HANNOVER MESSE: Drive Systems Evolved
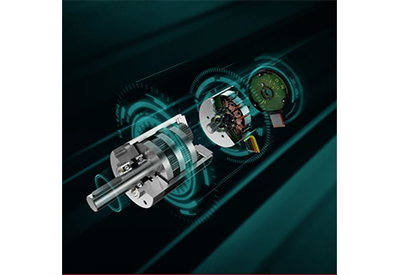
April 20, 2021
Most users do not need individual motors to realise their drive solutions. They are better off with complete drive systems in which the individual components are perfectly matched to each other. A solution is now available for applications where installation space is extremely limited and where high-torque drives are required which, owing to the installation situation, need to be as short as possible in the axial direction.
The drive specialist FAULHABER has used its many years of experience as a system provider and has recently extended its BXT flat motor series by adding matched gearheads as well as integrated encoders and speed controllers that are also exceptionally short in the axial direction. Typical applications for the compact drive systems can be found e.g. in robotics, prosthetic joints, laboratory automation, pumps, medical technology or aircraft cabin equipment.
Thanks to innovative winding technology and an optimised design, the motors are just 14, 16 and 21 mm in length but deliver torques up to 134 mNm, within a diameter of 22 mm, 32 mm and 42 mm respectively. For precise speed control or in the case of high requirements on positioning accuracy, diameter-compliant magnetic encoders or speed controllers are now fully integrated into the housed motor variants, whereby the drive is increased by just 6.2 mm. The matching metal planetary gearheads of the GPT series too are characterised by a short design, high torque and extremely fine graduations of the numerous reduction ratios.