Multi-Tasking Facts and Fiction
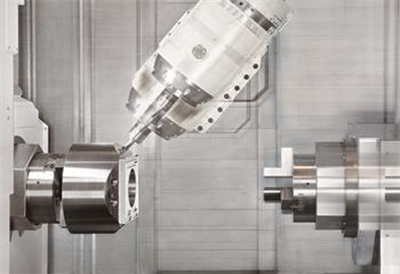
January 24, 2019
Despite the fact that Multi-Tasking technology has become increasingly common in shops across the country and around the world, many manufacturers still believe such machines are costly and a challenge to integrate into existing processes and automation. Where these myths arose remains a mystery, but the facts are easy to find, especially when discussing Mazak Multi-Tasking. Here are a few myths we can quickly debunk:
MYTH: Multi-Tasking is too new to trust
FACT: Multi-Tasking is tried and tested technology
The first Mazak Multi-Tasking machine, the SLANT TURN 40N ATC Mill Center, came out in 1982. Since then, Mazak has invested heavily in pushing this technology forward, both in terms of machine tool parameters and the infrastructure needed to help customers succeed. As a result, Mazak has a comprehensive selection of Multi-Tasking machining centers that have been put to profitable use in virtually every industry – along with an equally comprehensive training program that comes free with every machine sold to help manufacturers get their operators up to speed.
MYTH: Multi-Tasking machines are too expensive for my shop
FACT: Multi-Tasking machines are a great value in terms of costs
For many manufacturers, comparing a machine tool’s sticker price with the business’ bank account balance is the beginning and end of their cost-benefit analyses. And indeed, in terms of price, Multi-Tasking technology is more expensive than traditional lathes or mills. However, instead of looking at price, manufacturers should look at costs. This requires a more involved analysis – one should consider maintenance costs, available services and other factors that impact the purchasing and operating costs of the machine. When you invest in manufacturing technology that will be used for decades, it pays to think long-term.
MYTH: Changing my processes won’t speed things up enough
FACT: Fewer setups across the production cycle leads to higher-value parts
For some shops, particularly those in the medical and aerospace industries that produce parts with highly regulated supply chains and quality requirements, changing processes in search of greater profitability is difficult or impossible. But for all other shops, updating processes can be a great way to improve productivity, and Multi-Tasking is an equally great way to achieve that goal. Eliminating extraneous setup time, for example, does more than just shorten part processing time, it prevents scrapping parts due to human error and makes repeatability far easier to achieve.
MYTH: My parts are too simple to require Multi-Tasking
FACT: The majority of parts have secondary operations
For some manufacturers, such as those in the automotive sector, simple, mass-produced parts are the norm. But even these parts often have secondary operations and benchwork to consider, and for most manufacturers, simple parts are a thing of the past. With Multi-Tasking, secondary operations can easily be completed as part of the first setup for a far more secure machining strategy.
MYTH: Multi-Tasking applications are too difficult to program without special training
FACT: MAZATROL Smooth CNCs make Multi-Tasking applications easy to create for any operator
As manufacturers across numerous industries have discovered, skilled machine operators are getting increasingly scarce as experienced operators and engineers age out of the workforce, especially with an already tight job market. The solution? MAZATROL SmoothG and SmoothX controls, which make it easy for even new operators to program complex parts right at the machine thanks to MAZATROL, Mazak’s conversational programming language. Answer the computer’s questions with your part’s dimensions and characteristics to generate sophisticated Multi-Tasking cutting programs – it’s that simple.
MYTH: Multi-Tasking is tough to automate
FACT: Mazak Multi-Tasking machines are built for automation
In many ways, Multi-Tasking technology is automation built directly into the machine – rather than using a robot to move a part from a lathe to a mill, the Multi-Tasking machine simply performs both operations in one setup, perhaps passing the part from one spindle to the next to continue working. However, Mazak Multi-Tasking takes this much further, with machines designed for automation solutions that range from the Multi-Pallet Pool (MPP) System or Auto Work Changer to full PALLETECH or MAZATEC SMS installations, all to help shops achieve unmanned lights-out operations.
Interested in learning more about Multi-Tasking and demystifying the process? Visit our 5 Levels of Multi-Taskingpage and discover how much these technologies can impact your machining operations – and your bottom line.