EtherNet/IP Network Specification Complete for Ethernet-APL Physical Layer for Process Automation
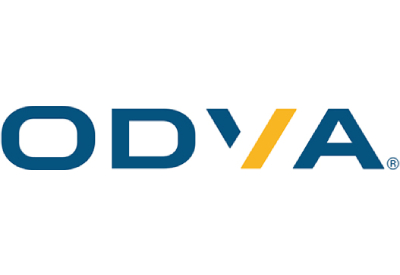
December 3, 2021
ODVA announced recently that The EtherNet/IP™ Specification has been enhanced to enable EtherNet/IP networks to support the Ethernet-APL physical layer for process automation. Licensed Vendors for the EtherNet/IP technology can immediately start developing EtherNet/IP components for Ethernet-APL, including controllers, power switches, field switches, and instrumentation.
Ethernet-APL is the new intrinsically safe, two-wire extension of 10BASE-T1L (IEEE 802.3cg-2019) Single Pair Ethernet that meets the requirements of the process industries. The advantages of Ethernet-APL include communication speeds of up to 10 Mbit/s, hazardous area protection, power to field instrumentation, and long cable runs of up to 1,000 meters (IEC 61158-2). Ethernet-APL devices adhere to IEC TS 60079-47 (2-Wire Intrinsically Safe Ethernet) in order to ensure “intrinsically safe” ignition protection. The Ethernet-APL physical layer overcomes the challenges of using fast, high bandwidth Ethernet at the field level in process plants with hazardous locations and a large geographic footprint.
“Today’s announcement is a culmination of many years of cooperative work to bring Ethernet-APL to industry. ODVA is pleased to continue to expand the capabilities of EtherNet/IP for process automation with the inclusion of Ethernet-APL in the EtherNet/IP Specification,” said Dr. Al Beydoun, President and Executive Director of ODVA. “With the aid of Ethernet-APL, EtherNet/IP will be able to expand precise, efficient Ethernet-based control and commissioning across field instrumentation. The full use of EtherNet/IP in process installations will enable concurrent seamless connectivity from the field devices to the controllers, to Industrial IoT applications, as well as the edge and cloud for prognostic analysis.”
The addition of support for the Ethernet-APL physical layer is another key step in the adaptation of EtherNet/IP to meet the full requirements of the process industries. Completed enhancements for EtherNet/IP which benefit applications in the process industries include NAMUR NE 107 diagnostics, HART integration, IO-Link integration, and support for the next generation of digitized device description files, including FDT and FDI. Inclusion of the Ethernet-APL physical layer will allow for end users to take full advantage of the benefits of EtherNet/IP in process plants, including commercially-based industrial control hardware, an object-oriented foundation, and standard internet protocol compatibility including TCP/IP, HTTP, FTP, SNMP, and DHCP. With support for functional safety with CIP Safety™, device defense with CIP Security™, time synchronization with CIP Sync™, and fault tolerant redundancy with parallel redundancy protocol (PRP) and Device Level Ring (DLR), process automation installations with EtherNet/IP can benefit from network and device health monitoring, built in security and safety, and remote device configuration.
The first Ethernet-APL controllers, power switches, field switches, and instrumentation that support EtherNet/IP are expected to be available in 2022 once the conformance testing certification process is complete. Visit odva.org to obtain the latest version of The EtherNet/IP Specification including EtherNet/IP for Ethernet-APL.