Rittal establishes a smart factory
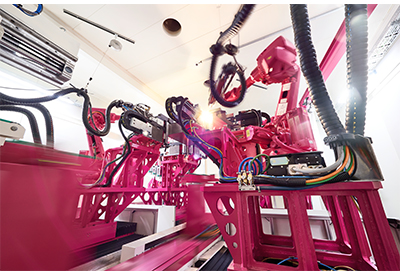
August 6, 2019
The new Rittal plant in Haiger embraces the principles of Industry 4.0. The company has made its largest single investment, totalling 250 million euros, to establish the world’s most advanced facility for its new compact and small enclosures. The highly automated manufacturing processes, in conjunction with the neighbouring distribution centre, enable seamless order fulfilment, guaranteeing rapid availability of standard products and accessories.
Rittal is putting Industry 4.0 theory into practice: the world’s leading provider of solutions for enclosures, power distribution, climate control and IT infrastructure, as well as corresponding software and services, is creating a smart factory – the world’s most advanced production plant for compact and small enclosures. “The plant is to be fully aligned with highly efficient Industry 4.0 principles,” states Professor Friedhelm Loh, Owner and CEO of the Friedhelm Loh Group. “The new manufacturing site will also safeguard future competitiveness for our customers and our own business. The total investment of 250 million euros is a positive statement in terms of the regional economy and the 290 jobs at our Haiger plant. We have quite consciously decided to proactively shape the future with the local people who made us what we are today.”
The new factory halls, with 24,000 square metres of floor space, will soon house more than 100 high-tech machines. Together they will manufacture some 9,000 AX compact and KX small enclosures daily, processing approximately 35,000 metric tons of steel annually.
Manufacturing in a smart factory
The equipment in Haiger will be highly automated, producing individual work pieces and assemblies with exceptional efficiency. In the past, individual steps such as cutting to size, edging, welding and painting were transactional, sequential and independent of one another. In the new era, all workers, machines and materials will be increasingly integrated into the manufacturing execution system. At the end of the process, the individual assemblies are automatically merged and a QR code is applied. This enables identification as well as the further processing by the customer.
The machines and handling systems communicate with each other and also with higher-level control systems via modern industry 4.0-capable communication networks. Materials and components will be moved by means of 20 automated guided vehicles. Packaging, marking and transfer to the distribution centre are also performed automatically. Knowledge-based “learning” systems will enable predictive maintenance, preventing faults from occurring and minimising downtime.
Automated order management and fulfilment will guarantee ongoing availability of standard products and accessories in the nearby global distribution centre, creating an end-to-end digital process chain, from configuration and engineering on the part of the customer to shipment of the end-product.
A new world of work in Haiger
The new era of industrial manufacturing will also usher in major changes for human workers. There will be fewer strenuous manual tasks, such as lifting and carrying. Instead, the focus will shift to controlling, monitoring and fine-tuning processes. “The expertise and capabilities of experienced employees are one of the keys to the success of smart factories: systems can only learn and gain intelligence if they are taught systematically by humans,” explains Professor Loh. Rittal proactively builds digital skills in the workforce through training courses held at its Loh Academy.
The new technologies will bring improvements to the working environment as a whole. The Haiger facility will be quiet, clean and energy-efficient. For example, waste heat from the new paint shop will be recovered and reused, e.g. for degreasing components or for heating the factory halls. Efficient use of water is also a high priority. Process water is managed within a closed-loop system, where it is cleaned and reused.
Digital value creation at the customer organisation
Rittal will be manufacturing the new AX compact and KX small enclosures at the new plant. Digital transformation has created new challenges in terms of the products themselves, the operating environment, and its availability. Rittal has therefore rethought and redesigned this offering in line with the imperatives of Industry 4.0. Rittal provides effective support for the entire value chain for the production of panels and switchgear, from engineering to ordering to automation. Its digital product twin delivers high-quality data for the entire design, configuration and manufacturing process. Following the successful launch of Blue e+ cooling units and VX25 large enclosures, the AX and KX products are now an integral part of this approach.
Digital transformation is vital to business success
The Haiger facility is a pilot for the real-world implementation of Industry 4.0 and will act as a role model for Rittal’s international operations. It will also be a pioneer and reference for Rittal’s own products and services in terms of the Industrial Internet of Things (IIoT). Blue e+ cooling units enhance the increase of energy efficiency and are integrated into the monitoring and energy management systems via the IIoT interface. The entire machine park permanently provides data from the control system and the current operating states. Production systems in the new factory are an ongoing source of actionable data on their operational status. In future, this information will be collected in an on-site edge data centre and analysed using powerful applications developed by sister company Innovo.