Best for healthy babies – Baby food production reliably automated with Siemens technology
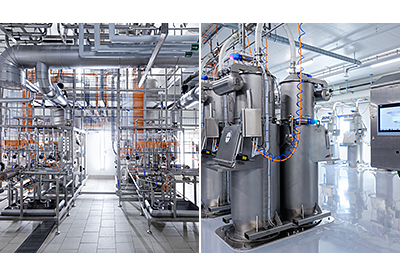
May 30, 2019
Hochdorf Swiss Nutrition AG specializes in the manufacture of foods made from ingredients such as milk, oilseed and cereals. In its new 30-meter high production facility, Tower 9, the Swiss company processes around 75 million liters of milk to produce some 30,000 tons of baby food every year. Ensuring that the resulting milk powder has just right final consistency without being either too powdery or too liquid, precise process control is vital. Here, Hochdorf has opted to rely on modern technology from Siemens, which enables reliable 24-hour monitoring of the plant and seamless traceability of the entire production process. The company has also been able to substantially shorten its commissioning times by using Siemens simulation software.
In Tower 9, the concentrated homogenized milk arrives from the mixing area at a pressure of 25 bar, is finely atomized and then pulverized by a hot air current as it drops. During this process, 663 digital and 637 analog sensors continuously capture relevant process data such as pressure and temperature levels. The required drive output is provided by 300 motors, and 1700 fans control the air currents. A plant of this complexity with all its different components calls for failsafe, reliable and sophisticated automation technology. The solution used is a standardized system landscape supplied by Siemens.
Reliable automation of a highly complex system
A total of ten Simatic S7 controllers and 64 Simatic ET 200SP distributed I/Os are used for closed and open-loop control of the overall process. These communicate using a ring structure Profinet network. Profinet is an open Industrial Ethernet standard for reliable network communication. Use of the “shared device” function enables two thirds of the I/O modules to be actuated by both types of controller, permitting flexible system configuration. Two failsafe Simatic S7-315F controllers are in charge of safety technology and ensure controlled shutdown of the plant in case of a fault. Visualization of all the different processes is performed using a Simatic WinCC Scada (Supervisory Control and Data) system and 16 thin client-based Simatic ITC 2200 operator stations.
Reliable advance testing using simulation
The Siemens solution partner Tophinke Automation & Gebäudetechnik AG, which was responsible for the automation, electrical planning and installation of the new production plant, used Simit simulation software to enable advance virtual testing of the complex functions taking place in Tower 9. “Our simulation process enabled us to trial the system virtually in-house at Tophinke, and so uncover any possible sources of software error before the physical installation took place,” says Heinz Thönen, Project Manager at Tophinke. This meant cutting the time needed for actual software commissioning by half.
For more information, visit HERE.