Industry Insights with Owen and Linda Caron, Global Product Manager, Factory Automation at Parker Hannifin
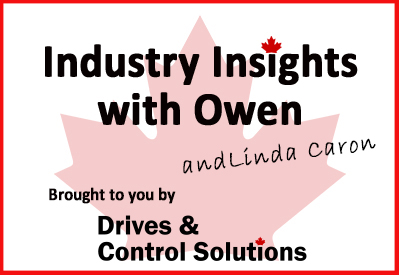
June 18, 2019
By Owen Hurst
In this issue of Industry Insights with Owen I had the privilege of asking Linda Caron of Parker Hannifin a few questions about the industry and how Parker Hannifin is addressing industry shifts and concerns.
Linda has over 20 years of experience working with technical products in the areas of industrial automation, robotics, mechatronics and electrical. After just a few minutes speaking with her the passion she has for her work is clearly abundant, along with her deep knowledge and understanding of the products and more generally the marketing of the industry. Not to mention that Linda is an exceptionally good writer that has published numerous articles (find links to Linda’s articles below).
We now dive straight into the valuable insights provided by Linda. Enjoy!
One primary trend among manufacturers today is to provide full solution offerings and services beyond that of a traditional product supplier, in your opinion how has this changed the industry and affected Parker Hannifin’s initiatives?
The shift in this trend has had a major impact in the way we are doing business in todays world. Rather than see us as a product supplier, we view ourselves as a partner and solutions provider, and, as such, we are committed to making it easier for our customers to do business.
One example where we have implemented this is with our Virtual Engineer program. This is an online tool which allows our customers to “self service” and size their systems. This tool is free, easy to use and allows our customers to review various options while selecting the product that best fits their specific needs. This represents a tremendous shift in the mindset of marketing products and how we engage with our customers.
In addition to launching online tools, Parker is also focused on how we can better improve our overall customer support. We have placed Controls Engineer’s in the field as sales support resources to better service our customers. Our process for product development has become more complex as we move from traditional mechanical products to mechatronic products that employ sophisticated electronics and embedded diagnostic capabilities. This enhanced level of field service is essential to our customer base as products become more sophisticated and as such; Parker continues to place tremendous investment in growing and developing our most valuable asset: our people.
Safety is a key focus when dealing with motion and control, are there any new directions products that you feel will increase operator safety? And where does the safety journey start?
Safety is our top priority. The safety journey starts with the user/designer of the equipment conducting a risk analysis to identify the most dangerous areas of the machine, so those areas can be addressed. Parker requires our plants to have Environmental Health and Safety (EHS) coordinators and teams to ensure this is being done. After our customers have done their own risk analysis, our sales teams can engage to help ensure they are using the right products to make the machine safe.
To support this strategy, we’ve expanded our portfolio to included dedicated safety rated products suitable for up to Category 4, performance level E and certified for the global market place meeting the Machinery Directives of many countries. Our commitment to safety doesn’t just end with our products. We also educate our distribution channel on machine safety, bringing machinery to a safe state and what is involved in conducting risk assessments on machinery. We also help to educate on properly sizing and selecting our products. We are committed to building the knowledge that is essential for reducing work place injuries.
Parker has a very interesting approach regarding its internal workings, allowing a great deal of flexibility and autonomy to its employees that has seen measurable results in innovation and safety. How essential do you see this type of policy for advancing not just Parker Hannifin but the entire manufacturing industry as a whole?
Parker has several driving factors in its business operations and “engaged people” is one of the most important. We trust in the knowledge and competence of our people and we always ensure they have a voice in decision making.
Our product development process called “Winovation” is an excellent tool with many stage gates of review before a product goes to market. We consider at each stage the opinions of our team members that include Operations, supply chain, value stream managers, mechanical, electrical and electronic engineers, marketing and product management among others. The decisions about a product vary at each stage of development and include safety considerations, certifications and testing to name a few.
A well-rounded product development strategy and deployment plan is essential for every company that needs to include the voice of its people. It’s amazing to bring a team of people together with varying skill sets and diverse backgrounds to solve problems and discuss next steps. No one mind works quite as well as our team of skilled people with high knowledge levels of varying parts of the operation.
Are there any new trends or insights for the future of motion and control technologies that you are currently excited about?
We are very excited about several new trends. Networked connectivity is a market driver. Companies are migrating away from hardwired connectivity and moving to networked solutions because of the ability it offers to monitor, connect and control the plant floor. Our goal and the basis of our product development has been to make this migration easy and cost effective.
The next evolution of this networked connectivity will be safety over network. Safety over network is a necessity to enhance operational efficiencies, reduce complexity and increase safety for plant personnel. This migration to a networked world is of significant interest for companies as they look to protect workers, reduce social costs and increase operational efficiencies.
Is there anything keeping you up at night right now?
According to OSHA statistics, more than 6,000 people die every year in the USA due to industrial related accidents and many of these accidents are easily avoided with the integration of basic safety fundamentals like bringing machinery to a safe state.
There is a lot of work to be done for companies working in the global marketplace to ensure that products and technology are certified in a uniform way that meet or exceed safety standards. One of the many challenges we see with regards to safety is the rapid evolution of products and technology across the globe. We recognize that we must all be able to respond quickly to these changing conditions, meet the certifications and requirements of each country which are often not harmonized and sometimes actually conflict while ensuring the products supplied are global, uniform and safe.
Further, network security is something that keeps us up at night. The worlds of IT and manufacturing are continuing to collide and ensuring our network products are properly secure is of the utmost importance.
Linda has also authored many articles, several of which can be seen here:
https://drivesandcontrols.ca/latest-news/4095-parker-hannafin-why-right-sizing-matters