Sanitary Conveyor Manufacturer Opts for Invertek Optidrive NEMA 4X VFDs for Improved Motion, Control and Communication
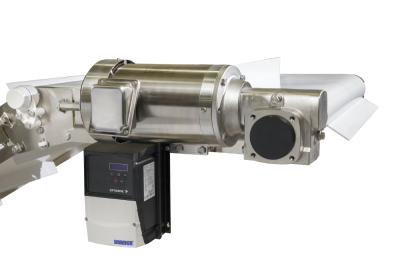
March 4, 2022
A global manufacturer of sanitary conveyor systems used in food and pharmaceutical industries recently began exploring the next generation of variable frequency drive technologies available to power its platforms. A need for better communications for IoT and remote access, improved quality and reliability, and global access to supplies were critical to ensuring the manufacturer could satisfy its customers. This is where Invertek Drives and its Optidrive E3 NEMA 4X / IP66 range of VFDs came in.
U.S. based Dorner is a global leader in the design, applications, manufacturing and integration of conveyor systems. Its AquaPruf and AquaGard platforms are engineered specifically for industries that require their conveyors meet the highest level of sanitary standards for their applications.
These platforms can be disassembled with no tools by one person, cleaned, sanitized and reassembled in about 10 minutes. Dorner’s sanitary designs represent real-time savings for customers. Dorner’s AquaPruf conveyors are used every day in industries including baking, meat, poultry, confectionery, pharmaceutical and many others. The need to clean or washdown conveyors regularly meant any VFD used would have to have a NEMA 4X / IP66 enclosure.
“We were searching for new VFD technology as our existing motor control solution was ‘old technology’, albeit a proven unit we had used successfully for 10 years, it was long-in-the-tooth from a standpoint of component make-up,” said Scott Grahl, Engineering Manager, New Product Development at Dorner. “Additionally, we were looking for a design that has the proven ability to seamlessly power either AC induction or synchronous permanent magnet motor designs, as well as having built-in communication capability to tie into an IoT or remote interface system.”
The company evaluated several VFD options before selecting Invertek Drives’ Optidrive range.
“Although there are many choices in the area of VFDs, Invertek’s met our requirements with a quality product and cost-effective offering,” Grahl said. “Additionally, the NEMA 4X enclosure means they can be directly mounted on the conveyors, saving space and the need for a separate cabinet.
A need for NEMA 4X / IP66 rated enclosures for harsh conditions
The conveyors can carry loads up to 20 lbs per square foot at speeds up to 100mpm. Dorner chose the Optidrive E3 NEMA 4X / IP66 to control the 1.5kW (2HP) 7A, motors used. The E3 has Bluetooth connectivity along with Modbus RTU and CAN on board as standard. Its compact and robust design makes it suitable for a variety of applications, including conveyors. It is also easy to set up and commission.
The Optidrive E3 is available in IP20 and NEMA 4X / IP66 enclosures, making it ideal for harsh conditions or where hygiene is important and washdown is required, such as in food and beverage. Dorner conveyors meet industry-recognized standards, including the coveted Baking Industry Sanitation Standards Committee (BISSC) certification, which is the definitive sanitation standard for equipment used in the baking industry. The conveyors meet U.S. Department of Agriculture (USDA) standards as well, and they use FDA approved materials and components.
Pete Roberts, National Sales Manager at Invertek Drives USA, said a combination of design, reliability and global accessibility were key to winning the order from Dorner. “Dorner came to us with a list of requirements that would ensure their conveyors would remain one of the best on the market. In-built communication was just one requirement, and this would future proof its products for IoT and remote monitoring,” Roberts said.
Efficient and reliable conveyor system
“We knew the partnership of Dorner and Optidrive would create an efficient and reliable conveyor system for its customers. The design of the drive, including the ability to have NEMA 4X / IP66 enclosures was also ideal for applications where washdown is required for hygiene, such as food industries.”
“In addition to the quality of the product, we knew Invertek had a strong existing customer base and history in the market,” Grahl said “Its presence in manufacturing and distribution was also a key point as Dorner is also a global product provider and having a supplier in the same position is important for us.”
The Optidrive E3 is part of Invertek Drives range of easy to use and set-up VFDs. The E3 includes simple commissioning, with 14 parameter basic set-up, default settings, and up to 50 parameters available for flexible use. It comes with an intuitive keypad and application macros for switching between industrial, pump, and fan modes, depending on the application being controlled.
More details about the Optidrive range of VFDs can be found here
More details about Dorner and their leading-edge conveyor systems can be found here