Yaskawa: Matrix Drives Reduce Energy Costs for Asphalt Transport System
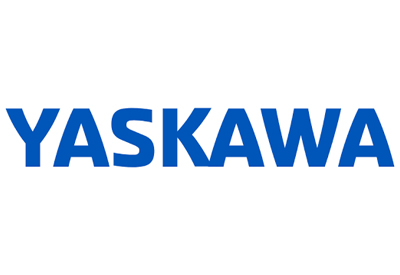
March 29, 2019
Application Overview
A material handling application is generating about $1,500 per year in electrical savings rather than dissipating the regenerative energy as heat. Additional equipment life cycle savings are also anticipated as a result of the simplified electrical and mechanical designs. These benefits are realized because of the application of the U1000 Industrial Matrix Drive.
In spring 2016, Maxam Inc. of Kansas City, MO and Yaskawa America Inc. developed an asphalt transporter system for Gallagher Asphalt in Thornton, IL. The Maxam Transporter™ asphalt mass transfer system is a fully integrated asphalt distribution product that is designed to fill and evenly distribute asphalt into individual load-out silos. The Gallagher Asphalt system’s motor-driven transporter features an 8-ton high-speed material transfer vessel and recharging storage vessel.
Retrofitting the System
conveyor systems and their inefficient motors were removed and eliminated from the original transporter system. The old drag slat system was a steel floor conveyor that used chains and required additional power due to conveyor plate heating. The existing 200-ton asphalt storage silos were retrofitted with the asphalt transport system. The new transporter replaced a complex system of asphalt material conveyors. Five 40 hp
Matrix Drive Solution
The Maxam Transporter system uses two Yaskawa U1000 Industrial Matrix drives, which utilize direct AC to AC conversion. One drive operates the 60 hp, multi-motor powered carriage and a second 30 hp drive operates the transfer vessel power train. The main carriage has four drive motors and the moving vessel (batcher) has two additional motors. The main carriage and the vessel need to be driven at exactly the same speed. The new and innovative system is designed to be more energy efficient and provide a more maintenance-free, mechanically integral asphalt distribution system.
How Matrix Drives Increase Energy Efficiency
This transporter has been operating since February 2016. The duty cycle requires the motors ramp to full speed in 1.5 seconds. The motors will operate at full speed for about 4 seconds, then decelerate to stop in about 3.5 seconds. The system repeats the process every 10 seconds. During the fast stop time, the transporter motor’s regenerative load energy normally would be channeled into the AC drives’ separately mounted dynamic brake switching and connected resistors. The regenerated energy would then be dissipated as heat energy. Since the regenerative cycle occurs during about 20% of the total duty cycle time, significant amounts of energy would be lost as heat.
The direct AC to AC U1000 Industrial Matrix drive works for this application because of its control technology. It employs a system of 9 bi-directional switches arranged in a matrix to convert the three-phase AC input voltage directly into a three-phase AC output voltage. This state of the art AC drive topology eliminates the need for a traditional AC drive’s rectifying circuit, DC smoothing circuit, and even the remote mounted dynamic braking components usually required for this type of application.
The drive uses all three input phases in pulse width modulation (PWM) switching to control output voltage and input current. But it also provides regenerative motor control operation. This regenerative control is required when the carriage and vessel motors decelerate. This allows the Matrix drive to recover the otherwise lost energy by regenerating the motor’s overhauling energy power directly back into Gallagher Asphalt’s power distribution system. This is much more efficient than releasing the motor’s regenerative energy as heat into the traditional AC drive’s dynamic braking option.
Reduced System Complexity
The motor control centers (MCC) for the transporter systems are installed in outdoor-rated enclosures. Considerations for the limited MCC panel space, dirty, and wet weather environments along with wide ambient temperature fluctuations are important design criteria for this motor control solution. MCC wiring complexity is simple with the direct AC to AC matrix drive topology. Wiring requires little panel or field installation labor. The drive provides a three-phase power supply input and three- phase output main power supply wiring. The main motor power circuit component count is reduced from several components to one. Using the Matrix drive allowed the motor controller panels to be about 70% smaller than the traditional AC drive with the dynamic brake module and resistor solution or a traditional AC drive regenerative power supply solution.
Actual Cost Savings
Gallagher Asphalt applied for a Commonwealth Edison utility grant because of the energy savings offered by the Matrix drive. Gallagher’s KWh costs are .076 cents/KWh. Operation cycle time is 8.5 hours per work day, five work days per week with an average of 40 weeks a year of system operational time. Approximately 20% of the total run time is spent in regenerative mode. This is 340 hours/year. Assuming each motor is at 100% braking torque during regeneration, the 30 hp drive’s total motor load will yield approximately $500/year and the 60 hp drive’s total motor load will yield approximately $1,000/year of energy savings (based on $0.076/kwh). This is compared to a typical motor control solution using a conventional AC drive with a dynamic braking resistor option.
Visit https://www.yaskawa.com/