Transport and Positioning Perfected: Linear Motor-Driven Transfer Systems from Rexroth
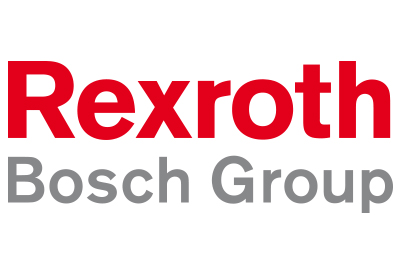
July 9, 2018
With its ActiveMover and FTS systems, Bosch Rexroth serves a wide variety of work specifications
For the highly dynamic transport and exact positioning of materials and workpieces, linear motor-driven transfer systems are the first choice. Bosch Rexroth is enriching this market segment with two innovative solutions at once, and can therefore meet the specific requirements of series and special machine manufacturers alike. Customers looking for a quickly applicable system for short-cycle applications will find the perfect execution in ActiveMover. Those who require a high degree of freedom in design and programming, however, should opt for the flexible transport system (FTS), which, due to its modular principle, can be scaled individually.
Whether a fast-running system with which the first transport cycle can be completed within half a day, or maximum freedom for implementing the most demanding applications – Bosch Rexroth offers transfer systems for every customer requirement. Both systems are based on Rexroth’s many years of know-how and experience from numerous successful projects in a variety of industries.
The standard for short cycles: ActiveMover
From the automotive and healthcare industries to electronics production and clean room applications – wherever products must be transported quickly and precisely, ActiveMover is at the start. The closed transfer system is specially designed for short-cycle applications and is particularly impressive with its unique combination of speed, precision and load-carrying capacity. The ActiveMover accurately detects the position of the workpiece pallets through an integrated measurement system, making the use of additional sensors superfluous. The guide system is also integrated, which reduces construction effort to a minimum and enables fast design. In practice, the ActiveMover scores with a high repeat accuracy of up to 10 µm, speeds up to 150 m/min and high acceleration. On the connection side, the transfer system is open for any controls and, as a complete system with limited engineering effort, is aimed in particular at special machine manufacturers that focus on large quantities with short cycle times.
Precise, scalable, adaptable: the flexible transport system (FTS)
As a modular system based on components, the FTS can be flexibly and easily integrated into systems and machines. This offers the user full flexibility, both in the selection of motors and drives as well as in programming of individual and synchronized movements. With its contactless drive, the intelligent system can adapt to a number of different production conditions. Through its magnetic principle of operation, the FTS also meets extreme requirements in a high vacuum, as all the electronics are located outside the vacuum. But the FTS also operates with high precision in robust environments with dust and dirt generation. This makes it attractive for a large number of fields, ranging from the semiconductor industry to battery production, where the FTS demonstrates its special handling characteristics and easily copes with loads of over 160 kg per carrier. Combined with a repeat accuracy of up to 1 µm and speeds up to 5 m/s, the FTS is optimally equipped for many applications.
Another unique feature: the FTS is also ideally suited to very low speeds, for example in coating processes, and due to its motion control functionality, reaches a maximum speed ripple of 2% at 20 mm/s.
For more information HERE