Fluke: Pyrometers for High Temperatures and Various Fieldbuses
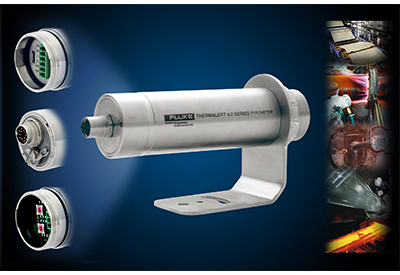
October 27, 2020
Fluke Process Instruments extends its Thermalert 4.0 spot pyrometer series, adding new shortwave versions and various additional interface options. The compact, extremely robust infrared thermometers provide noncontact, automatic temperature monitoring. Three new spectral models measuring at wavelengths of 1 µm, 1.6 µm, and 2.3 µm have been primarily designed for high-temperature applications and are particularly suitable for monitoring metal, steel, and glass. The full Thermalert 4.0 lineup covers measuring temperatures between -40 °C and 2300 °C and offers various different spectral models and focus distances.
All models are now available with connectivity options for Ethernet, EtherNet/IP, and PROFINET IO, in addition to analog or RS485 interfaces. Voltage can be supplied via Power over Ethernet (PoE). The Thermalert 4.0 series features an outstanding high maximum operating temperature of 85 °C. Users can therefore save costs by setting up many measuring points without cooling. The rugged IP65 infrared thermometers exhibit best-in-class repeatabilities, response times, and accuracies. An integrated laser focus facilitates alignment. In addition, the manufacturer also offers a pyrometer without laser for particularly cost-sensitive applications.
This model with an 8 µm to 14 µm spectral response has all the other advantages of the series and is suitable for a wide range of measurement tasks between -40 °C and 1000 °C.