.
Visit http://www.panduit.com/verisafe for more information.