Power Plants Forge Ahead: Speedy Delivery of High Quality, Open Die Forgings, Seamless and Contoured Rolled Rings, and Complex Forged Parts
January 24, 2024
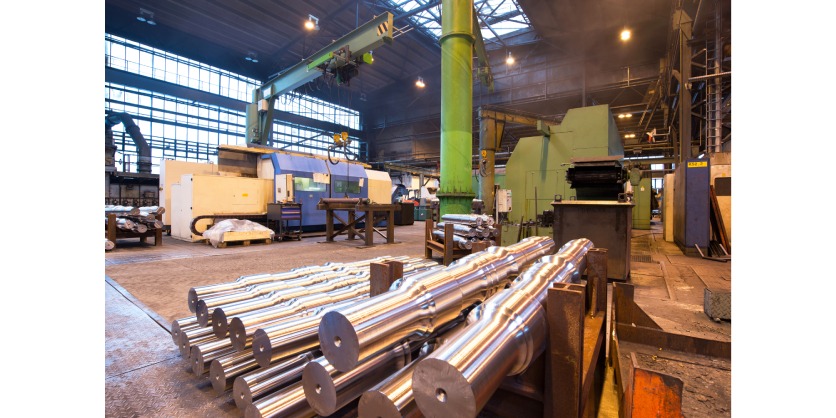
By Del Williams
Specialty forgers can manufacture custom, high-quality, seamless rolled rings in a variety of materials and finishes in as little as eight weeks
Open die forgings and seamless rolled rings are essential components in power plant engineering, contributing to the overall reliability and efficiency of turbines, generator systems, and transmission and distribution equipment.
Forgings for component parts and seamless rolled rings have a greater lifespan than other products due to their strength and durability, and are less prone to cracking or warping, making the option ideal for critical components requiring high tensile strength. Depending on the metal and alloy, the rings are also resistant to thermal and chemical damage, which further extends longevity while reducing the need for maintenance, repair, and replacement.
For the power generation industry, obtaining large seamless rolled rings and turbine parts in a timely manner remains a significant challenge, however. Currently, it may take many months to receive the forged components after placing an order. This delay can have a severe impact on the production and maintenance schedules of firms that depend on replacement parts.
Rings are typically provided with a rough surface finish, which necessitates the use of CNC machining to achieve the required level of smoothness. This poses a challenge for machine shops with a high workload, as allocating machine time for finishing inevitably leads to a decrease in production speed and an increase in costs, ultimately impacting the end-use cost or profitability.
Fortunately, power generation product manufacturers can rely on industry-leading forging specialists capable of producing a wide array of shapes and sizes of custom forged parts, seamless rolled rings, and contoured seamless rolled rings with the required surface finish in under two months. One example, All Metals & Forge Group, an ISO 9001:2015 and AS9100D manufacturer of custom and standard open die forged parts and seamless rolled rings can cost-effectively deliver these components with the required finish within 8-10 weeks.
The range of forged products includes rings, discs, hubs, blocks, shafts (including step shafts or with flanges), sleeves, gear blanks, cylinders, flats, hexes, rounds, plates, and custom shapes. Carbon steel, alloy steel, stainless steel, nickel, titanium, and aluminum are among the materials used for forging. These forgings meet rigorous industry specifications such as ASTM, AMS, AISI, ASME, Boeing, SAE, GE, DIN, ASME B 16.5, ASME B16.47, and API 6A.
When speed and quality are essential, the power industry can reap the advantages of an accelerated process for obtaining flawless rolled rings.
The Benefits of Open Die Forging
One of the chief advantages of open die forging is the customization it offers in the seamless rolled ring manufacturing process.
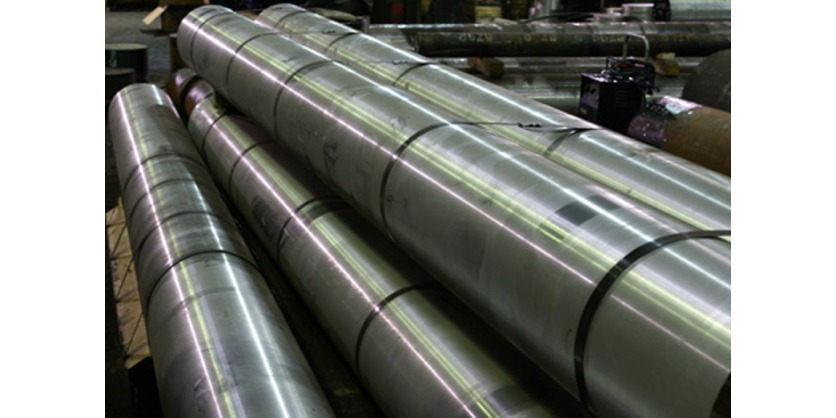
According to Lewis Weiss, President of All Metals & Forge Group, open die forging is ideal for providing large, custom parts. “We can produce seamless rolled rings or contoured rolled rings up to 200 inches in outside diameter, and custom forgings up to 40 feet long or 80,000 lbs.,” says Weiss. All Metals & Forge Group has been manufacturing and selling open die forgings and seamless rolled rings for more than 50 years
While open die forging is typically associated with larger, simpler-shaped parts like bars or blanks, the process enables the creation of “custom-designed” metal components.
