Maximizing Motor Efficiency: Navigating the Impact of VFDs on Motors
March 15, 2024
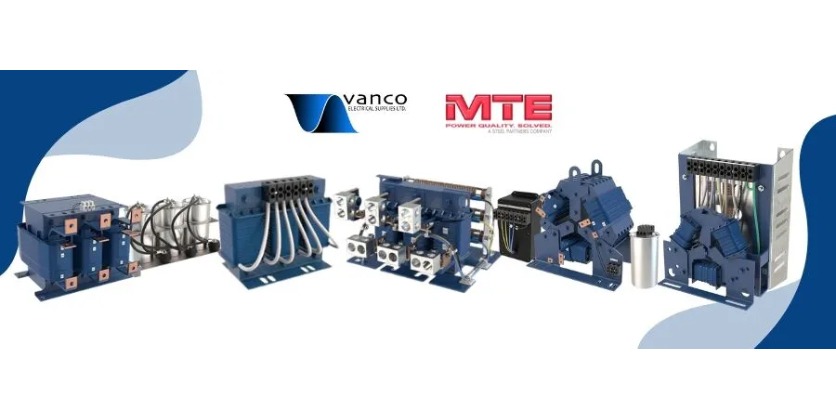
Introduction
Running a motor directly from the power source produces uniform, sinusoidal waveforms but wastes energy due to continuous speed operation regardless of the load requirements. To enhance efficiency, variable frequency drives (VFDs) control motor speed, reduce energy consumption, and minimize equipment wear. However, VFDs use pulse-width modulation (PWM) to supply electrical pulses instead of a true voltage waveform, generating harmful harmonics that can damage motors, cables, and bearings.
Understanding Differential Mode and Common Mode
When using a VFD, the output is no longer a sinusoidal wave where phases sum zero.
PWM signals produced by the VFD never sum zero during operation, which leads to the generation of common or differential mode voltages. The common mode voltage present induces common mode current, which finds a path to ground via cable shields, jackets and ground conductors, as well as motor frames via motor shaft and bearings. While the differential mode current path is found in the form of oppositional current in the supply conductors and windings.
