The New Security Norm in OT
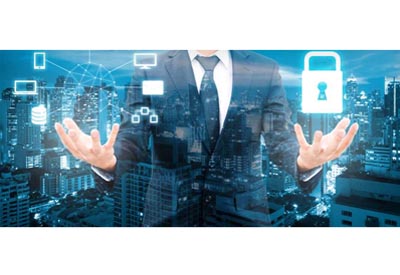
September 25, 2018
By Steve Ludwig, Rockwell Automation
The growing use of widely available technologies in industrial control systems (ICS) and the growth of more connected, information-enabled enterprises inherently increases security risks, and with it the responsibilities of control system providers and users alike.
Historically, industrial control systems used proprietary technologies, and were generally segregated from the information systems at most companies. The systems were largely incompatible and the commercial technologies that were used in office spaces simply didn’t fit the requirements of control systems.
As commercial technologies advanced in recent decades, they were adapted for use in control systems, improving costs, compatibility, and ease of use. With these improvements, connectivity between systems became simpler and increasingly demanded by users.
Bringing together enterprise-level IT and plant-level operations technology into a common infrastructure creates more opportunities to improve operations, but without proper cybersecurity hygiene may also provide increased opportunities for cyber-attacks against ICS equipment.
Such attacks, if successful, can have severe impact on worker, environmental and product safety, intellectual property, reputation and productivity.
These challenges are changing the way ICS providers and users work together, bringing increased responsibilities to each.
ICS providers have an increased responsibility to understand, detect, and remediate security vulnerabilities and to disclose them through patch and version management to users. While much of this is “old hat” to information technology (IT) professionals — receiving regular announcements of vulnerabilities and patches to remediate them — it’s new to ICS engineers.
A comprehensive cybersecurity strategy includes cybersecurity hygiene — asset inventory to understand what you have, controlling physical and digital access, segmentation, system configuration and other actions. It also includes adoption of NIST CSF to identify, protect, detect, respond and recover from cyber-attacks.
It also requires that ICS providers, like Rockwell Automation, constantly test products and review applications to identify and remediate vulnerabilities in products. Disclosing remediated vulnerabilities through patch and version management helps protect ICS users from cyber-attacks.
It is part of an ethical, comprehensive cybersecurity strategy to help verify our customers’ security and safety. While not actually new, the increased focus on security in recent years, and the more frequent disclosures may seem surprising to some.
To others that have worked closely with IT, it will seem natural and expected. To all, it should be welcomed as a clear focus on supporting the safety and security of industrial control systems.
For more information on security, please check out the following resources:
- Product Security Vulnerabilities FAQ (PDF)
- Converged Plantwide Ethernet (CPwE) Design and Implementation Guide (PDF)
If Assistance is Needed
Rockwell Automation and our partners provide scalable, tiered level assistance services based on the stage of the user in the cybersecurity risk management implementation. Use the following list of resources when your customer is requiring assistance:
Rockwell Automation Remote Support Services
Technical assistance in finding product downloads applying them to products.
https://rockwellautomation.custhelp.com/ to find the local support options.
Product Security Office
Non-critical support and general information about the security vulnerabilities and mitigations offered. No customer-specific advice can be offered; secure@ra.rockwell.com
Network & Security Services
Consultants for strategic and tactical industrial security services, such as security assessments and program development, asset inventory services, patch management, threat detection services; Network & Security Services Home
For more information https://www.rockwellautomation.com/en_NA/overview.page?