Comprehensive Guide to Preventing Premature Motor Failure
July 9, 2025
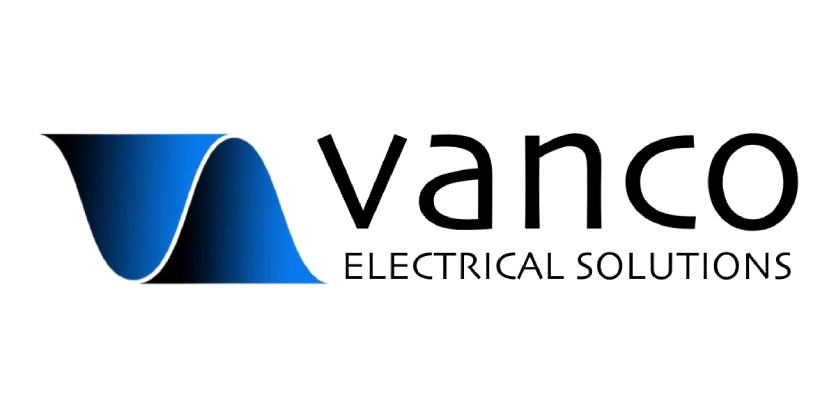
Electric motors are the workhorses of modern industry, driving pumps, fans, compressors, conveyors, and more. Yet, despite robust mechanical designs, many motors experience unexpected downtime due to hidden electrical stresses. This guide dives deep into the mechanisms of premature failure, empowers you to assess vulnerabilities in your installations, and provides a layered mitigation roadmap, drawing on industry standards, academic research, and real-world best practices.
Before diving in, check out this concise video introduction on motor protection from MTE:
1. Understanding Failure Mechanisms
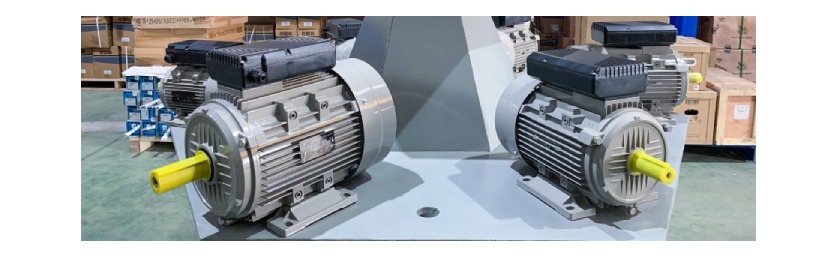
1.1 Bearing Electrical Damage
- Common-Mode Currents: Variable frequency drives (VFDs) generate non-zero common-mode voltages that induce high-frequency currents through motor windings and parasitic capacitances. These currents preferentially discharge through bearings, causing microscopic pitting and frosting. Over time, this leads to fluting patterns and rapid bearing wear.
- Key Statistic: Bearings account for roughly 50–60% of motor failures in VFD-driven applications (Industry Reliability Consortium, 2023).
1.2 Insulation Degradation
- dV/dt Stress: Insulation systems are rated for specific voltage rise times. Rapid switching (rise/fall times under 500 ns) leads to reflected wave overvoltages, which can exceed the dielectric strength of turn-to-turn and phase-to-phase insulation.
- Thermal Effects: Partial discharge events generate localized heating, accelerating breakdown of varnish and insulating paper.
1.3 Harmonic and Thermal Stress
- Harmonic Distortion: Non-sinusoidal motor currents produce eddy losses in the rotor and stator core, increasing operating temperatures by up to 10–15% under heavy load.
- Mechanical Resonance: Vibration frequencies matching structural natural frequencies can amplify mechanical loads, compounding electrical damage.
1.4 Environmental Factors
- Contaminants: Moisture, dust, and corrosive chemicals reduce insulation resistance and accelerate bearing corrosion.
- Temperature Extremes: High ambient temperatures can reduce lubricant film thickness, making bearings more susceptible to electrical erosion.
2. System Assessment: Diagnosing Vulnerabilities
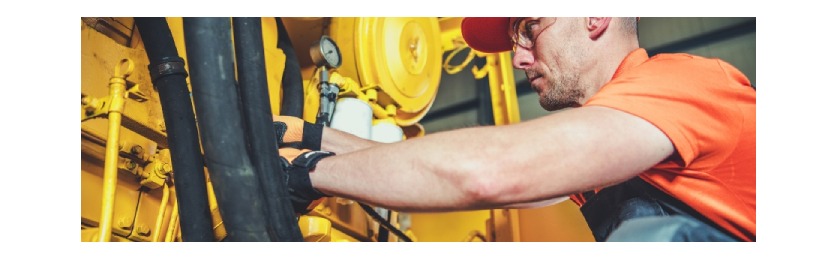
- Cable and Drive Analysis
- Measure cable length and shielding. Unshielded or unterminated cables over 50 m (164 ft) significantly increase reflected wave amplitudes.
- Document drive switching frequency and modulation scheme (e.g., space-vector vs. sine-triangle PWM).
- Ground Path Inspection
- Perform a grounding clamp test to validate low-impedance paths. Ideal <0.1 Ω from motor frame to earth ground.
- Inspect for loose grounding lugs or corroded connections.
- Thermal Imaging & Vibration Monitoring
- Use infrared cameras to spot hotspots in windings and bearings.
- Conduct vibration analysis (ISO 10816) to measure bearing-related frequency components.
