Energy Efficiency Is the Best Way for Industry to Cut Costs and Reduce Emissions Right Now
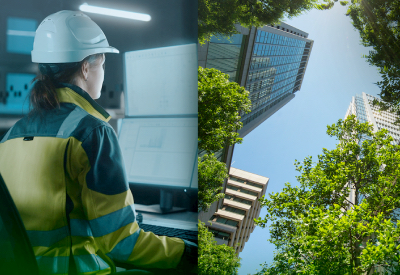
November 29, 2022
- •Independent report highlights 10 actions to help industrial users improve their energy efficiency right now
- •Improving energy efficiency will reduce energy bills and emissions substantially in the short- to mid-term, without compromising productivity
- •Industry is the world’s largest consumer of electricity, natural gas and coal, and accounts for 42 percent of electricity demand
With businesses around the world facing unprecedented pressure from the cost of energy and the urgency of climate change, a new report from the Energy Efficiency Movement shows that improving industrial energy efficiency is the fastest and most effective way for a business to cut energy costs and greenhouse gas emissions. The Energy Efficiency Movement is a global forum of around 200 organizations sharing ideas, best practices and commitments to create a more energy-efficient world.
Published recently, the “Industrial energy efficiency playbook” includes 10 actions that a business can take to improve its energy efficiency, reduce energy costs and lower emissions right now. It focuses on mature, widely available technology solutions that will deliver rapid results and ROI – and are capable of being deployed at scale.
“Energy efficiency is a win-win for companies and the climate,” said Kevin Lane, senior program manager, energy efficiency, with the International Energy Agency (IEA). “While industry needs to address climate change on all fronts – such as increasing use of renewable energy, investing in low-carbon processes and developing circular business models – energy efficiency stands out as the business-focused opportunity with the best near-term prospects for emission reductions. The 10 actions contained in this report are known, cost-effective resources, and can be employed at scale rapidly to help companies convert climate ambition into action.”
Industry is the world’s largest consumer of electricity, natural gas and coal, according to the IEA, accounting for 42 percent of total electricity demand, equal to more than 34 exajoules of energy.1 The iron, steel, chemical and petrochemical industries are the largest consumers of energy among the world’s top-five energy-consuming countries – China, United States, India, Russia and Japan. This energy consumption carries high costs in the current inflationary environment. It was also responsible for nine gigatons of CO2, equal to 45 percent of total direct emissions from end-use sectors in 2021, according to the IEA.
Organizations interviewed for the report include ABB, Alfa Laval, DHL Group, the IEA, Microsoft and ETH Zürich, the Swiss federal institute of technology. The contributors’ recommendations range from carrying out energy audits to right-sizing industrial machines that are often too big for the job at hand, which wastes energy. Moving data from on-site servers and into the cloud could help save around 90 percent of the energy consumed by IT systems.2 Speeding up the transition from fossil fuels, by electrifying industrial fleets, switching gas boilers to heat pumps or using well-maintained heat exchangers will also offer efficiencies.
The “Industrial energy efficiency playbook” includes 10 actions that a business can take to improve its energy efficiency, reduce energy costs and lower emissions right now
Further actions involve installing sensors and real-time digital energy monitoring to reveal the presence of so-called “ghost assets” that use power when on stand-by, unlike a digital twin that can simulate efficiency actions without interrupting production. Using smart building solutions to control power systems, lighting, blinds and heating, ventilation and air conditioning (HVAC) will also save energy in industrial facilities.
Other recommendations include installing variable speed drives which can improve the energy efficiency of a motor-driven system by up to 30 percent, yielding immediate cost and emissions benefits. If the more than 300 million industrial electric motor-driven systems currently in operation were replaced with optimized, high-efficiency motors, global electricity consumption could be reduced by up to 10 percent.
“There are energy efficiency solutions available that can help industry mitigate climate change and drive down energy costs, without compromising performance and productivity,” said Tarak Mehta, president, Motion business area at ABB. “With recent technology advances in energy efficiency, the improvement potential in industry is significant and readily available. So, rather than turning the lights off and halting production to save money, this important new report explains practical steps executives can take to reduce energy use and their bills while maintaining current operations.”
Business leaders and experts wanting to learn more about reducing their energy costs and carbon emissions are invited to join a special panel event that dives deep on the opportunities presented in the report and how to capitalize on them. The event will take place at 4pm Central European Time / 10am Eastern on Tuesday, December 13, and will be available afterward as video on demand. Register here.