The Destructive Effects
Damaged equipment due to differential mode voltage spikes, common mode noise, and high peak voltages due to the reflected wave phenomenon, jeopardize productivity and decrease profitability. Moreover, these effects are often difficult to diagnose and extremely problematic for everyday operations. Some common “symptoms” below.
- Damage to motor bearings.
- Erratic behavior of VFDs and PLCs
- Cable damage
- Unexpected ground fault trips
- Premature motor insulation failure
What Level of Motor Protection Do You Need?
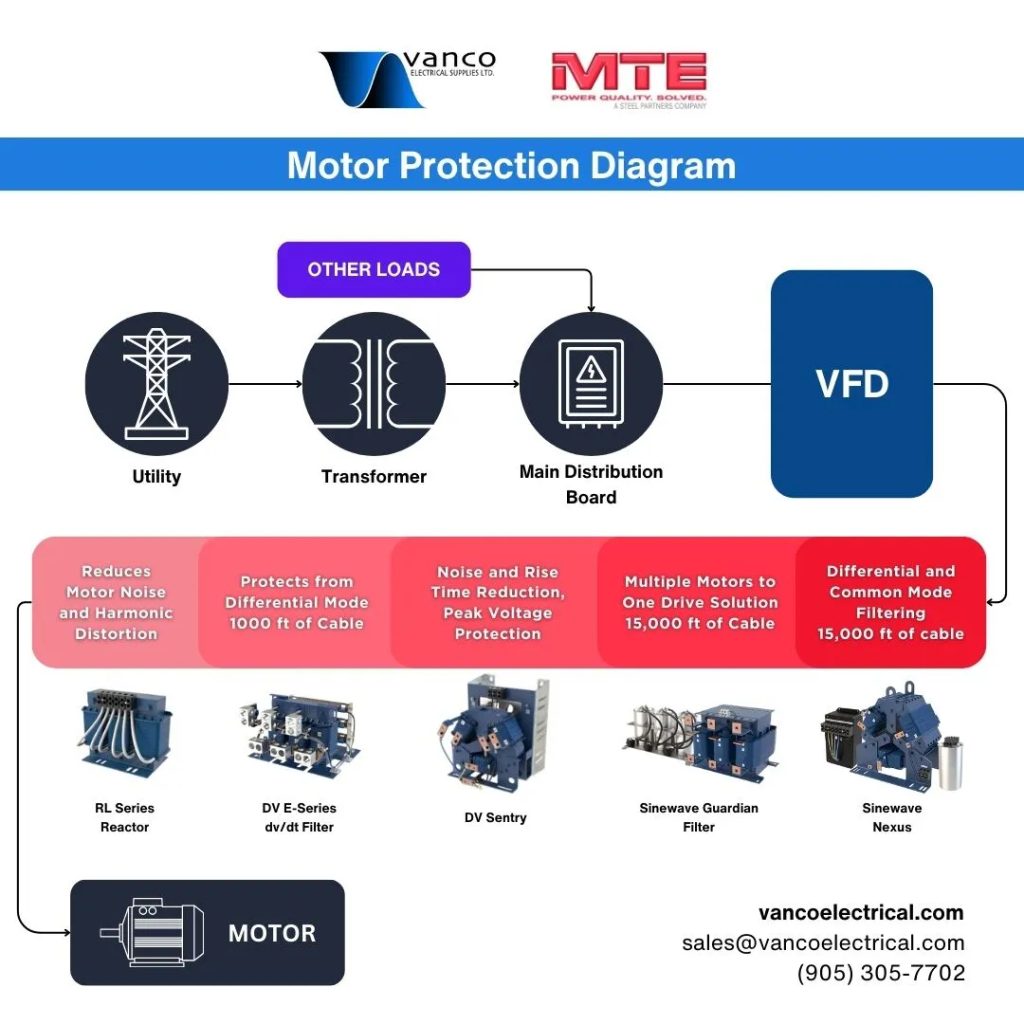
1. RL Series Load Reactor
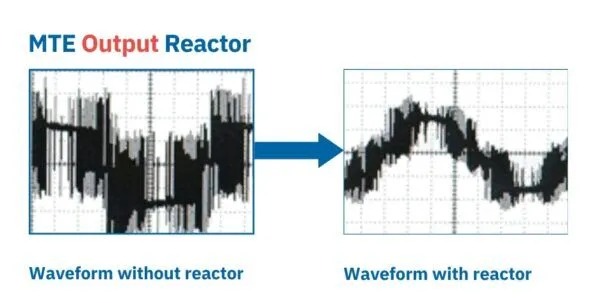
- Reduces audible motor noise
- Minimizes long lead effects
- Reduces harmonic distortion
2. DV E-Series DV/dt Filter
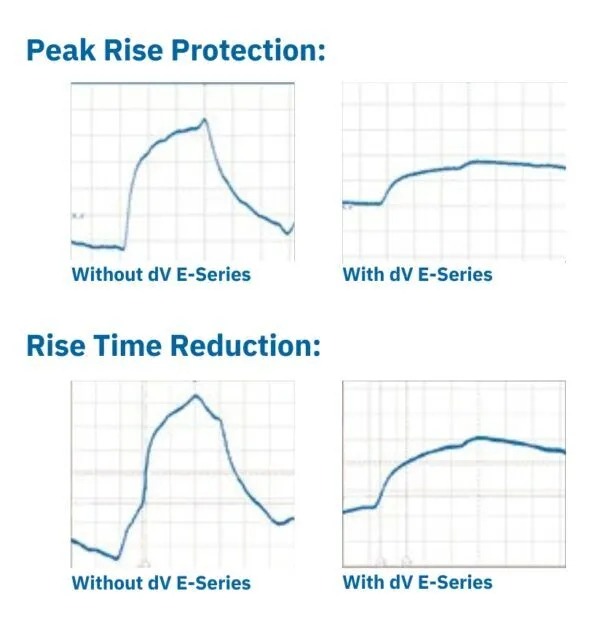
- Peak voltage protection, rise time reduction, economical solution for system reliability.
- Available in many configurations, suitable for a 1000 ft cable length.