- Electrical Waveform Capture
- Utilize high-voltage differential probes and current clamps to record common-mode voltages and currents at motor terminals under load.
- Historical Failure Data
- Review maintenance logs for patterns of bearing or winding failures, correlating with duty cycles and drive configurations.
3. Layered Mitigation Strategies
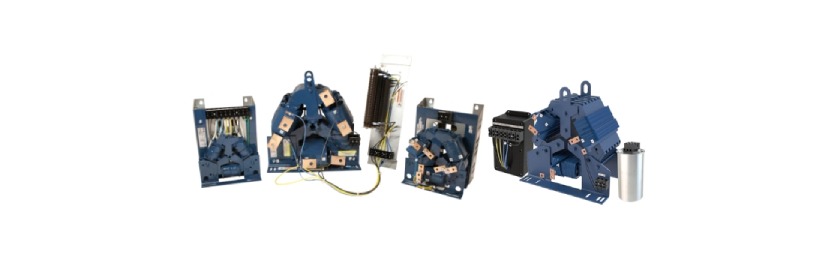
3.1 Electrical Filtering Solutions
- dV/dt Filters: Limit voltage rise times to <1,000 V/µs, reducing reflected overvoltages by up to 40%. Ideal for medium-length cable runs (<100 m).
- Common-Mode Chokes & Isolation: Combine with capacitive filters to attenuate common-mode currents by over 90%. Standard in long cable applications (>100 m).
- Sinewave Filters: Deliver near-pure sine outputs, eliminating most high-frequency content; recommended for sensitive loads or critical uptime environments.
3.2 Bearing Protection Devices
- Shaft Grounding Rings: Provide a dedicated discharge path for shaft currents, capturing >95% of bearing currents.
- Insulated Bearings: Electrically isolate bearings from the shaft, preventing current passage through bearing raceways.
3.3 Cable and Installation Best Practices
- Use VFD-Rated Cables with ≥100 pF/m capacitance control and braided shields bonded at both ends.
- Route Power and Control Cables Separately to minimize EMI coupling.
- Twist Pair Conductors in motor cabling to reduce loop area and common-mode generation.
3.4 Power Quality and Supply Conditioning
- Active Harmonic Filters: Mitigate voltage and current harmonics to maintain THD <5%.
- Line Reactors: Provide delta-wye conversion and impedance to smooth current draw.
- UPS and Voltage Regulators: Protect against sags and transients from upstream supply.
4. Monitoring, Maintenance, and Validation
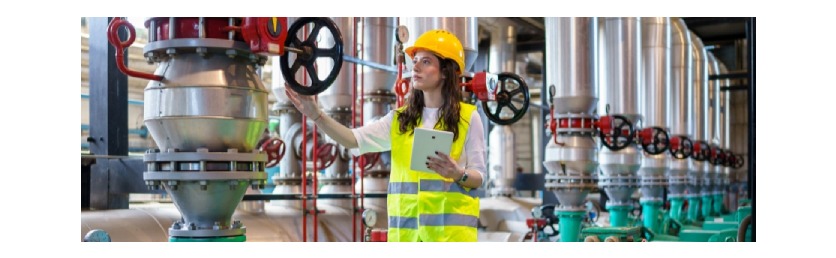
- Continuous Monitoring
- Install permanent sensors for bearing currents, vibration, and temperature.
- Use SCADA/IIoT platforms to set alarms and trend analysis.
- Preventive Maintenance Schedule
- Monthly: Visual inspection of filters, cables, and grounding devices.
- Quarterly: Electrical waveform capture and thermal scans.
- Annually: Comprehensive vibration analysis and insulation resistance testing (IEEE 43).
- Performance Validation
- Conduct before-and-after filter / grounding installation tests.
- Compare common-mode current measurements to baseline; aim for >50% reduction.
- Training & Documentation
- Develop clear SOPs for installation, testing, and troubleshooting.
- Train technicians on interpreting waveform and vibration data.
5. Filter Testing Results (Real‑World Data)
Configuration | Peak-to-Peak Voltage | Common-Mode Current | RMS Current |
VFD Only (No Filter) | 2,770 V | High | 1.10 A |
+ Load Reactor | 1,950 V | Minimal change | 0.90 A |
+ dV Sentry Filter | 1,850 V | Reduced peaks | 0.40 A |
+ microNexus® Filter | 1,250 V | Nearly eliminated | 0.02 A |
These data underscore the progressive benefits of MTE filters in both waveform quality and bearing current reduction.
Key Takeaways & Next Steps
- Bearings are the leading failure point: electrical stresses play a major role.
- Differential and common-mode mitigation are critical for long cable runs and sensitive applications.
- MTE filters (dV Sentry, SineWave Guardian, Nexus) offer demonstrable performance gains.
By systematically applying these insights and solutions, maintenance teams can transform hidden threats into predictable, manageable risks that extending motor life, optimize performance, and reduce unplanned downtime.
Document prepared as an educational resource for reliability and maintenance professionals.
Related Story
Vanco’s MTE Instant Lookup Tool: Your Shortcut to Finding the Right Product
Finding the correct MTE product shouldn’t feel like solving a puzzle. At Vanco, they know how frustrating it can be to juggle voltage specs, enclosure types, and part numbers while racing against project deadlines. That’s why they built the MTE Instant Lookup Tool, a streamlined, intuitive solution designed to cut through the clutter and deliver exactly what you need in seconds.
Vanco breaks down how it works, step by step.