Safety Standard EN ISO 13855 for the Positioning of Safeguards
May 13, 2025
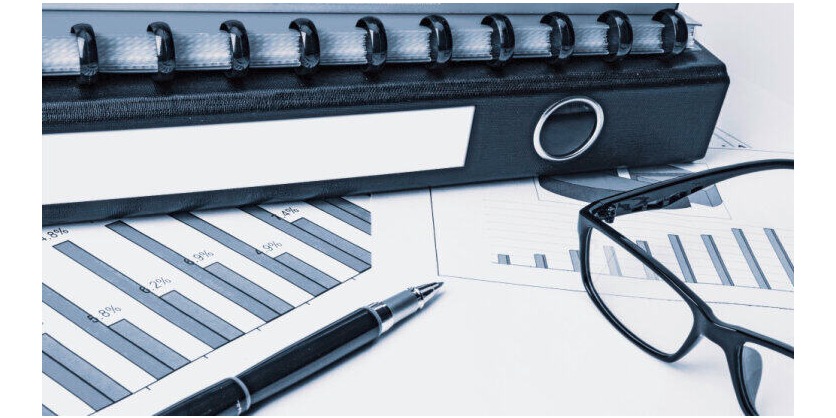
With safeguards on machinery, measures must be taken to guarantee the safety of human and machine. These measures are described in the standard ISO 13855 and ensure that the machine is brought to a safe state before the danger point can be reached. The safety distance must be selected in such a way that any dangerous movement comes to a standstill before any part of the body can reach the danger point.
The standard EN ISO 13855 “Safety of machinery – Positioning of safeguards with respect to the approach of the human body” defines the positioning of safeguards as well as the approach speed of humans. Both parameters need to be considered when designing safety measures and selecting the appropriate sensor technology. Different speeds and sizes are defined, depending on the direction and type of approach. Other aspects are also considered, such as indirect approach, the possibilities to circumvent safeguards and overrun measurement.
What’s new in EN ISO 13855:2024

The successor standard EN ISO 13855:2024 came into force in November 2024. There have been some important changes and some areas have been tightened up. Calculation of the safety distance is more complex and more structured in the new version, and requires some intensive study.
An overview of the key changes and new requirements:
- New, more complex supplements are now specified for safety distances.
- There is a definition of what constitutes a sufficiently large step surface, which can thus be used as a reference point for measuring the safety distance, also in relation to ascent or descent.
- The calculation of the safety distance must now also include the change in the position of the danger point in relation to the person, once the safeguard has been interrupted.
- The standard was extended to include the calculation of dynamic separation distances for known and unknown human directions of approach.
- Forms for manual switches and foot switches have been added and the formula for two-hand switches has been changed.
- New limits for vertical ESPE devices have been defined.
- There are extended calculations for interlocking guards.
Calculating the safety distance in accordance with ISO 13855:2024
The adjustments and new features of ISO 13855:2024 has resulted in the following formula for calculating the safety distance:
S = (K x T) + DDS + Z
S | The separation distance in millimetres (mm). S may not be less than 100 mm. |
---|---|
K | A parameter in millimetres per second (mm/s), which is derived from data on the approach speed of the body or parts of the body K is either 2000 mm/s for the speed of the upper limbs or 1600 mm/s for walking speed. If K = 2000 mm/s and S > 500 mm, 1600 mm/s can be used for K; however, in this case, S must be rounded up to at least 500 mm. |
T | The overall system response time in seconds (s); on new machinery it can be determined by measurement or by calculation. When measured, the highest value from 10 measurements is used. When calculated, T is a combination of 3 parameters: T = TSRP/CS (response time of the safety-related devices) + TME (time until the machine stops) + TF (tolerance factor) |
DDS | Supplements for the reaching distance associated with a protective device in millimetres DDS is the maximum of the possible supplements. Different ones may be applied. |
Z | An application-dependent supplemental distance factor, in millimetres. The value of Z depends on the precise application. Factors include measurement uncertainty, reflection, decreasing braking torque, for example. |
It should also be noted that a distinction must be made between two types of approach.
1. Static approach:
When calculating the safety distance for someone approaching a fixed safeguard, the end result depends on the type of approach. However, the main formula still applies:
S = (K x T) + DDS + Z
2. Dynamic approach for unknown human direction of approach:
If acceleration and deceleration are known and constant, the basic principle is the same as for the static approach, but an additional parameter SM must be taken into account, which represents the change in the position of the hazard. This results in the following formula, which is to be used when the human approach direction is not exactly known:
S = (K x T) + DDS + SM + Z
SM is calculated as follows:
SM = v0 x T – (d/2) x tm2 + (a/2) x tSRP/CS2
v0 | Starting speed in mm/s |
---|---|
a | Potential acceleration in mm/s² |
d | Potential delay in mm/s² |
tm | Time related to mechanical inertia |
tSRP/CS | The response time of the safety control system |
Pilz is happy to help!
To correctly calculate the safety distances in accordance with ISO 13855:2024, you need comprehensive knowledge of what is in the standards. The calculation or measurement should only be carried out by experienced personnel, or with specialist support. Pilz offers a comprehensive range of training or expert advice on site and helps you achieve sage, standard-compliant machinery.
More Information
Pilz consulting offer
Pilz’s consulting team can provide you with more detailed information and support when implementing the requirements of ISO 13855:2024. They will determine and evaluate all the relevant parameters for you and record them in a test document.
Pilz Safety Distance Calculator
Use Pilz’s Safety Distance Calculator to calculate the right safety distance for your safeguards in just a few steps.
Related Story
Safety Locking Device PSENmlock from Pilz
Safe interlocking and safe guard locking in one product!
The safety locking device PSENmlock offers safe interlocking and safe guard locking for personnel and process protection, up to the highest category PL e.
Safe guard locking is enabled by the dual-channel control on the guard locking device. As such, the switch is particularly suitable for use on machines with a hazardous overrun, which require safe guard locking up to PL d or PL e.
In conjunction with Pilz control technology, the result is a safe, complete solution for monitoring and activating guard locking on guards.