3. DV Sentry Filter
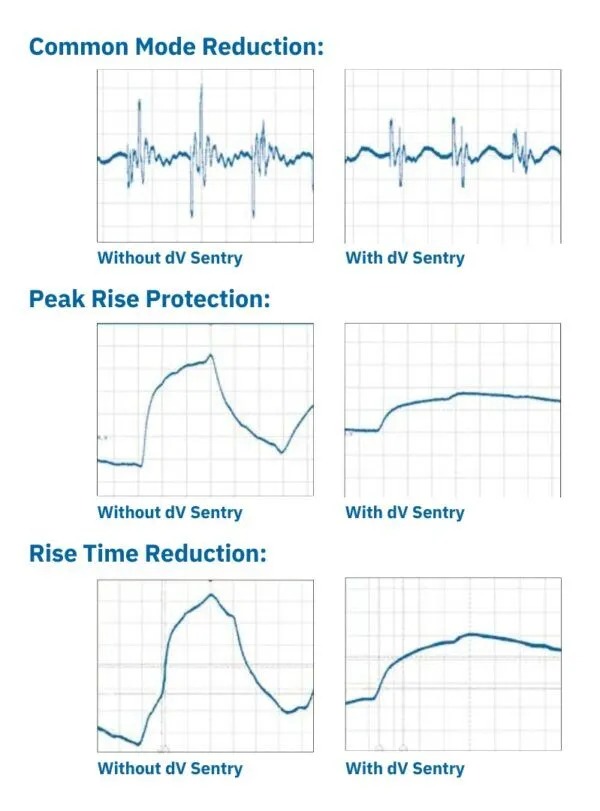
- Common Mode Noise Reduction
- Peak Voltage Protection
- Rise Time Reduction
4. Sinewave Guardian Filter
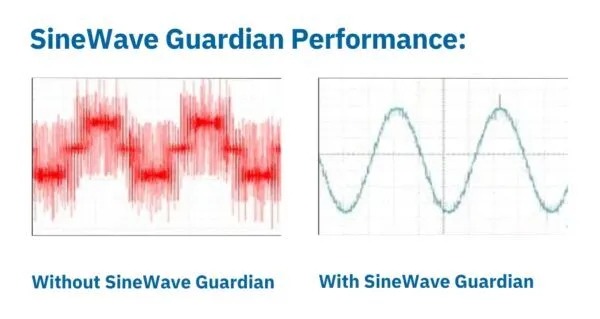
- Maximum 5% THVD.
- Differential mode filtering, suitable for multiple motors to one drive solution.
- Ideal for medium voltage applications with a step-up transformer, supports a 15,000 ft cable length.
5. Sinewave Nexus and Micronexus
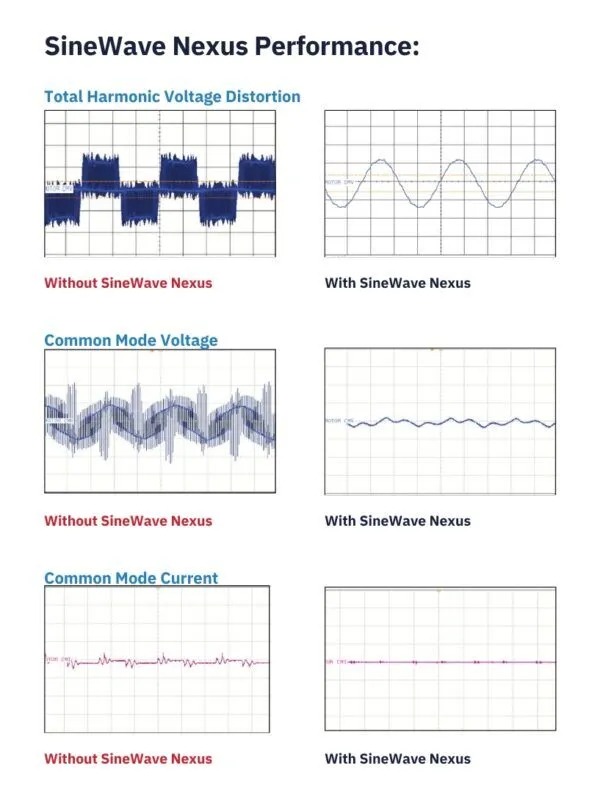
- Maximum 5% THVD, -20dB common mode attenuation, >90% PWM common mode RMS voltage reduction.
- Differential mode and common mode filtering, optimized microdrive solution.
- Perfect for demanding applications, supports a 15,000 ft cable length.
- VFD cable not required
- 5-year bearing warranty
Conclusion
Choosing the right level of motor protection is crucial for reliable and efficient operation. MTE offers a family of application-engineered products designed for the performance you need. For application support, contact Vanco Electrical Supplies Ltd.
More Information
Related Video
MTE Motor Protection & VFD Break-Down with Dan Schmidt
VFD’s are great, but what about the Power Quality issues they present? Check out MTE’s product demo video to understand what the problems are and how to correct them! Product Line Manager Dan Schmidt gives an overview of the dangers of VFD use and how MTE products can protect against them.