Printing With Precision – Improving Existing High-Speed Equipment
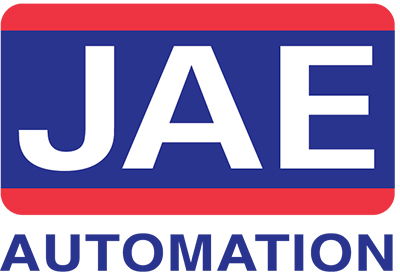
September 27, 2019
The Scenario
A high-speed printing company had partially completed an upgrade to their equipment. The printing machine used two alternating print heads to produce units at a rate of more than 11/s. Due to the nature of the product, speed, accuracy, and repeatability were extremely important. The process needed to be consistent as any defect would impact production further down the line.
To ensure there were no errors, the units would pass through a vision system designed to detect defects and other irregularities. A mechanical reject system would then remove any defected units from the line. The entire process needed to operate in less than a second with extreme precision.
The partially completed equipment was expected to be installed in the facility, but performance issues meant that improvements needed to be made. The printing company needed to address these issues and retrofit the machine in time for a major upcoming contract.
The Requirements
The printing company had a number of requirements which were communicated with JAE Automation during the initial consultations, including:
- Improving the speed, performance, and reliability of the partially completed equipment
- Implementing and installing the equipment in time for scheduled contracts
- Achieving near 100 percent accuracy and defect detection rates
- Developing a high-speed reject system that would consistently meet performance requirements
The Engagement
JAE Automation was initially brought in to assist with the setup and implementation of the partially completed printing equipment. The company selected JAE Automation due to the fact that they were a local company with extensive experience in high-speed and mechanically complex automation projects.
Early on in the process, JAE Automation identified and communicated a number of other areas that could be improved upon to enhance the performance of the machine and achieve the speed and accuracy requirements of the company. For example, it was determined that the reject system previously in place was not adequate and would be unable to consistently reject defective units.
The customer agreed to the recommendations and budgets provided by JAE Automation, and contracted them to work on all areas of the machine.
The Solution
JAE Automation designed and delivered a solution that improved and retrofitted the machine. This included improving the control systems, motion controls, safety systems, and packaging systems.
One of the major components of the solution was the reject system designed by JAE Automation, which used high-speed equipment connected to the vision system to immediately remove any defective units from the production line.
The Results
The delivered solution met the accuracy, repeatability, and speed requirements of the customer. With the additional recommendations provided by JAE Automation, the machine achieved better performance and the entire process was greatly improved. Specifically, the reject system achieved rejection rates that were significantly better than the previous system, reducing error rates and ensuring only correctly printed units reached the next stage of the production process.
The equipment was installed and running when the customer needed it for their upcoming projects and contracts, and they were able to continue their business without delays. JAE Automation demonstrated an ability to go above and beyond the initial requirements by successfully retrofitting the existing equipment and making things better.