New Mindsphere app from Siemens supports Predictive Services for Drive Systems
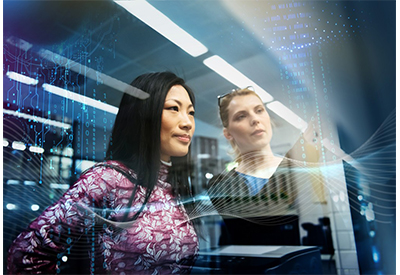
November 11, 2019
With Predictive Services for Drive Systems, Siemens presents a standardized extension to the local service agreement at this year’s SPS. This is based on the new Mindsphere Predictive Service Assistance app. It makes maintenance more efficient for Sinamics drive systems and/or Simotics motors in the low voltage range.
With the new service portfolio including Mindsphere app, Siemens is focusing on the operative demands of machine users, who are looking for full transparency for spare parts and servicing. Thanks to digital support via the Mindsphere app, Siemens can offer customers optimized service cycles, increased service efficiency, easy and streamlined documentation, plus full transparency for historical service activities.
Predictive Services for Drive Systems comprises a comprehensive service package where first a digitalization check is carried out and then the connection to Mindsphere is established. The Mindsphere Predictive Service Assistance app supports customers continuously by providing an overview of assets and service triggers, for example defined KPIs and operating hours based on predictive analytics. The app also offers transparency and detailed information for spare parts depending on the configuration of the drive system and for recommended and pending service work. In addition, it includes an assistant for planning, implementing and documenting maintenance activities and offers an easy ordering function via the Siemens ServiceMall and the Global Service Platform (GSP).
With Predictive Services for Drive Systems, customers benefit from increased productivity and reduced downtimes for their machines and plants. With support from the associated Mindsphere app, they can also enjoy full transparency for spare parts and maintenance activities to reduce risk through simple weak-point analysis. In addition, the app makes maintenance more efficient and streamlines the ordering process.
With digital services, Siemens is supporting digital transformation all the way through from consulting to implementation. The company is therefore assisting customers on the path to digitalization – from strategic consulting for industrial digitalization through to solution consulting to improve productivity.