Why Integrated Safety Is the Right Strategy for Large, Complex Applications
July 18, 2023
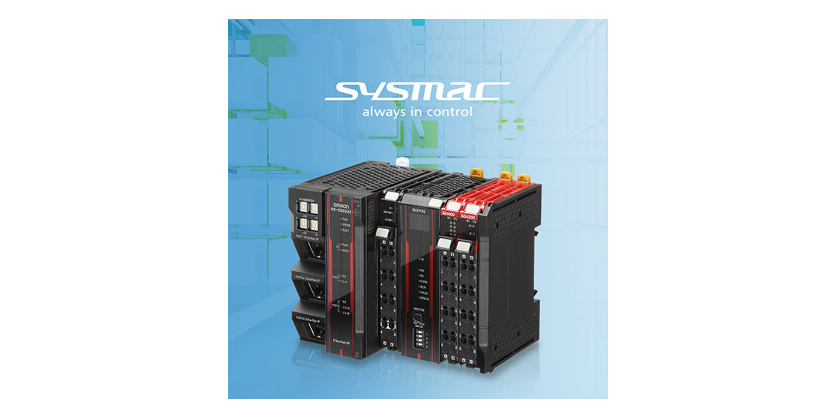
During the safety design process for a machine or application, manufacturers must choose whether these measures will be implemented as a standalone or networked (integrated) safety solution. Basic safety solutions can work for smaller-size applications, but then we are talking about large automotive production lines, for example, complexity makes these unworkable.
Integrated safety isn’t just a highly effective way to mitigate risk. In fact, it’s a key element in building a high-performing, future-ready manufacturing facility since it’s capable of improving automation efficiency and boosting throughput.
Omron takes a look at the differences between standalone and integrated safety — and why the latter is important for large, highly complex applications.
What goes into a basic (standalone) safety system?
Basic safety involves an input device, a logic device, and an output device. This configuration can be abbreviated as ILO for “input, logic, output.” One input device, one logic device, and one output device constitute a complete standalone system, and each of these will be a discrete device that’s hardwired.
- An input device — which could be a light curtain, a scanner, a door interlock, a safety mat, or the like — detects human incursion into an automation workspace. E-stops also count as input devices, even if they require a human to purposefully activate them, rather than simply detecting human presence.
- A logic device takes the input, decides whether the input is a valid safety signal, and then makes a safety-related decision to interrupt primary power to a machine and remove any energy that pose a hazard. Examples of such hazards could be machine motion, arc flashes, or high-pressure water.
- An output device removes the energy from the hazardous situation. For electrical power, the device will usually be contactors. For rotating and/or moving hazards, it might be a clutch brake, which separates a blade from its motor and forces the blade to stop instantly while allowing the motor to coast down.
Detecting human incursion isn’t the only job of a safety system. If a copper wire within the system gets cut, for example, the system will detect that as well, since this could lead to potentially hazardous machine failure or dysfunction within the safety system itself.
Discover Omron’s full range of safety solutions
How integrated safety builds upon the ILO concept
When you have a complex production line that has large assemblies with robots lifting heavy parts right and left, there are lots of forces and individual hazards to deal with. Each of these hazards must be considered within the context of the larger system, so that shutting down one machine on the line won’t necessarily result in an entire line stoppage.
The goal here is to create a network integrated safety system where you’re not simply adding a layer of safety over an already-designed production line. To ensure that all hazards are safeguarded and that the line will function as smoothly as possible, safety can’t just be an afterthought. This is where integrated safety comes in.
In integrated safety, you still need input, output, and logic devices, but you combine multiple smaller safety modules into a comprehensive safety “umbrella” that works like an orchestra. All the ILO devices are tied together via a communication network that can quickly communicate any legitimate safety trips. When someone’s limbs (and possibly life) are in danger, speed is key.
Need help understanding machine safety requirements? Learn about Omron’s safety services
Distributed vs. centralized systems in integrated safety
Integrated safety systems can be either distributed or centralized. Distributed safety is a lot easier to wire, since wiring distances are shorter and there’s more flexibility in designing the safety matrix (the directions that indicate which energy sources should be shut down for different specific hazards).
Each of these remote hubs would collect the individual wiring inputs from the input devices and then communicate their actions via communications line. Centralized wiring would require running all the leads back to the control panel where the distances, complexity, time, and effort of this would be significantly greater.
More Information
Integrated Safety Solutions Improve Safety management
Related Story
Omron’s Robotic Solutions: Thousands of Possibilities
Robots can improve the productivity of many industries and processes. They can handle a variety of tasks, such as laborious or repetitive work, and can dramatically improve processes in industries such as machine tending, assembly, packaging, and other manufacturing activities. Moreover, they can handle routine operations, allowing employees to perform higher-value tasks.
This article will look at a selection of Omron’s robots and robotic solutions, such as autonomous robots and collaborative robots, and will explore how these products can be integrated into facilities to improve productivity. It also discusses the next evolution in factory automation: MoMa’s, or Mobile Manipulators – the growing trend of having collaborative robots mounted onto AMRs to achieve new levels of automation.