Digitalization, AI, and collaboration revolutionize handling and assembly
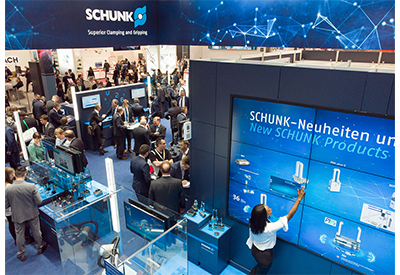
April 11, 2019
Humans playfully interact with robots, let lightweight robots grip objects with any geometry as granted, and rely on the fact that their own hand won’t be harmed by the robot’s powerful grip. Things that were unthinkable only a few years ago are now true, as seen at SCHUNK booth, the specialist for gripping systems and clamping technology at Hannover Messe.
“Digitalization, AI, and collaboration will revolutionize industrial handling and assembly in the years to come. At Hannover Messe you can recognize the outstanding significance of digitalization, automation, and AI in a global context and its high development pace,” emphasized Chief Executive Officer, Henrik A. Schunk at the end of the world’s leading industrial show.
Prime Minister Kretschmann is asking for creativity and courage
The family-owned company consistently focuses on the digital future. As the demanded supplier of mechanical clamping devices and gripping systems, the company developed from a “technology forge” with 3,400 employees to a trendsetting company in smart production. Winfried Kretschmann, the Prime Minister of the federal state of Baden Wuerttemberg visited SCHUNK at their show booth. “I am glad that SCHUNK, a company of the Federal State of Baden-Wuerttemberg is represented at Hannover Messe and that value awareness and pioneering spirit equally belong to their nature. We need creative entrepreneurs, who break new ground in times, where we are facing radical changes on the way to digitalization,“ underlines Kretschmann, and emphasizes “It makes me happy to see that SCHUNK, a family-owned global player, have asserted themselves at the interface between humans and robots for many years.“
Key topic human/robot collaboration
Within a very short time SCHUNK has developed a DGUV-certified product line of collaborative grippers for small components that can be combined with almost every available cobot in the market. By the end of the year the powerful SCHUNK Co-act EGL-C gripper will also be available. This gripper shatters the applied gripping force limit for human/robot collaboration of 140 N with the help of an intelligent, safe gripping process, and it is the first time that a workpiece weight up to 2.25 kg can be handled. The Co-act EGL-C also ensures safe gripping featuring a package of more than six safety functions – which is more than any other standard gripper offers in the market. Particularly, in view of ergonomic aspects, new margins for industrial use of cobots will open up, and will be very interesting for the automobile industry and their suppliers.
Artificial intelligence is gaining importance
SCHUNK and their partners are intensively working on a gripping solution that will open up autonomous gripping by robots. The groundwork is a tight interplay between image processing, planning of gripping scenarios, robots, grippers and safety. Instead of programming every movement in a laborious way, it is the aim that robots will be able to recognize objects by themselves, and to control and autonomously handle them in the environment of humans. Corresponding studies on the technology such as the autonomous gripping with the SCHUNK SVH 5-finger hand or a collaborative, self-optimized bin picking that was realized in cooperation with Roboception and KUKA, were available in the SCHUNK booth for testing them live.
Moreover, SCHUNK announced its cooperation with AnotherBrain, the world’s leading expert for artificial intelligence. Together they are going to develop intelligent gripping solutions that could autonomously act without requiring manual programming. Henrik A. Schunk is convinced that “this promising cooperation between SCHUNK and AnotherBrain will accelerate the progress in autonomous handling enormously.” From his point of view, companies will have to cooperate more closely in the future in view of the challenges of smart production than ever before. “Smart processes require a close coordination of all the involved disciplines, and this was clearly evident at Hannover Messe,“ emphasized Schunk. “Particularly, users, integrators, and machine builders will benefit from this. In the future, they will receive many more intelligent solutions from one source.“