Siemens and UL Solutions Redefine Future of Certification Process with Groundbreaking Digital-Twin Technology
February 20, 2024
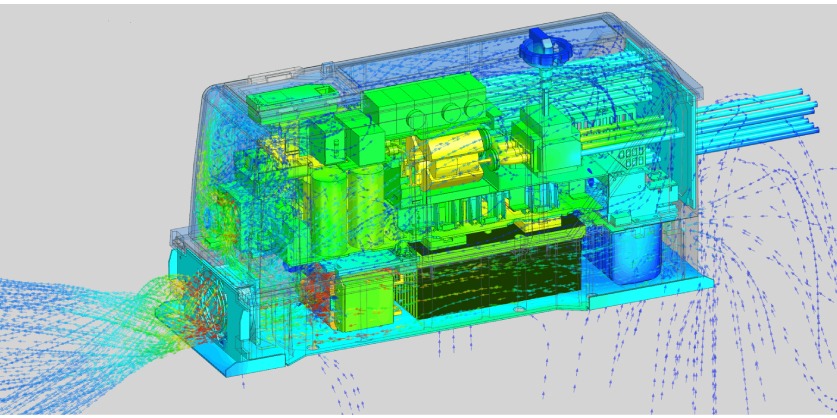
- Siemens and UL Solutions demonstrate a transformative shift from relying solely on physical tests to reliable integrating digital simulations.
- Reduced costs, accelerated time-to-market and seamless integration of digital modeling tools will redefine the future of verification.
- Siemens’ digital twin technology breaks through traditional testing boundaries, serving as a testament to the industrial metaverse’s potential for reshaping product development possibilities.
For the first time ever, an industrial product has been certified for the United States after parts of the required tests were conducted through digital simulation. That simulation was verified and validated with physical testing. This remarkable achievement is a global first in a national safety-certification process. To make this advance possible, Siemens collaborated with UL Solutions, an esteemed global leader in applied safety science. The result is a testimony to the remarkable accuracy and reliability of modern digital twin simulations. It marks a step forward into a future in which digital twins and the industrial metaverse streamlines product development, enhances innovation, safety and accelerates time-to-market.
Cedrik Neike, CEO Digital Industries and Managing Board Member at Siemens, said: “Siemens’ digital twin technology is rewriting the rules of innovation. This collaborative effort with UL Solutions is a testament to our dedication to a future in which innovation knows no bounds. It invites industries and innovators alike to explore the limitless possibilities that comprehensive digital twins offer for shaping the future of product development.”
“UL Solutions has always been at the forefront of advancing safety science. Our collaboration with Siemens in this transformative journey represents a significant shift in the certification paradigm,” Jennifer Scanlon, President and CEO of UL Solutions points out. “The certification process relies on physical testing. Now, digital simulations integrated with traditional methodologies can redefine how our customers approach testing and certification and open new avenues for precision and efficiency. UL Solutions is proud to be part of this revolutionary leap.”
Revolutionizing product certification
Traditionally, product certification demanded exhaustive physical tests, often subjecting a single product to a battery of assessments. Simulation based on the digital twin is the answer to the special challenge and cost factor of test units and certified laboratories when high power electronics components are involved. Siemens and UL Solutions, however, introduced a paradigm shift. A product may not need to undergo every test physically; instead, the process can integrate the power of Siemens’ digital twin technology. UL Solutions spearheads this transformative approach, navigating the certification process with unmatched expertise.
By harnessing the power of digital simulations, Siemens is ushering in an era in which traditional testing boundaries are being transcended and product insights can be gained with unprecedented speed and accuracy. The future of certification will be characterized by reduced costs, accelerated time-to-market, and seamless integration of digital modeling tools. Comprehensive digital twins are becoming the cornerstone for not just helping to meet compliance requirements, but also driving innovation at high speed without compromising safety, performance or quality.
In Siemens’ pioneering venture into the industrial metaverse, the demarcation between physical and digital spaces is becoming increasingly indistinct. The resulting combination is fostering a dynamic environment conducive to innovation. The first certification of an industrial product – the “SINAMICS G220” to be precise, a sophisticated system that enables precise control and efficient operation of electrical drives in various applications – leveraging Siemens’ comprehensive digital twin is a compelling demonstration of the industrial metaverse’s potential to usher in unprecedented possibilities for product development and other engineering tasks.
Related Story
Siemens Innovates SINAMICS S210 Servo Drive System with New Hardware and Software for An Even Larger Range of Applications
Siemens is innovating the well-established Sinamics S210 servo drive system with a new hardware architecture and new V6 software generation that expand the system’s range of applications. The servo drive system is especially suitable for applications with high dynamics in the power range between 50 W and 7 kW: for example, machines for packaging, pick & place applications, and digital printing.