Nidec’s New Fusion Pump Motor System Offers OEMs All-in-One Drive Solution
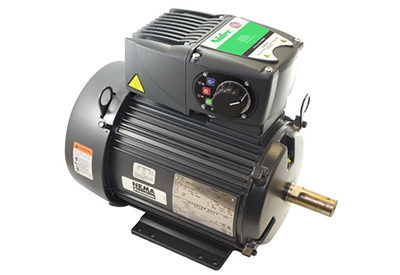
March 16, 2021
Nidec Motor Corporation has introduced the ID300 Fusion Integrated Motor Drive that features U.S. MOTORS brand 3-10HP UL-certified induction motors and customizable variable speed drives.
With this compact all-in-one product, original equipment manufacturers (OEMs) do not need to buy stand-alone products such as motors, drives, conduits and cords, and integrate them for a customer application. Nidec delivers directly from the factory a compact integrated motor and drive that is perfectly paired for use. With the ID300 Fusion, OEMs have quality products that they know and trust, along with reduced worries associated with installation and frequency issues.
Designed and engineered with Nidec’s most advanced technologies for power and control, the ID300 Fusion incorporates all of the functions of a variable frequency drive (VFD) into the motor for better system performance and efficiency. The ID300 Fusion, backed by Nidec’s substantial resources, offers new levels of technology, security and convenience for OEMs and end users.
A global leader in the design and manufacture of electric motors and VFDs, Nidec has worked closely with OEMs to utilize VFDs to meet Federal energy requirements and satisfy customer needs. With Nidec’s investment and support, the electronics manufacturing technology has made tremendous advancements that have enabled the highly reliable fusion of the motor and drive. The evolution of the system architecture has paved the way for exciting innovations such as the ID300 Fusion.
The integrated ID300 Fusion provides superior control and monitoring capabilities that help with real-time pump management and intelligence analytics. The product features a powerful suite of development tools, backed by experienced application engineers in the Nidec Motor Technical Center.
With pumping applications in mind, the ID300 Fusion allows OEMs to embed the pump curve information into the drive so that the pump runs at its best efficiency point without an external sensor. That saves the cost of the sensor, the labor to install it, and also minimizes the risk of error if the drive is incorrectly programmed for the sensor. An onboard programmable logic controller (PLC) can regulate the pressure (constant pressure/variable flow). When programmed with the pump curve, the ID300 PLC can perform sensor-less constant pressure control, eliminating sensor cost and simplifying its installation and commissioning. One ID300 Fusion can control up to three additional constant speed backup pumps.
In addition to the operational benefits of the ID300 Fusion, its small modular design takes up less space than separate products. Its compactness also makes it easier and quicker to install into other existing control systems. Built and tested to withstand harsh environments, the product offers a 24-month warranty from the date of installation or 30 months from the manufacturing date, whichever comes first.