ABB Signs MoU with EVE Energy to Support Sustainable Greenfield Battery Manufacturing Globally
September 26, 2024
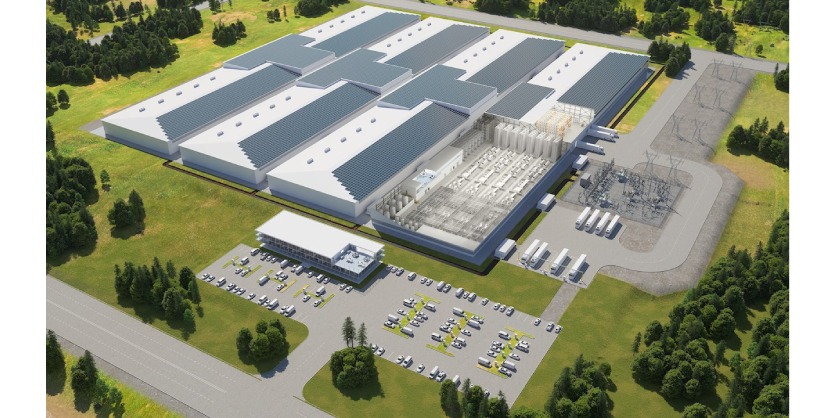
- ABB has signed a Memorandum of Understanding (MoU) with Chinese battery cell manufacturer EVE Energy
- The companies will work together to enhance battery production operations, improve safety standards and deliver energy-efficient solutions in line with lithium battery demand
- ABB will support in the design and operational efficiency of new plants for rapid time-to-market battery manufacturing
ABB has signed a Memorandum of Understanding (MoU) with EVE Energy Co., Ltd. (EVE), a global lithium battery cell manufacturer, to support the development of new, sustainable lithium battery factories in locations worldwide. The agreement, founded on EVE’s ‘Global Manufacturing, Global Delivery, Global Cooperation’ capability system, aims to improve efficiency, meet project timelines, and enhance overall productivity and profitability, thereby addressing the evolving challenges and requirements in the lithium-ion battery manufacturing industry.
With EVE set to open new factories globally in the coming years, ABB will collaborate with its project teams for the design and construction and share its expertise in the greenfield battery manufacturing space. The company will support EVE’s initiatives in line with its pillars for success: electrical, instrumentation, control and digital (EICD) integration, Adaptive Execution™, and efficient ongoing operations. According to the MoU, the two companies will also collaborate on research and development (R&D) and explore the supply of battery cells, modules and packs to ABB.
EVE has more than 23 years of experience in lithium battery innovation and an established presence in the Internet of Things (IoT) and energy sectors. The company’s product portfolio involves primary lithium batteries, small lithium-ion batteries, power batteries and energy storage batteries. EVE is currently building its first European plant in Hungary to supply the region’s automotive sector and has plans in place for other sites, expanding on its existing footprint in China and the US.
The global lithium-battery manufacturing industry is evolving in response to increasing clean energy demands. Alongside this growth, the industry faces several challenges, including improving quality while reducing off-spec material, enhancing throughput, managing cost pressures and decreasing battery prices, and ensuring safety and environmental responsibility. ABB’s Plant Optimization Methodology is designed to combat these challenges at project inception, helping to design, equip, and operationalize new plants for more efficient operations.
“Our collaboration with ABB will be invaluable to this project, enhancing the efficiency and safety of our greenfield battery factories,” said Steven Chen, SVP of EVE Energy, CEO of EVE Energy Storage. “We are looking forward to working with ABB on the design and implementation of solutions for optimized battery manufacturing operations, contributing to the ongoing efforts towards sustainable energy production.”
“Securing steady and reliable battery supplies is one of the most pressing challenges faced today,” said Staffan Sodergard, Global Business Unit Manager for Battery Manufacturing, ABB Process Industries. “Expanding global capabilities to manufacture high-quality lithium batteries is a crucial part of this energy transition. EVE not only recognizes this but has risen to the opportunity to optimize and streamline operations across these new sites. Bringing our industry expertise, ABB will help EVE to answer growing demands in a cost-effective and efficient manner.”
The integration of EICD technologies is designed to create comprehensive, optimized solutions that enhance every phase of project execution. Among these efficiencies is the indispensable need to ensure worker health and safety. By automating and streamlining these systems, ABB minimizes risks and reduces interface complexity, ensuring a seamless and efficient process from design to implementation. ABB’s Adaptive Execution approach transforms both physical and digital activities, delivering standardized global projects while keeping CAPEX to a minimum.
Covering the entire battery manufacturing value chain, from materials sourcing to production and recycling, ABB’s end-to-end solutions include ABB Ability™ Manufacturing Operations Management (MOM) and ABB Ability™ Energy and Asset Manager, which provide comprehensive visibility and control over manufacturing processes and energy consumption. These tools will enable EVE to optimize production, reduce energy usage, and ensure the highest quality standards.
Related Story
ABB To Support Canadian Refiner in Transformation of Conventional Crude Oil Facility into Renewable Fuel Production Site
ABB has been selected by Braya Renewable Fuels to support the transformation of the idled Come By Chance oil refinery in Newfoundland and Labrador, Canada, into a state-of-the-art renewable fuels production center. Braya Renewable Fuels is focused on powering the decarbonized future of the heavy transportation sector, a critical component of the global economy, and is seeking to complete the Phase one conversion project and begin producing renewable diesel in late 2022 with initial nameplate production capacity of up to 18,000 barrels per day.