How Distilleries Can Maximize Throughput Without Sacrificing Quality
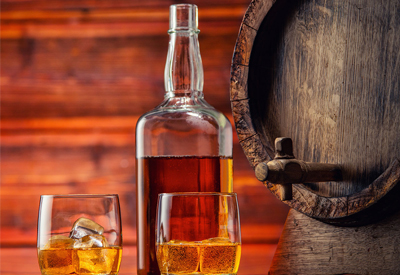
December 17, 2018
By: Kent Stephenson, Rockwell Automation
Between 2009 and 2016, the number of distilleries in Kentucky tripled, primarily due to the worldwide growing interest in bourbon whiskey and an increased appreciation of craft cocktails. Due to this surge in demand, U.S. distillers are scrambling to identify and adopt methods for maintaining quality while increasing efficiency and throughput.
Over the next three months, you’ll be able to read how the spirit industry’s growing pains are moving companies to improve performance across their process. The issues they’re targeting today vary from removing bottlenecks to improving yield and quality.
To create what becomes bottled spirits, grains are milled and cooked to release fermentable sugars. Yeast is then added, and the cooked grains are fermented, producing alcohol. The fermented grains, known as distiller’s beer, are distilled either in batches or continuously, one or more times, to produce the spirits. Lastly, depending on the type of spirit being produced, they’re stored in barrels to age, or diluted to the desired strength and bottled for consumers.
With this context in mind, let’s focus on the continuous distillation process. How can processors alleviate issues like maximizing throughput, minimizing alcohol loss, improving the operator’s ability to focus on value-added tasks, while maintaining their traditional recipe?
Technology like model predictive control (MPC) can help operators push against process constraints and freely adjust what they’re doing to optimize production. Throughout production, MPC prevents over-correction and constantly makes necessary adjustments to maintain steady measurements of steam, temperature, materials and pressure.
Technology like model predictive control (MPC) can help operators push against process constraints and freely adjust what they’re doing to optimize production.
Maintain Tradition and Quality
When it comes to implementing MPC in distillation, the primary concern companies have is maintaining product consistency. And understandably so, since their unique process has been around for centuries. When the process doesn’t follow their recipes, you just don’t have the same end-result.
For years, the spirits industry ran consistently with the technology and equipment in their facilities. Now, with the ongoing boom, there’s pressure to make improvements to compete against demand. As a result, operators are moving from manual to automated distillation, which can help eliminate inconsistencies that negatively impact product quality.
The distillation process involves many opportunities for optimization, beginning with the amount of feed to stills, which ultimately determines throughput. Along the way, optimization can also occur in relation to steam flow, reflux flow and other parameters.
Since controlling the process at one part of distillery will have an impact on other parts, operators know that if they make one adjustment, they must also make additional adjustments down the line. MPC helps maintain consistency and can even predict what adjustments will be needed, before they’re required, resolving process interactions before they create disturbances, which ultimately helps to ensure quality throughout production.
For example, in bourbon production, if more feed is added to the beer still, operators know to change the steam and reflux at the beer still and to change the feed and steam going to the doubler. In these situations, operators can rely on MPC to manage the material balance in the distillery, while also maintaining the quality targets.
Added Value Tasks
With MPC managing minute details and adjustments, operators have time to focus on high-level tasks around the plant, like running tests and monitoring trends. While technology handles the details, operators can dedicate time to the big picture, make observations and anticipate issues.
These value-added tasks are key because they have a financial impact on the plant and involve tasks that make use of operator eyes, ears and years of experience in the distillery.
If an operator spots an issue ahead of time, the situation can be managed and corrected in a timely manner. For example, if the operator notices potential equipment failure, that creates an opportunity to repair the equipment during production or during a scheduled maintenance outage. This is extremely valuable from an economic and production standpoint because resolving challenges in advance avoids shutting down production and unplanned downtime.
Overall, MPC answers the call for quality control and tradition in the distillation process. By continuously manipulating the process, it’s possible to maintain quality targets and to confirm adherence to the traditional recipe, while also maximizing production and making operators more effective.
If you want to learn more about the benefits of MPC in the spirits industry, read here.