Exploring The New CDS Series Clean Motor Disconnect
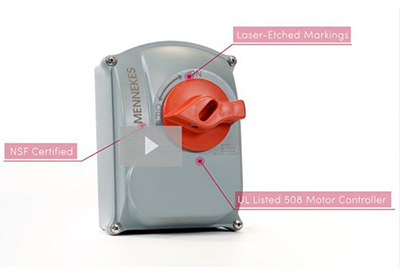
November 16, 2020
You will find requirements for line-of-sight motor disconnects in all plant environments. That’s why Mennekes have designed their new CDS Series to withstand demanding operating conditions, especially in food, beverage and pharmaceutical applications.
What’s New
Mennekes’ 30 Amp CDS Series is the industry’s first curved, non-metallic motor disconnect. Its unique shedding design eliminates standing water, debris and other contaminants. Because you can’t run power into the top, you also avoid risks like water ingress and condensation.
To mount the CDS Series, you have two options. The first is with external mounting feet. When positioned in a vertical orientation, the unit matches Hubbell’s HBLDS3 footprint, making upgrading to the CDS quick and easy. Second, an internal mounting option maintains the legacy footprint of our MS1A enclosures. Units also feature easy-to-read, laser etched markings and are rated for demanding environments:
- – NSF Certified
- – UL Type 4X and IP69K
- – Robust 20 HP at 480V rating
- – SCCR rating—65,000 AIC with Class J Fuse
If you don’t need a curved top or you require top entry, the DS Series satisfies that need with 25, 30 and 40 Amp variants. Best of all, both series have many of the same features as Mennekes’ legacy disconnects, including impact-resistant VALOX enclosures, stainless steel captive cover screws, highly visible handles for LO/TO, top-position early break auxiliary contacts—and many more.