According to Weiss, open-die forging facilitates the production of seamless rolled rings to exact specifications with optimized mechanical properties and structural integrity. He notes that the rings can be produced in a variety of alloys, sizes, and shapes specific to the requirements.
The forging of the rings is also cost-effective since the process reduces material waste and manufacturing costs. Since the rings are constructed from a single metal piece using a specialized ring rolling machine, there is no need for welding or assembly, saving time and labor. The seamless rolled rings are also more structurally sound because they create a circular grain flow in the material, following the shape of the ring, which increases strength and integrity, creating a refined grain structure. This can enhance the material’s fatigue resistance and overall performance, resulting in a stronger, more durable final product compared to other methods of ring making, such as cutting from plate.
Near Net Shape Parts with Finer Surface Finish
Typically, when seamless rolled rings are forged, they are often left in an unprocessed state with a rough surface measured at approximately 500 RMS. As a result, significant CNC machining time is required to achieve a smoother surface for the finished machined part. This poses a challenge for machine shops as the allocation of machine time for finishing these rough parts directly affects production efficiency and delivery time to the client.
To optimize efficiency and reduce costs, All Metals & Forge Group frequently provides near-net-shaped forged parts with more refined surface finishes.
“Typically, we provide a 250 RMS surface finish. We can even provide 125 RMS. We can also drill holes and do contour forgings as needed,” says Weiss. “Some forge shops only offer a raw unmachined part. We produce a rough machine part, saving machine shop time and equipment wear and tear since we have already taken off the first rough cuts off the ring or forged parts,” he adds.
Lewis Weiss, President of All Metals & Forge Group
In addition, the company conducts ultrasonic testing at zero expense to the customer to guarantee the absence of internal cracks, pits, or voids. This instills the utmost confidence in the quality of the parts, according to Tim Grady, Management Consultant for All Metals & Forge Group.
“In many cases, All Metals & Forge Group can offer ultrasonically tested parts that are more affordable than raw forged rings,” says Grady.
Tim Grady, Management Consultant for All Metals & Forge Group
Streamlining Delivery
In today’s market, the procurement of forged seamless rolled rings usually takes a considerable amount of time, from 20 weeks to as much as a year, as there are long lead times in receiving the necessary steel from mills.
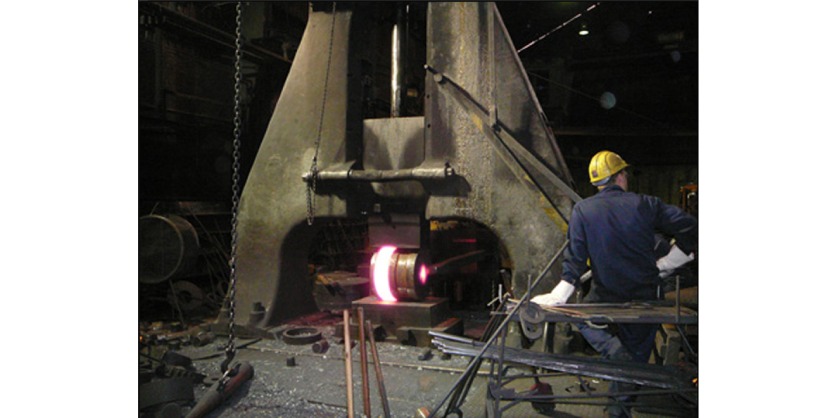
“When replacement parts are required, a delay of a year or more is not acceptable,” says Grady. “Even 20+ weeks is a serious issue.”
To expedite the process for customers, All Metals & Forge Group has established strategic partnerships within the industry, enabling the company to deliver many custom forgings in a timeframe of eight to 10 weeks. Furthermore, to minimize any potential production downtime for machine shops, the company strives to provide accurate quotes within 48 hours.
Positioning for the Future
The need to acquire seamless rolled rings will only increase in industries like power generation that require high-quality custom-forged components that can safely withstand extreme forces with minimal repair or replacement. In these cases, working with an expert forger who can expedite the process will convey a significant advantage.’
More Information
For more information, contact All Metals & Forge, LLC at 75 Lane Road, NJ 07004; (973) 276-5000; Canada 416-363-2244, toll-free (800) 600-9290; fax (973) 276-5050 or visit http://www.steelforge.com
Related Story
Massive Expansion of Renewable Power Opens Door to Achieving Global Tripling Goal Set at COP28
The world’s capacity to generate renewable electricity is expanding faster than at any time in the last three decades, giving it a real chance of achieving the goal of tripling global capacity by 2030 that governments set at the COP28 climate change conference last month, the IEA says in a new report.