Will Automation become Autonomous thanks to Artificial Intelligence?
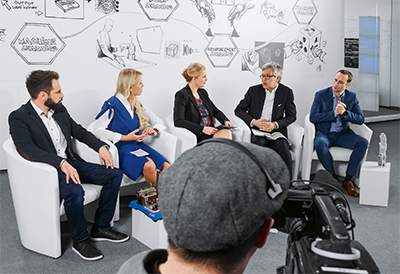
March 4, 2019
Artificial intelligence and human-machine cooperation are the major topics of the automation of the future. The Hannover Messe 2019 trade fair will also be held under the motto “Integrated Industry – Industrial Intelligence”. At the Festo TechTalk held at the end of February, four experts discussed the potential and opportunities offered by artificial intelligence and explained how Festo is positioning itself within this context.
How does anticipatory machine maintenance work? How is artificial intelligence advancing automation? And how can Germany as an industrial location benefit from these activities? Answers to these questions were provided by Dr Frank Melzer, Member of the Management Board Product and Technology Management; Tanja Krüger, Managing Director of Resolto Informatik GmbH (a company of the Festo Group); Dr Elias Knubben, Head of Corporate Research and Innovation; and Dionysios Satikidis, Digital Strategy and Business Model.
Will automation become autonomous thanks to artificial intelligence? This question was put forward by Dionysios Satikidis, a software engineer and expert in artificial intelligence, in his opening presentation. He used the example of newborn babies to explain various learning methods in artificial intelligence that can ultimately lead to autonomy. Babies first of all perceive objects, and this enables them to recognise differences – which is exactly what algorithms can do in machine learning, for example when recognising anomalies or clusters. When systems also remember what they perceive, this is known as deep learning. They can then recognise objects or understand speech. If this memory is connected with a task and practised, one then speaks of reinforcement learning. In this case, it involves learning a skill. “Once artificial intelligence finally becomes capable of transferring acquired knowledge to unknown tasks, we will have arrived at transfer learning, which in the final stage can lead to autonomous automation,” said the expert with a view to the future.
BionicSoftHand – a pneumatic gripper with AI based on the human model
Dr Elias Knubben showed an example of how Festo can use reinforcement learning for automation engineering: the Head of Corporate Research and Innovation presented the BionicSoftHand, the new Future Concept from the field of bionics. The natural model for this gripper is the human hand. The BionicSoftHand is pneumatically operated so that it can interact safely and directly with people. Its fingers consist of flexible bellows structures with air chambers and other soft materials. This makes it light, flexible, adaptable and sensitive, yet capable of exerting strong forces. By means of artificial intelligence, the bionic robot hand learns to independently solve gripping and turning tasks similar to the human hand in interaction with the brain (see press release on the 2019 bionic projects).
Intelligent process monitoring
Artificial intelligence has been made usable to industry by Tanja Krüger, Managing Director & Owner of Resolto Informatik GmbH (a company of the Festo Group since 2018). This theoretical computer scientist, a pioneer in the field of data analytics, founded Resolto in 2003. Visitors to the booth of Festo at the Hannover Messe can see how the intelligent monitoring software SCRAITEC analyses and interprets data, and detects and reports anomalies, all in real time. The permanent data analysis also enables the system to constantly learn and extend its basis of knowledge, so that intelligent process monitoring is possible. “In Hanover we will be demonstrating how our software works in a showcase for the detection of faulty batteries. The batteries are lifted by a handling gantry. SCRAITEC monitors the engine currents and positional values of the axis. If anomalies occur, for example if the handling unit grasps the wrong battery format, a report is issued,” said Tanja Krüger.
AI will enormously influence the product portfolio of Festo
“The acquisition and monitoring of data by the intelligent software solution can either be effected at the component, as with the handling of batteries, or be carried out via the IoT gateway CPX-IoT in the Festo cloud. It connects components and modules from the field level, such as handling systems or electrical drives, via its OPC UA interface to the Festo Cloud,” added Dr Frank Melzer, Member of the Management Board Product and Technology Management. “The topics of analytics and artificial intelligence will enormously influence our product portfolio in future. For simple analysis tasks, AI algorithms can run directly on the component in real time; we then speak of field level or on-edge. If I want to analyse the data flows of an entire machinery unit or even a production hall, the processing power within the component will of course not be sufficient. The servers for the more complex calculations can be integrated into the production network. The advantage: my data remain within my protected infrastructure and are not communicated via the Internet. It is only in the processing of very large volumes of data with complex analyses and reference series that communication with the cloud is necessary and appropriate.”
Festo at the Hannover Messe 2019 trade fair
From 1 to 5 April 2019, Festo will be showcasing the new Future and Bionic Concepts along with further product innovations for factory and process automation at its main booth in Hall 15, Booth D11.
A further stand with products from Festo can be seen at Siemens in Hall 9, Booth D35 in the Mindsphere Lounge. Here Festo will be presenting the field of energy monitoring via dashboards. At Microsoft in Hall 7, Booth C40 and at the OPC Foundation in Hall 9, Booth A11, the topic of “Motion controllers with OPC UA communication servers” will be on display. Festo will also be represented with a computer workstation at the booth of EPLAN in Hall 6, Booth H30. You can also visit the shared booths of PROFIBUS & PROFINET International (PI) in Hall 9, Booth D68 and “Plattform Industrie 4.0” in Hall 8, Booth D24. At the shared stand of the technology initiative SmartFactory e.V. (Hall 8, Booth D18), Festo AG & Co. KG and Festo Didactic SE will be participating in the non-proprietary demonstrator for Industry 4.0 and showing the use of Smartenance, the first IoT-capable maintenance management tool. You can also visit Eichenberger Gewinde AG (a company of the Festo Group) in Hall 16, Booth F08.