Condition Monitoring and Predictive Maintenance with IO-Link Rotary Encoders
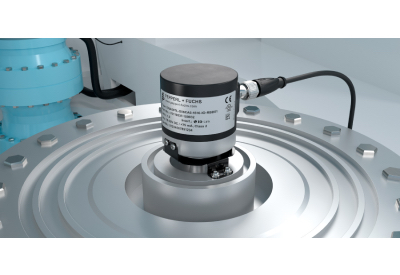
January 11, 2022
Whether in the material handling industry, in packaging machines, or in wind turbines—sensors with IO-Link interface are increasingly being used to pave the way to Industry 4.0. With the ENA**TL-**IO-Link, Pepperl+Fuchs was one of the first manufacturers to launch an absolute rotary encoder with IO-Link interface, which is available in numerous variants and with a wide range of setting parameters. Pepperl+Fuchs explain how you can benefit from easy configuration and integration with this IO-Link rotary encoder, while at the same time monitoring the status of your plants in a cost-effective manner.
Why Rotary Encoders with IO-Link?
The internationally standardized IO-Link interface enables continuous communication between the control level and the individual sensors at the field level. Sensors equipped with IO-Link not only fulfill their actual sensor function, but also create the basis for systematic diagnostic concepts. Therefore, the condition of machines can be continuously monitored so that failures and downtimes can be prevented through predictive maintenance.
The use of intelligent, communication-capable rotary encoders is an easy way to implement condition monitoring and predictive maintenance: this way, no high investments are required for retrofitting the plant. Since other sensor technology, for example in material handling technology, is also increasingly being converted to IO-Link, the IO-Link rotary encoder fits seamlessly into the overall concept of many industrial plants. Furthermore, the measured values are transmitted at a speed of 230.4 kBit/s via COM3—the highest transmission speed in the IO-Link standard.
Sophisticated Functionalities
Pepperl+Fuchs offers a wide range of IO-Link rotary encoders in different mechanical variants that can be implemented in all common applications for absolute rotary encoders. Due the magnetic detection principle, the sensors are robust and wear-free, and precisely detect the rotation angle of the encoder shaft. In addition, the ENA**TL-**IO-Link comes with a multitude of sophisticated functionalities:
- The multiturn function enables the mapping of cyclic applications.
- The preset function allows position values to be adjusted during operation. This way, inaccuracies caused by slip can be compensated for without the need for time-consuming readjustment.
- The rotary encoder not only measures position values in rotating movements, but also temperature values. This makes it possible to draw conclusions about the condition of the machine.
- Critical position and temperature ranges—so-called signal flags—can be individually defined. As soon as a critical value is reached, the machine can be switched off automatically.
Easy Commissioning Due to IO-Link
The IO-Link interface not only enables condition monitoring and predictive maintenance, but also facilitates configuration and integration of the rotary encoder. Via an IO-Link master, the ENA**TL-**IO-Link can be parameterized more quickly and easily than conventional rotary encoders. The IO-Link master offers extensive configuration options: the parameters can be easily adapted via software tools. On request, the rotary encoders can also be delivered with customer-specific parameter adaptation, even in small quantities.
Our customers also benefit from the advantages of the IO-Link interface when replacing the sensors: Since the setting parameters are stored both in the rotary encoder and in the IO-Link master, there is no need for time-consuming re-parameterization. This saves time when replacing sensors in existing systems.
Three Practical Application Examples
Typical applications for the ENA**TL-**IO-Link are positioning and length measurement tasks, for example on conveyor belts, cranes, elevators, and packaging machines. In the following, you will learn more about three practical application examples.
On Conveyor Belts
IO-Link sensor technology is already widely used in conveyor technology. Therefore, the IO-Link rotary encoder fits perfectly into the overall architecture of existing plants: Since all components are based on the same standard and can be commissioned in a similar way, the management and maintenance effort is reduced.
For example, the ENA**TL-**IO-Link is used on conveyor belts in beverage filling machines. Depending on the type of bottle, the width of the conveyor belt must be flexibly adjusted so that the bottles run in an accurate row for filling and labeling. Attached to an automatic crank wheel, the IO-Link rotary encoder uses the adjustable signal flags to provide information on whether the new conveyor belt width has been correctly implemented by the motor.
In Wind Turbines
Due to its robust design, the ENA**TL-**IO-Link is also suitable for use in harsh environments—for example, in wind turbines. Here, it detects the position of the nacelle as part of the azimuth control to determine whether the alignment to the wind has taken place correctly. At the same time, it measures how often the nacelle has already been turned in which direction. This makes it possible to decide whether the turbine must be turned to the left or to the right in order to prevent a cable break between the nacelle and the tower. With its painted and galvanized housing, a flange made of aluminum and an encoder shaft made of V2A stainless steel, the sensor is protected against corrosion. In accordance with the degrees of protection IP65 and IP67 (extra charge), it is also insensitive to splash water and temporary submersion. Therefore, the rotary encoder can easily handle weather conditions like rain or snow.
On Ship Cranes
Due to its high resistance, the ENA**TL-**IO-Link is also suitable for offshore environments: The mechanical parts of the sensor are protected against the effects of salt and the associated risk of corrosion, as well as against splash water and temporary submersion. In cranes that are used for loading and unloading on ships, the rotary encoder can be employed to monitor the horizontal and vertical movement of the machine. Since the rotary encoder is installed inside the equipment, its inherent protective measures are sufficient so that a heavy-duty rotary encoder is not necessary.
Additional Information
Interested in using the ENA**TL-**IO-Link in your plant? Experts at Pepperl+Fuchs look forward to your inquiry, and will be happy to support you in making the best choice.
Learn more here:
Product Selection ENA**TL-**IO-Link rotary encoder
More about sensors and systems with IO-Link
The complete portfolio of rotary encoders by Pepperl+Fuchs