Robust in the Spray Zone
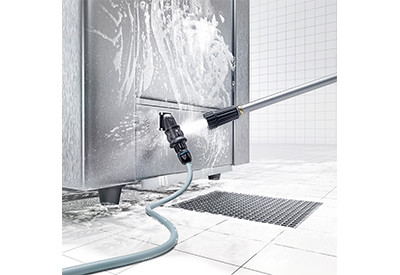
March 25, 2020
To date, food producers have so far often been sceptical about the use of connectors in sensitive areas. Given their profiles and footprints, they fear that interfaces will interrupt the smooth, easily washable surfaces needed for cleaning in areas close to the product. With the Han F+B, HARTING has now developed a special connector that will hold up to intensive cleaning while at the same time opening up new options for the design, assembly and maintenance of production facilities.
Installations in the food industry must be designed in such a manner that no substances hazardous to health can get into the food. Consequently, processing and packaging machines must be designed in such a way that they facilitate cleaning and prevent the formation of dirt pockets – and what sounds so plain and simple causes headaches for many production managers in the industry.
The product zone, i.e. the zone with direct food contact, makes the most stringent demands on machines and components. This area is often kept small in order to reduce the required cleaning input. Smooth surfaces are ideal, as they prevent bacteria from colonizing. Due to the fact that electromechanical interfaces interrupt the smooth surfaces, they are positioned outside this zone if possible.
Electrical connections in the spray zone
But even in the spray zone, however, food producers often consider the use of industrial connectors instead of hard wiring as risky: this is because cleaning chemicals are sometimes used here that put a lot of stress on materials. In addition, high-pressure cleaners regularly impact on the equipment with hot water and high pressure. This can cause seals and cable glands on connectors to lose their protective effect on the inside of the housing.
At Packaging Automation (PA), a manufacturer of tray sealers in Knutsford, Great Britain, the use of connectors also used to be associated with risks: There were cases in which cable glands and sealing rings lost their protective function after the use of highly effective cleaning chemicals and high-pressure cleaners. In the meantime, however, PA has been relying on the special Han F+B connector from Harting for some years now. “The connector has helped us overcome a number of design challenges on our own machines,” as Steve Woodhead, Development Engineer at PA relates. The connectors thereby enabled standardization at the lower part of the machine. “If a customer wants an option changed, we can now easily change inserts without having to redesign the entire metal construction of the tray sealer,” Woodhead adds. Thanks to the use of the connectors it has become easier to quickly connect components such as suction systems.
Resistant to aggressive chemicals
The special connector from HARTING transmits power and signals in the splash zone – in other words in a particularly hygienically sensitive environment where plant components can come into contact with food. Although such food is not returned to the product flow, residues may remain on the machine components. This zone requires connectors that can withstand cleaning with high pressure and aggressive chemicals and consequently also protect the electrical connection from water under high pressure. Subsequent to cleaning, no residues must remain which could lead to the formation of germs.
It is readily apparent that the Han F+B has been designed for the spray zone: the housing features an easy-to-clean design with large radii and smooth surfaces, and was designed according to the guidelines of the European Hygienic Engineering & Design Group (EHEDG). Special housing and seals protect the electrical connections according to the IP69K protection class against high pressure and steam jet cleaning. In addition, the gaps that occur in connectors due to their function are covered. The housing material is FDA 21-approved, while Ecolab certification confirms resistance to aggressive cleaning chemicals.
In addition to the Han F+B inserts with nine contacts, over twenty different inserts are available for the Han 3 A construction size: The range extends from RJ45 interfaces and signal inserts with a maximum of 21 poles to power contacts for currents up to 40 amps. Thanks to this highly diverse portfolio, users can flexibly install electrical interfaces even in compact and tight installation spaces. There is no need to open cable glands on the control cabinet to decouple field devices. The time and effort consuming disconnection and reinstallation of hard wiring can be dispensed with. Thanks to the connectors, plant installations are quicker, while tool changeovers and service calls are shorter.
Greater system design flexibility thanks to connectors
The demands on connectors in the product-free zone are not quite as high, since direct contact between food and system components is not intended here. Nevertheless, the components should be easy to wash and disinfect. This is where the advantages of the Han B industrial standard connectors enter the picture. They feature the IP65 protection class as a minimum and are therefore suitable for many applications.
Stainless steel housings represent another option: If the product-free zone is cleaned together with other areas, the components can be exposed to considerable chemical stress. In such cases, stainless steel is a suitable housing material for connectors because it is particularly resistant to corrosion and features smooth surfaces, enabling the thorough and residue cleaning of surfaces.
Consequently, the stainless steel housings of the Han-INOX series are therefore particularly resistant to chemical cleaning in the food industry. The interior with the contacts is safely protected against splash water. Opting for the housing of the larger 10 B size, users can also benefit from inserts of the Han-Modular series. The series consists of a large number of inserts in standard sizes that cover the various industry lifelines, ranging from the Han Gigabit module for fast data transmission to power modules (with e.g. 16 amps), high-current modules (100/200 amps) and pneumatic contacts for compressed air. The right system can be assembled for (almost) any scenario.
Alternatively, compact Han 3A stainless steel housings can also be used as the feature IP67 protection class and are decidedly compact. As a result, they are ideal for use as motor connectors, for example.
High performance plastic as an alternative
Plastic offers an alternative to stainless steel outside the production area cleaned under high pressure. In addition to the special Han® F+B connector for the splash zone, HARTING’s product range also includes the Han-Eco®, which is suitable for the product-free zone. The non-corrosive properties of the glass fibre reinforced high-performance plastic represent the main advantage here. Han-Eco® features housings that are characterised by high mechanical robustness and IP65 protection, while the weight of the plastic material is low. Here too, the combination with contact inserts from the Han-Modular® series is expedient, whereby Han-Eco has the advantage of providing room for one module more in each size than in the standard metal housing, thereby saving space, weight and costs.
Docking frames are expedient in setup-intensive applications with regular tool changes, for example format changes on thermoforming machines. The frames serve as a receptacle for Han-Modular®. Various modules for transmitting power, data, signals or compressed air can be positioned next to each other. In view of over 100 different modules, the modular connector range offers virtually infinite combination options and superb flexibility. The docking frame serves to connect or disconnect the interfaces together with the tools or machine elements. These docking systems can be structured modularly and adapted to the respective application, thereby creating expedient and efficient solutions for many set-up processes.
Hygienic design
Information on deploying connectors in the food industry
HARTING has published an informative white paper on the subject of connectors in the food industry. The document provides users with an overview of the demands made on connectors as they result from the zoning in food production (e.g. EN 1672-2). In addition, it provides information on the appropriate design of interfaces for machines as well as the materials to be used in the food industry as well as information on the resistance of connector components to cleaning agents.
Background:
The three zones of food production
Processing in the food industry takes place in three different zones: the product zone, the splash zone and the product-free zone. Each zone places different demands on the components employed. All plant parts and components with direct food contact are assigned to the product zone, and must be washable, desinfectable, corrosion-resistant, non-toxic, non-absorbent, smooth, continuous or sealed. As connectors do not usually come into direct contact with food they are rarely encountered in this area.
In the spray zone, food can also come into contact with components, but does not return to the product flow. Since this area also needs to be cleaned regularly, the criteria applicable to the product zone should be consulted for orientation in order to ensure a high level of hygiene at this point as well. In the product-free zone, there is no direct contact between food and plant components. These components must be resistant to corrosion as well as being easy to wash and disinfect.
For more information, visit www.harting.com/fb.