Siemens’ gearless drive technology powers high-capacity overland conveyor in Quellaveco
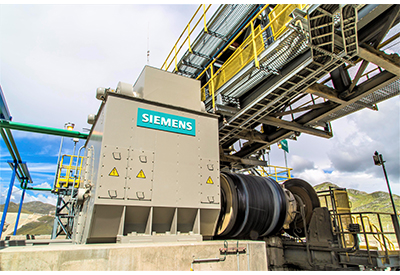
November 11, 2019
Powered by Siemens’ new gearless drive technology, thyssenkrupp’s high-capacity overland conveyor will access one of the world’s largest copper reserves in Quellaveco. The Quellaveco mine in Peru contains approximately 7.5 million tons of copper in ore reserves – enough to wire 80 million homes or equip 90 million electric vehicles.
With the rugged landscape in Quellaveco, transporting the primary crushed ore requires durable and efficient technology systems. By employing Siemens’ technology on this project, thyssenkrupp’s new conveyor system will transport 127,500 tons of primary crushed ore per day from the pit to the stockpile adjacent to the copper concentrator. Vast sections of the overland conveyor must traverse from one valley to another through a 3.2 km long tunnel. After exiting the tunnel, the conveyor will pass over hilly terrain before feeding the stockpile.
Compared with the combination of high-speed motor and gearboxes otherwise used in belt conveyor systems, the gearless drive solution offers a range of benefits. The size of the motor is not limited anymore by the size of gearbox, thus eliminating the necessity to install multi-motor drives. The required belt driving power can be provided with one drive per drive pulley. This means that the number of switchgear enclosure could also be scaled down, saving space and weight within the e-house. The elimination of a whole series of mechanical and electrical components increases the reliability and efficiency of the overall system by between 3-4%.
Another important factor is that the maintenance requirements of the drive system have been significantly reduced. This is important as gear maintenance work alone can account for up to 5% per year of the original investment volume for the gears.
thyssenkrupp’s overland conveyor is 4,700 m long, 1,830 mm wide featuring Siemens’ dual 5.5 MW gearless drives operating at a design tonnage of nearly 11,000 tons per hour. Siemens also provides the e-house with MV and LV power distribution and the cooling system for motors and e-house. The automation of the conveyor system as well as for the complete mine will be realized with the process control system Simatic PCS-7.
“This order again shows how gearless conveyor systems meet today’s demand for ever more efficient mining solutions and increased safety requirements,” Torsten Gerlach, CEO of thyssenkrupp’s Mining Technologies business unit explains. “It is the seventh overland conveyor project of this magnitude utilizing gearless drives that have been awarded to us since 2010. Together with our partner Siemens, we have managed to become one of the world leaders in bringing this technology to the market.”