Will the Current Pandemic Affect Functional Safety? Some Thoughts From Omron’s Experts
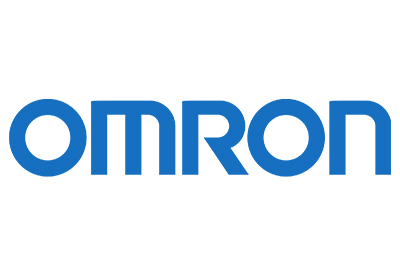
June 30, 2020
By Tina Hull, Technology Development Engineer, TUV Functional Safety Expert
COVID-19 is impacting society in a myriad of ways. Although restaurants, clinics, grocery stores and entertainment venues are experiencing the most obvious changes, the manufacturing industry is also being affected, including when it comes to functional safety. Let’s take a look at the ways in which the pandemic may create new challenges for manufacturing employees.
Efforts to rationalize the pandemic may cause biases
COVID-19 is challenging society with a “black swan event” – a major occurrence that comes about as an outlier, dramatically impacts society, and prompts people to rationalize it in detail after the fact. The idea of black swan events was put forth by Nassim Nicholas Taleb, a Lebanese essayist, scholar and statistician.
According to Taleb, a black swan event can alter rational thought processes depending on how the matter is presented, and people tend to look for more instances that confirm their worldview. This is how biases get formed, and they can lead to poor conclusions while amplifying the emotional impact of the situation.
Biases can prompt the formation of new habits
Biases are based on a specific view of the world that may have been formed from past experiences. Some individuals may create a bias as a way to provide protection from undesirable situations. In the case of COVID-19, typical biases that may result could include the following:
- – Assuming all germs – viruses and bacteria alike – are bad. (In fact, some bacteria are essential for good health.)
- – Equating organized workspaces with cleanliness. (It’s not necessarily true that people with messy offices aren’t disinfecting their workspace.)
- – Assuming that masks will be effective simply because people wore them in past epidemics. (It’s important to consider variables like the material, the environment, and the true impact of the virus.)
These biases can lead to behavioral changes, some of which could negatively impact productivity. Some habits an operator may require in response to the pandemic include the following:
- – Using hand sanitizer constantly after touching something. (This can give a false sense of security due to a lower effective rate and less friction during use.)
- – Maintaining an altered perception of cleanliness. (This could include polishing something until it shines even if that might not be necessary.)
- – Stopping work on a task in response to someone sneezing or coughing nearby. (In fact, the sneezing could be due to allergies rather than an infection.)
Biases could also lead to harmful reactions, like dropping a heavy load in an attempt to protect one’s face from a coughing coworker, or to poor performance due to anxiety about being contaminated.
Operators returning after a long work hiatus may need to readjust
Being away from a task for an extended amount of time, whether planned or unplanned, can result in a temporary readjustment as employees recall and resume their normal routines. The period of readjustment is expanded when it includes dramatic changes and a general atmosphere of uncertainty.
Re-evaluation of risk assessments before the return of the workforce can lead to potential solutions for easing the transition. Some things to consider include the following:
- – Operators may forget steps that used to come naturally, increasing the likelihood of an accident.
- – Equipment power-up is not part of the normal process, so tasks must be performed carefully.
- – Additional cleaning procedures may need to be implemented.
- – Work shift changes may need to be enacted to enable social distance.
- – The number of operators at any given time will likely change.
Equipment may be less efficient or more prone to failures due to the long period of non-use.